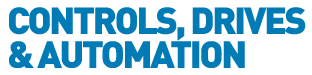
![]() |
Charlotte Stonestreet
Managing Editor |
What Makes A Phase Failure Relay Fail?
17 January 2013
Malcolm Greenhill of Charter Controls looks at the issues surrounding why Phase Failure Relays occasionally fail
Question: When is a Phase Failure Relay not a Phase Failure Relay?
Answer: Well, when it’s failed of course. Phase Failure Relays occasionally fail – fact!
So why do Phase Failure Relays occasionally fail? The biggest enemy of a Phase Failure Relay (PFR) is heat and that heat can come from a number of sources, the most common in my experience is incorrect installation. Other causes are harmonics and other supply borne interference such as voltage spikes and surges.
A PFR must have a low input resistance whereas other supply powered devices will have a high input resistance
But first we must consider what a PFR is being asked to do. How many electronic devices in your control panels operate on 400/415vac? Would that be just one? PFRs are normally the only electronic device in a Control Panel which is powered by the incoming three phase supply, however internally they only use low voltage. This means that they must dissipate a lot of electrical energy and one way they do this is to get warm. This is allowed for in the design process. Capacitors are used to drop the voltage. Better types use capacitors with internal series connections, but the quality from different component manufacturers can differ and only experience will weed out the bad ones.
This issue is compounded by the fact that in order to measure the supply voltage a PFR must have a low input resistance whereas other supply powered devices will have a high input resistance, which effectively eliminates much of the external electrical noise, depending on the source.
Heat sources
Let’s look at heat sources;
Incorrect installation: We all like to do a neat job and in many instances we see PFRs ‘crush’ mounted next to the motor contactor. This may look neat but the surface temperature of a contactor at nominal voltage can be in excess of 60˚C. Add this to the internally generated heat in the PPR at say +10˚C the result is 70+˚C. This is immediately outside the temperature tolerance of the components inside the PPR. Any air gap up to 10mm between the contactor (or other adjacent heat source) and PFR will help. Above 10mm makes no great difference.
Harmonics: Harmonics on the supply cause increased current flow in the PFR’s power supply. Increased current equals increased heat – simple! Many a site harmonic survey has revealed this to be the cause.
Spikes and surges: These cause gradual degradation of the foil capacitors in the PFR’s power supply by causing flash-overs between the foil ‘plates’. Even if self-repairing foil capacitors are used these will still deteriorate over time. Add that to the heat from other sources drying the electrolyte in the aluminium electrolytic capacitors and the life of the PFR is seriously reduced. The first indication of this will be that although the PFR powers up, when the output relay tries to pull in it will chatter as the power supply cannot deliver sufficient power to hold it in.
Of course, you could use a PFR with a transformer power supply. Apart from costing you up to three times more than one with a Switched Mode power supply, and having a limited operating voltage range, there are still heat issues associated with transformers. I have witnessed a PFR with a hole melted in its housing from just this cause when crush mounted with a contactor. Thus the primary benefit when using a transformer is galvanic isolation, which is not generally required in this type of device.
At Charter Controls we sell a wide variety of Phase Failure Relays from a number of sources. All of these use top quality components including self-repairing ‘3000 hour, 105˚C’ capacitors which feature the ‘doubling 10˚C rule’. At 105˚C the rated life is 3000 hours. For every 10˚C reduction in temperature the rated life doubles. Therefore at 65˚C the rated life is 48,000 hours (5.48 years) at 55˚C is 96,000 hours (11 years), at 45˚C is 192,000 hours (22 years) and at 35˚C 384,000 hours or 22 years.
All GIC products are manufactured to withstand tropical temperatures and poor quality supplies. They are soak tested for 24hrs at 50˚C after final testing and prior to packaging. Quality and reliability are never taken for granted.
Key Points
- The most common cause of Phase Failure Relay failure is heat, which can come from a number of sources
- In many instances PFRs ‘are crush’ mounted next to the motor contactor
- Charter Controls sells a wide variety of Phase Failure Relays from a number of sources
- SPE Offshore Europe looks to the future
- Belting for peak season
- Tech start-up to half the cost of CNC machined parts
- AMR revolution in cold chain logistics
- Conscia becomes first Cisco IoT Advantage Partner
- Food industry automation
- Covariant launches to bring universal AI to robots
- Are you ready for the changes to EU Authorised Representatives?
- Automate UK CTO helps to set new standards
- Data woes stifling innovation