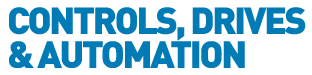
![]() |
Charlotte Stonestreet
Managing Editor |
Home> | AUTOMATION | >Encoders | >Simple path to safe productivity |
Home> | MACHINE BUILDING & ENGINEERING | >Machinery Safety | >Simple path to safe productivity |
Editor's Pick
Simple path to safe productivity
16 November 2021
SICK HAS extended its safe encoder offering with the AFS60S Pro and AFM60S Pro, its first programmable safe absolute encoders, opening a simpler and quicker route to safe productivity in stationary and mobile machinery, together with seamless integration for safe motion control.
The SICK AFS60S Pro (singleturn) and SICK AFM60S Pro (multiturn) absolute encoders are compact, programmable, high-resolution absolute encoders that deliver functional safety certified up to SIL3/PLe when monitoring the position, speed and rotation direction of drives and axes.
When fully-integrated with the SICK FX3-MOC1 safe drive monitor and the SICK Flexi Soft safety controller, the AFS/AFM60S Pro encoders also support the safe motion functions of drives in accordance with IEC 61800-5-2. They have therefore enabled a convenient new single-source solution from SICK for rapid integration of safe motion control.
Plug and Play Integration
The SICK AFS/AFM60S Pro safety encoders save implementation time and cost, for example for safe speed and position monitoring of automated transport vehicles. They enable safe monitoring of machinery drives to protect personnel during operations such as tool set up, manual loading or maintenance. They also offer a much-simplified solution for the safe position monitoring of operator access to presses.
“Whether you are building a new machine, or upgrading an existing one, SICK’s new safe absolute encoder will offer a good fit for plug and play integration into your application,” says Darren Pratt, SICK’s UK encoder product manager.
“Thanks to SICK’s streamlined safety engineering, you also no longer need to worry about selecting the right individual components for safe motion control. Integration, commissioning and maintenance are also quicker and easier with a complete package that benefits from SICK’s 70 years of industry-leading machine safety expertise.”
Application versatility
The SICK AFS/AFM60S Pro absolute encoders are ideal for safe monitoring of the propulsion and steering drives of mobile transport, such as Automated Guided Vehicles. When integrated with a safety laser scanner through the SICK Flexi Soft controller, the SICK AFS/AFM60S Pro safe absolute encoders enable the vehicle’s protective fields to be adapted to steer around obstacles and avoid collisions.
Some of the earliest successful applications of the SICK AFS/AFM60S Pro safe absolute encoders have been to simplify the implementation of operator safety on presses. When integrated with a safety light curtain, using a programmable safe absolute encoder eliminates the need for a complex and costly mechanical cam concept to mute the light curtain during the safe period of the press stroke.
The SICK AFS/AFM60S Pro has been developed for maximum configuration versatility and, with its SSI and sin/cos interface, it can be easily integrated into a range of different controls. The SICK AFS60S Pro (singleturn) offers a resolution of up to 262,144 steps per revolution (18 bit) and SICK AFM60S Pro (multiturn) up to 18 bit x 12 bit (262,144 x 4,096), making them easily compatible with most applications.
The easy programmability of the SICK AFS/AFM60S Pro makes for simple and rapid set up, with the ability for the singleturn resolution, counting direction and other parameters to be entered and adjusted individually. With versatile multiple mechanical and electrical connection options, one encoder type covers a wide variety of needs, so inventories can be optimised.
The SICK AFS/AFM60 Pro offers variants with both hollow shafts or solid shafts, with a face mount or servo flange. Connected directly to a machine’s drive shaft, the encoders offer the added security of a keyed groove or flat form-fit options to prevent slippage and meet the high safety requirements of PLe.
The SICK AFS/AFM60S Pro encoders’ integrated fault memory saves important ambient and functional data that can be easily read by the SICK Safety Designer software tool, to assist with the correct installation, ongoing operation and service of the encoder. With an IP65 enclosure rating and an operating temperature range of -30 °C to +95 °C, the AFS/AFM60S Pro can be used even in harsh industrial environments.
- 3D vision made easy for all
- How safe is your cobot application?
- Turning inspectors into detectives
- Open service for IO-Link function blocks
- Easy vision robot guidance
- Keeping safety in the loop
- Encoders Cut Costs
- Powerful and compact cube sensor
- Brings live sensor data to the Cloud
- Open a window to compressed air energy savings