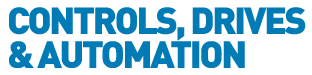
![]() |
Charlotte Stonestreet
Managing Editor |
Home> | MACHINE BUILDING & ENGINEERING | >Machinery Safety | >Safeguarding cardboard feed |
Home> | AUTOMATION | >Sensors | >Safeguarding cardboard feed |
Safeguarding cardboard feed
30 August 2022
IN TRAY forming applications, during normal operation cardboard blanks queued for processing act as a movable guard. If the material feed runs empty, though, the operator can reach unhindered right inside the tray former – which constitutes a significant hazard.

That’s why, on tray formers from Sema Systemtechnik, two Pilz diffuse sensors keep a permanent eye on the feed opening. If there are no blanks left in the feed, the safety function triggers an immediate stop to the hazardous movement. The TÜV-Süd-certified solution, consisting of a configurable safe small controller PNOZmulti 2 and special diffuse sensors with background suppression, ensures that the tray formers of Sema Systemtechnik meet the very highest safety requirements. The safe solution removes the need for 'fixed' guards in the feed area.
Outer packaging or cup trays made of cardboard carry a huge range of articles. Their design depends both on the form and size of the product and on the requirements made of the respective production and logistics processes. Since outer packaging is now also used for presenting merchandise, individual handling and design requests from the product manufacturers have to be factored in as well. That means modern tray formers need to offer high levels of flexibility; cassettes that can be exchanged quickly and easily enable format changes at ultra-fast speed.
Digitalisation has long since arrived in the packaging sector. Powerful control systems have come to replace relay-based hardware, and modern safety concepts are being implemented to provide the best possible protection while neither hindering flows nor encouraging operators to engage in manipulation. Digitalised processes have made flows more efficient, handling easier and breakdowns rarer.
Based in Hüllhorst, near Bad Oeynhausen, Sema Systemtechnik has been manufacturing plant and machinery for the semifinished goods and packaging industry for more than 35 years. It focuses on machines for the packaging, transportation, palletising, straightening and re-packing of primary packaged products, especially for the dairy industry. With a workforce of around 100, the SME offers a comprehensive portfolio of services extending from design through manufacture to commissioning and line integration.
Flexible product adaptation
A tray former such as the 1200 s model from Sema Systemtechnik, which has an overhead servo drive and large-surface panel cladding, outputs up to 60 trays per minute. The compact machine is a flexible-format system with short change-over times. “It’s essentially a standard product which we have adapted to meet the relevant customer requirements and offer as a stand-alone or fully integrated machine,” says Thomas Wehrhahn, who is responsible for hardware design at Sema.
To demonstrate, Wehrhahn places prepunched blanks in the feed magazine: The machine starts when the stack has reached a depth of at least 80 millimetres. The vacuum-driven puller pulls the cardboard blanks in and presses them onto the carrier of a toothed belt. The blanks are then folded, glued and sealed in a number of steps at one-second intervals. Once formed, the trays are carried on a conveyor either directly to the filling station or for onward transport.
As long as multiple cardboard blanks cover the feed opening, the operator is unable to reach into the danger zone while the machine is running. Since many blanks are smaller than the opening of the tray former, the area not covered by the blank is sealed by a Plexiglas pane made to the precise contours. This is replaced without the use of tools and scanned by coded, manipulation-proof RFID sensor safety switches PSENcode from Pilz.
It became clear from the risk analysis that an effective security solution restricting neither the operator nor the process had to be found for the case that there is “no cardboard in front of the feed opening.” Sema opted for an integrated, TÜV-Süd certified safety solution from Pilz. “We have been relying on the robust and reliable products from Pilz for more than ten years already. What’s more, many of our customers don’t want to see safety and security solutions from anyone other than Pilz in their machines,” emphasises Thomas Wehrhahn.
The advantage of this solution is that the safety function is realised with the devices of the PNOZmulti 2 family, which means it can also be implemented in existing applications. In addition, multiple cardboard feeds can be monitored with just one base unit. Only the necessary hardware inputs and outputs have to be considered in the configuration. The function blocks for the evaluation are included in the PNOZmulti Configurator V11.0, which does not require a licence fee, and its predecessor versions.
Two diffuse sensors at the material feed permanently monitor the presence of cardboard blanks. The sensors have to be located 30 mm to 100 mm away from the cardboard stack, which allows flexibility in positioning. They can be mounted on the side or, as in this case, on the top of the feed opening, a useful option enabling them to detect all formats processed on the machine and ensuring they do not obstruct the insertion process. If the sensors don’t scan anything, the safe small controller PNOZmulti 2 brings the hazardous movement of the machine to a safe stop. Once the cardboard has been replenished, the machine can be restarted after confirmation.
Solution saves money and labour
The solution removes the need for rigid protective devices such as tunnels, while the blanks can also be reloaded from both sides, which makes sense from an ergonomic point of view. To prevent the machine moving needlessly to a “safe stop” and stopping in the middle of the cycle, a light sensor installed at the feed magazine acts as a notification stage: This constantly verifies the level of cardboard and sends an alert if more blanks need to be supplied.
For compact packaging machines such as the tray former, Pilz offers a TÜV-Süd certified solution for PL d and Cat. 3 of EN ISO 13849-1 or SIL CL 2 of EN IEC 62061. If the sensors are operated in combination with PNOZmulti 2 or the new kind of modular safety relay myPNOZ, the users can be confident that this solution meets all safety requirements.
Alongside monitoring protection of the feed magazine, PNOZmulti 2 also evaluates the signals of the safety gate systems PSENslock, which are installed as magnetic process guards on doors and hoods, as well as those of the installed E-STOP pushbuttons. The plain text messages from the PNOZmulti 2 primarily enable possible problems to be detected immediately and standstills to be rectified quickly. “We only use the configurable small controller PNOZmulti 2 from Pilz in our tray formers. There it normally has to monitor at least ten or even more inputs and outputs. When combined with the feed protection, PNOZmulti 2 offers sufficient flexibility for adjustments and real added value for our customers,” explains Wehrhahn.
Sema recognised that the focus is increasingly being placed on efficient safety solutions for end customers. That, after all, is how process efficiency can be improved, standstill times reduced and, ultimately, a competitive edge achieved. It has long been clear to Wehrhahn that it's not just a matter of reliable products – process and solution expertise and in-depth industry knowledge are also essential: “Another reason we’re happy to work with Pilz is that we always get detailed answers to our questions, are kept regularly informed of changes and new features and, quite simply, get good advice,” he says in summary.