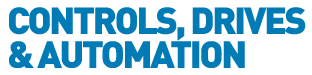
![]() |
Charlotte Stonestreet
Managing Editor |
Home> | INDUSTRY FOCUSES | >Food & Beverage | >Food industry automation |
Food industry automation
23 October 2014
Pressure on prices is rising in food manufacture. Productivity and profit margins are low. Above all, small and medium-sized operations are facing the challenge of competing in price terms with the discounter and supermarket offers. All this adds up to automation looking like an ever-more attractive option for the food industry
More than ever, manufacturers in the food industry need to maximise flexibility and standardisation. Often, these two objectives appear to be at odds. For example, there is no such thing as a standard worldwide taste (regardless of how global a brand may be). In farming, factors like seasonality, climate changes, and feedstock quality make it difficult to get nature to function like a highly efficient and consistent factory to feed a planet of over 7 billion people.
Although way behind the rest of the EU and US markets in terms of sales, the UK food industry has understandably taken an interest in robots. 2013 figures from the British Automation and Robotics Association (BARA) reveal a 60% increase in food sector adoption compared to 2000.
Fanuc, for example, has seen enquiries increase by 27% from food manufacturers looking to automate their food handling and packing operations. Robots are also common in pick-and-place applications. Fanuc has responded by developing a food picker cell, combining both articulated arm and delta style food grade robots. The food picker cell (measuring 4 x 2.2 x 2.35m) is designed to orientate and pack a wide variety of unpackaged and packaged foods. Fanuc’s latest robots are designed specifically to work in harsh environments, and incorporate vision technology.

"Many barriers to entry have been addressed: only in the last 12-18 months have we made available IP69K-certified robots to meet the toughest of hygiene standards,” says John Rainer, Regional Sales Manager of Fanuc UK. "Manufacturers looking to improve hygiene, by removing the uncertainty that the human element brings to the equation, have been driving the need for food-grade robots.
"Food manufacturers face a number of challenges in their production operations,” Rainer adds. "In a manual process, they must deal with ergonomic issues, labour availability and the uncertainty of increasing costs associated with legislation. In an automated process, accommodating rapid-fire product and pack changes driven by sustainability initiatives and shelf impact is key. And in any process, food safety is an overriding concern on the minds of processors, as the consequences of foodborne illness and/or massive product recalls have affected a wide range of food categories.”
Combining ultrasonic technology with robot systems offers a highly flexible and effective approach to many different food-cutting applications and continues to increase at a steady pace. Telsonic’s expertise in ultrasonic food cutting led food industry automation supplier Newtech to seek its advice when building its dual robot system, to process tray baked product for one of the UK’s leading cake manufacturers. For Newtech’s latest application the specification requirements included a fast clean cut with no smearing, accurate portion control, reduced waste at edge of tray/offcuts and low noise.

Telsonic supplied Newtech with demonstration equipment, including a 500mm wide blade, to allow trials and customer demonstrations to take place. These trials were conducted across a range of tray-baked product including flap-jack, malt loaf, slab cake and brownies, with and without inclusions.
Industry 4.0 (aka the Internet of Things) is also being introduced into the food and drinks industry. The focus is on new automation technologies and intelligent production processes. Data transparency within networked production is easily achieved with standard automation technology. Automation can substantially contribute to the long-term sustainability of new systems, as well as enhance systems which have been expanded over the years.
When existing plants are modernised, companies need to retrospectively link isolated networks from different manufacturers and of different ages in order to collect all relevant data for the higher-level management systems at field level. With the help of standard automation components such as the MES-IT interface module from Mitsubishi Electric the necessary transparency can be achieved quickly and cost efficiently. Wholly in terms of Industry 4.0, the module detects production data and test results from every manufacturing step and transfers them in real-time to higher-level systems. These then produce transparent and reliable analyses of processes and procedures using Excel, SAP or pre-produced reports. Such equipment is quick to connect to existing systems with no interruption to machinery processes.

