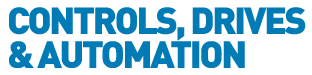
![]() |
Charlotte Stonestreet
Managing Editor |
Editor's Pick
Safely hand in hand
05 August 2019
Separate working areas with no direct interaction between man and machine: these are the principles that have applied to robot applications for more than 50 years. However, the new generation of robots, safe sensors and control systems, along with the Technical Specification ISO/TS 15066, offer practicable ways towards safe collaboration
Current developments in the field of robot applications are characterised by the desire to allow man and machine to work as closely as possible with one another. Instead of man and machine cooperating by means of defined static transfer points, both partners collaborate in a shared workspace and are deployed together on a flexible basis such that they can exploit their respective strengths.
Collaborative Robots – Cobots – are lightweight robots with a sensory, tactile capability. As service robots, they are intended to “give humans a hand” with physically burdensome or monotonous tasks. Typical uses are pick-and-place applications, handling operations between different production steps or follow-the-line applications where the robot has to follow precisely a specified trajectory (e.g. when tracing a contour or for bonding tasks).
In human-robot collaborations (HRCs) like this, the workspaces of humans and robots overlap both spatially and chronologically. This combines the strengths and advantages of the machine, such as reliability, endurance and repeat accuracy, with human strengths, in other words dexterity, flexibility and the capacity to make decisions. The most conspicuous difference between “classic”, enclosed robot applications and human-robot collaboration is that collisions between machines and humans are a real possibility. This brings with it additional challenges as they must not be allowed to result in any injuries.
Despite the new ‘Cobots’, the following applies: robots cannot provide safety on their own. There are no safe robots, there are only safe robot applications. Safety results from the interaction of normative boundary conditions, the risk analysis that is based on it, the selection of a robot with the corresponding safety functions and the matching additional safety components, and finally from validation.
This means that the Technical Specification ISO/TS 15066 “Robots and Robotic Devices - Collaborative industrial robots”, plays a key role. This Technical Specification makes it possible to implement safe human-robot collaborations following appropriate validation.
Four types of collaboration are described in ISO/TS 15066 as protection principles:
- Safety-rated monitored stop
- Hand guiding
- Speed and separation monitoring
- Power and force limiting
When implementing a safe human-robot collaboration (HRC), system integrators can choose one of these “types of collaboration” or a combination of them for their application.
The Annex to ISO/TS 15066 describes a body model. It provides information for each part of the body (e.g. on the head, the hand, the arm or the leg) about the respective collision limit values. If the application remains between these limits when a human encounters a robot, then it is compliant. These pain threshold values are used in practice to validate a safe HRC and form the basis for implementing the application with “power and force limiting”.
In practice, it has been found that human-robot collaborations can often be achieved by combining “speed and separation monitoring” and “power and force limiting”
Pilz has developed a collision measuring device PRMS to measure forces and speeds. Equipped with springs and appropriate sensors, the device can record precisely the forces generated in a collision with a robot, evaluate them in software and compare them with the specifications from ISO/TS 15066.
The challenge in the basic “risk assessment” for robot applications is that the boundaries between separate working areas for man and machine have ceased to exist. As well as the hazards presented by a robot, the human’s movements need to be taken into consideration. But they are not always calculable in terms of speed, reflexes or the sudden arrival of another person.
Intelligent sensors
Then follow the “safety concept” and “safety design” steps, which cover the ‘human element’ as well as selection of the correct components. These are usually a combination of intelligent sensors that are interlinked, and control systems that make the necessary dynamic working processes possible in the first place. The selected safety measures are then documented and implemented in the “system integration” step. This is followed by “validation”, when the previous steps are scrutinised again.
When supplying in to Europe, manufacturers of robot applications are then subject to the principle that, by law, they must complete the assessment procedure with CE marking of the robot application.
The demands on safety technology always depend on the respective application. Safe robot cells can only be set up within the overall context of the robot, tool and work piece plus any associated machinery such as conveyor systems, for example. This means in practice that every application calls for a separate safety assessment.
Implementing human-robot collaborations in an industrial environment is definitely going to increase; however, its growth will be heavily dependent on innovations in the fields of sensor technology and robotics. Together, automation engineers, robot manufacturers, integrators and notified bodies will be able to make the vision of a robot workmate reality on a step-by-step and application-by-application basis.
Pilz as a solution supplier provides the relevant services and products and systems for safe robot applications. The company supports users with a services portfolio tailored to the individual life cycle phases of a robot system: from process analysis to risk assessment and beyond to CE marking. A specific training package on robot safety completes the range of services.
Contact Pilz via www.pilz.co.uk for further information, or to receive a copy of the Pilz Poster ‘HRC – Human Robot Collaboration – ISO/TS 15066’ and the Pilz Whitepaper ‘En-Route to Robot Safety’
- Safety and security go hand in hand
- When were your Light Curtains last tested?
- Expand your CE and UKCA knowledge with Pilz
- Pilz Machinery Safety webinar series updated for 2024
- Safe machinery, step-by-step
- Machine safety webinar series
- Safeguarding frequent access danger zones
- Meets latest interlocking standard
- En Route to Robot Safety
- Meets PLe For Series Connected Switches
- No related articles listed