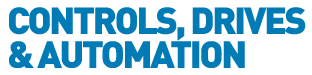
![]() |
Charlotte Stonestreet
Managing Editor |
Home> | IIot & Smart Technology | >IIoT | >The impact of IoT on the manufacturing industry |
Home> | IIot & Smart Technology | >Industry 4.0 | >The impact of IoT on the manufacturing industry |
Editor's Pick
The impact of IoT on the manufacturing industry
08 May 2024
THE INTERNET of Things (IoT) has allowed companies to forge innovative, integrated technologies, facilitating the creation of cutting-edge solutions for the manufacturing industry. Leveraging IoT-enabled systems, they drive advancements and foster the evolution of Industry 4.0.

Aside from streamlining processes, these IoT-enabled systems help enhance efficiency and promote connectivity, ushering in a new era of technological prowess in manufacturing.
Here's what to know about the impact of IoT on the manufacturing industry.
Improved supply chain
The Internet of Things (IoT) revolutionises supply chain management in manufacturing by providing real-time visibility, automation, and predictive analytics capabilities. IoT-enabled devices, such as sensors, RFID tags, and connected machinery, create a network of interconnected assets throughout the supply chain. These devices continuously collect and transmit data regarding inventory levels, equipment status, production rates, and environmental conditions. This data is then analysed in real-time, allowing manufacturers to monitor and optimise various aspects of the supply chain.
One significant benefit of IoT is enhanced inventory management. IoT sensors track the movement and storage of raw materials, components, and finished products, enabling manufacturers to maintain optimal stock levels, reduce excess inventory, and prevent stockouts. IoT also facilitates predictive maintenance by monitoring equipment performance and detecting potential issues before they lead to downtime. This proactive approach minimises disruptions, prolongs equipment lifespan, and reduces maintenance costs.
Additionally, IoT enables supply chain transparency and traceability by providing detailed insights into the origin, location, and condition of products throughout their lifecycle. This visibility helps manufacturers ensure compliance with regulations, meet quality standards, and address any issues promptly.
Increased revenue
Integrating Internet of Things (IoT) technology in manufacturing offers significant opportunities for companies to increase revenue through various avenues. First, IoT enables predictive maintenance, allowing manufacturers to anticipate equipment failures and schedule maintenance activities before breakdowns occur. By minimising unplanned downtime, companies can maintain consistent production levels, fulfil orders on time, and avoid losses associated with halted operations.
Secondly, IoT facilitates enhanced product quality and customisation. Real-time monitoring of production parameters and product performance enables manufacturers to identify and rectify defects promptly, ensuring that only high-quality products reach the market. Additionally, IoT enables mass customisation by collecting data on consumer preferences and usage patterns, allowing companies to tailor products to individual needs and capture niche markets, thereby commanding premium prices and boosting revenue.
Furthermore, IoT enables manufacturers to optimise resource utilisation and operational efficiency. By monitoring energy consumption, material usage, and production processes in real-time, companies can identify opportunities for cost savings and efficiency improvements, thereby increasing profitability and overall revenue.
By leveraging IoT technologies effectively, manufacturers can stay competitive, capitalise on new market opportunities, and achieve sustainable revenue growth in the rapidly evolving manufacturing landscape.
Creating more jobs
The adoption of IoT technology in the manufacturing industry not only transforms operational processes but also creates new job opportunities across various domains. As manufacturing becomes increasingly automated and data-driven with IoT, there is a surge in demand for automotive software engineers, alongside other roles capable of troubleshooting and repairing IoT-enabled equipment and machinery.
One significant way IoT contributes to job creation is through the demand for skilled professionals to develop, deploy, and maintain IoT systems and devices. Manufacturing companies require engineers proficient in IoT technologies to design and implement connected machinery, sensors, and data analytics platforms.
Moreover, integrating IoT into manufacturing processes often necessitates the development of specialised software tailored to industry-specific needs. For example, in the automotive sector, the growing reliance on IoT-driven systems for vehicle assembly, quality control, and supply chain management increases the demand for automotive software engineers. These engineers specialise in developing software solutions for embedded systems, connectivity protocols, and vehicle-to-everything (V2X) communication, driving job growth in this niche area.
The adoption of IoT in manufacturing not only enhances operational efficiency but also creates a diverse range of job opportunities, from software development to technical support, contributing to the growth and dynamism of the industry.
Predictive maintenance
IoT revolutionises predictive maintenance in the manufacturing industry by enabling real-time monitoring, data analytics, and proactive decision-making. IoT sensors installed on machinery and equipment continuously collect and transmit data regarding various parameters, such as temperature, vibration, and operating conditions.
This data is then analysed using advanced algorithms and machine learning techniques to detect patterns and anomalies indicative of potential equipment failures. By leveraging historical performance data and predictive models, manufacturers can anticipate maintenance needs and schedule proactive interventions before breakdowns occur.
Moreover, IoT enables condition-based maintenance, where maintenance activities are triggered based on the actual state of the equipment rather than predefined schedules. This approach optimises resource allocation and minimises unnecessary maintenance, reducing costs and downtime. Furthermore, IoT facilitates remote monitoring and diagnostics, allowing maintenance teams to access real-time data and insights from anywhere, enabling timely interventions and troubleshooting.
By leveraging IoT technologies, manufacturers can transition from reactive to proactive maintenance strategies, ultimately optimising resource utilisation and enhancing competitiveness in the market.
Asset monitoring
IoT revolutionises asset monitoring for manufacturing companies by providing real-time insights into the assets' status, location, and performance throughout the production process. IoT sensors and connected devices embedded within machinery, equipment, and inventory enable continuous data collection and transmission, facilitating proactive monitoring and management.
With IoT, manufacturing companies can monitor key performance indicators (KPIs) such as equipment uptime, production output, and energy consumption in real-time. This real-time visibility allows companies to identify inefficiencies, anticipate potential issues, and optimise asset utilisation for improved productivity and profitability.
Moreover, IoT enables predictive maintenance by monitoring equipment health parameters such as temperature, vibration, and lubrication levels. By analysing this data using machine learning algorithms, manufacturers can predict equipment failures before they occur, schedule maintenance activities proactively, and avoid costly unplanned downtime.
Furthermore, IoT facilitates asset tracking and inventory management by providing accurate location data and real-time updates on the movement and status of goods and materials within the facility or across the supply chain. This enhanced visibility improves inventory accuracy, reduces stockouts, and streamlines logistics operations.
- No related articles listed
- Industry 4.0 ready
- Intelligent interlocks
- What operators need to know about IIoT adoption
- Predictive maintenance leader
- The digital future has begun
- The smart future of manufacturing
- Partnership integrates freight & warehouse management
- Secure data handling
- Makes IoT available in practice
- When & where will Industry 4.0 actually happen?