Optimising machine running times by preventative maintenance is another major issue in the food processing industry. If a machine suddenly fails, an entire batch is usually lost. This is expensive and damaging to productivity. Modern control platforms, touchscreen operating devices and sensors with comprehensive, integrated functionalities as well as flexible maintenance and repair concepts such as the FAG SmartCheck from Schaeffler FAG or the MAPS Life-Cycle-Software tool from Mitsubishi Electric provide the necessary data transparency for simple implementation of preventative maintenance concepts.
The FAG SmartCheck for example recognises and reports the first vibrations of a system long before any noise is generated. The reaction time before machine failure is therefore substantially longer. The maintenance cycle can be adjusted to production at an equally early stage. Machines can be easily retrofitted with the FAG SmartCheck. In bakery systems, for instance, it could be retrofitted to the loading system, mixer or conveyor belts.
From shop-floor to top floor
More companies are aiming to measure Overall Equipment Effectiveness (OEE) in order to identify bottlenecks and weaknesses in the production process. But these calculations can only be arrived at, once sufficient data is being collected from the entire operation and reliably stored.
Sectors such as food processing, pharmaceuticals and automotive manufacture are feeling increasing regulatory and customer pressure to log process-critical data in ever finer detail and in ways which are fully traceable. In the food industry’s complex supply chains, the traceability of its ingredients from multiple sources is more important than ever. In the meat industry, these demands have reached the stage where provenance needs to be traceable back to an individual animal. The amount of detail, the speed of acquisition and retrieval and the security requirements for any data are only going to increase in sensitive product areas such as food and pharmaceuticals.
This means not only that the days of ‘pen and paper’ data collection are long gone, but that some of the slower ways of electronically logging information are giving way to much faster, real-time collection and processing.
For example, the Food & Drug Administration’s (FDA’s) CFR21 part 11 directive for the pharmaceuticals sector is now well-established, and foresees the collection and storage of production data without the possibility of human intervention. The EU’s Good Manufacturing Practice directive lays down similar standards regarding reliable and secure records.
To make this vision a reality, the controller hardware must be able to connect directly with the same networks as the databases which form the backbone of each enterprise-level system. Up to now, additional hardware modules or SCADA middleware have been the enabler for this, but have also introduced bottlenecks into the process, losing the real-time aspect of data exchange. Inserting this intermediate level into communications also introduces an element of risk, with requirements for maintenance, system updates and constant vulnerability to viruses.
The answer lies in a combination of much faster communications (sub-millisecond speeds) and local control systems which allow this direct, two-way dialogue with enterprise-level relational databases to take place.
Ethernet-based networks such as EtherCAT allow every part of an automation system, from sensors to robots, to exchange information at speeds that were undreamt of in the past. This gives the controller instant access to every detail of production information.
Solutions allowing real-time data exchange already exist. Omron’s NJ501-1_20 machine automation controller CPUs have this level of functionality embedded, thanks to programme-free ‘wizard’ connections to relational databases including Microsoft SQL, Oracle, MySQL, IBM DB2 and Firebird. Pre-written function blocks then allow data from the machine or process to be mapped, inserted or updated into the database, or a query delivered to select specific data.

The latest controllers, such as Omron’s Sysmac NJ series, combine the reliability and rugged design of a traditional PLC, but use an open hardware architecture combined with software ‘engines’ within a single CPU – rather than multiple CPUs – to manage their different functions.
MES Performance Software
What started out as a beer brewing hobby fuelled by a passion for great tasting niche beers, has turned into one of America’s best multi-million dollar success stories.
"New Belgium’s brewing operations were rapidly reaching capacity, and we needed to identify both efficiencies and inefficiencies in our bottling lines so the brewery could maintain its operating schedule,” said Joe Herrick, packaging systems manager at New Belgium Brewing. "With such a rapid growth of our business year after year, and sometimes at a pretty fast clip, this was a good problem to have, but still a problem we needed to address.
"The operations management team realized it was time to expand our current Wonderware automation software capabilities to take advantage of its full Manufacturing Execution System (MES) capabilities,” Herrick said.
With the implementation of Wonderware MES Performance Software from Invensys Systems, New Belgium has achieved record levels of efficiencies in scheduled and non-scheduled downtime throughout its operations.
After completing an audit of its production line and the data being gleaned from system operations, New Belgium determined that valuable packaging time was being lost during both scheduled and unscheduled downtimes. Its manual data recording process, which involved managing paper production logs and spreadsheets, was just not enough to keep up with the level of bottling production New Belgium was now required to achieve.
The management team realised it was time to take the next step in its plant automation strategy to implement a software strategy that would increase operational efficiencies, quality, compliance and overall performance. With the implementation of a Wonderware MES software solution, New Belgium was able to use the data collected by the MES software to increase Overall Equipment Effectiveness (OEE).

"At one point our filler was experiencing a significant amount of micro stops (30 seconds or less) due to some bottles coming down the line that were falling down, or getting hung up on rails,” Herrick said. "The Wonderware software was able to provide us specific information related to these downtimes, so we had our team complete a Kaizan evaluation to figure out what we needed to do to improve it."
The software also provided for smoother transitions between shift changes by enabling the new shift to easily view what went on during the previous shifts, which help them identify potential issues that need to be addressed by the staff.
Key Points
- 2013 figures BARA show a 60% increase in food sector adoption of automation compared to 2000
- Fanuc has developed a food picker cell, combining both articulated arm and delta style food grade robots
- Combining ultrasonic technology with robot systems offers a flexible and effective approach to food-cutting
- In bakery systems the FAG SmartCheck could be retrofitted to the loading system, mixer or conveyor belts
- With the implementation of Wonderware MES Performance Software, New Belgium has achieved record efficiency
- 2022: a watershed year for AI adoption
- Physical AI framework enables rapid learning of complex skills in robotics
- Harwell Space Cluster on track to hit 2030 target
- Leading manufacturers join Venturefest North West line-up
- Sophisticated end of arm tooling enhances automated manufacturing
- 3D Hubs launches Online Engineering Summit series
- IET announces new chief executive and secretary
- Warehouse automation benefits stack up
- Pump up the savings
- Wind sector O&M costs fall with Covid-19 induced work practices
- DEEPER INTEGRATION IN THE FOOD INDUSTRY
- Offering benefits to the food & beverage industry
- Reliable Feeding
- Food & beverage sector benefits
- High hygiene
- Extra reach for high speed applications
- Cut the cost of bearing downtime
- The value of continuous development
- Keeping the milk flowing
- Food handling robots