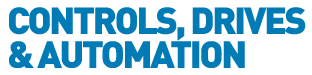
![]() |
Charlotte Stonestreet
Managing Editor |
Home> | POWER TRANSMISSION | >Gearboxes | >New smart gearbox enables I4.0 predictive maintenance |
New smart gearbox enables I4.0 predictive maintenance
06 September 2023
AVAILABLE FROM Mclennan, Wittenstein’s new cynapse® smart gearbox combines built-in sensors with analysis and visualisation software to monitor significant gearbox threshold data that is communicated via IO-Link to PLCs as well as higher level IPCs/Gateways and Cloud systems for comprehensive IIoT integration. Data including acceleration, vibration, operating time, and temperature etc. can be evaluated as part of Industry 4.0 predictive maintenance.

With its ability to collect, analyse and visualise built-in gearbox information and sensor data, cynapse adds a layer of predictive maintenance that is stored locally in the gearbox, or communicated via IO-Link to PLCs as well as higher level IPCs/Gateways and Cloud systems – enabling comprehensive IIoT integration.
By directly monitoring and logging gearbox threshold data – where the gearbox output is often directly connected to the critical load-point of typical position-controlled motion systems – applications across automated machinery and processing can achieve real benefits in higher transparency, reduced downtimes, and improved system reliability.
To support cynapse Wittenstein offers its Smart Services software comprising various functions that include a Monitor control terminal that allows graphical visualisation of all gearbox data, a Data Gateway facility to easily configure integration with PLCs and higher-level systems, a Teach-In facility for straightforward set-up of gearbox threshold values, and an Anomaly Check facility that detects nonconformity in the process or the component behaviour.
The cynapse option is built into the gearbox housing and although not available as a retrofit, customers requiring upgraded predictive maintenance requirements can easily swap out existing gearboxes. A single IO-Link connector interfaces the gearbox allowing retrieval of sensor information which includes acceleration in X, Y and Z spatial axes as RMS and Peak-to-Peak values as well as temperature and runtime.
Derived information and events such as vibration levels, gearbox orientation, ambient temperature, operational duty time, and more are thus made available via commands through IO-Link. This data can be compared alongside the expected lifetime predictions and maintenance periods for the specific application to realise comprehensive predictive maintenance for individual motion system axes. The sensor data is always stored and retained within the gearbox, so is available in case of power loss or where further analysis might be required.
- Mclennan safeguards manufacture & supply of SmartDrive D- & DM-series Eurocard stepper drives
- Full featured microstepping drive is a real space saver
- Deterministic real-time motion control
- New microstepping drive range with multiple communication options
- Custom motion systems provide energy savings
- Designed for high performance robotics
- EtherCAT encoders
- EtherCAT motion controller complements Mclennan's custom build service
- IP65 rated
- Cost-effective servo motors
- GEARBOX IS CHEAPER TO REPLACE THAN REPAIR
- PLANETARY/SPUR GEARBOXES
- PLANETARY GEARS WELL SUITED FOR RETROFIT
- AGEING WORM GEARS REPLACED BY PLANETARY GEARS IN SEWAGE PLANT
- REHFUSS BRINGS QUALITY AND VERSATILITY TO GEARBOX DESIGN AND SELECTION
- FLEXIBLE COUPLINGS
- GETTING THE BEST OUT OF GEARBOXES
- A Guide to the Selection
- Greater Corrosion Resistance
- Fits existing parameters