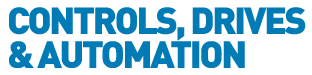
![]() |
Charlotte Stonestreet
Managing Editor |
Home> | MACHINE BUILDING & ENGINEERING | >Machinery Safety | >Machinery safety system design simplified |
Machinery safety system design simplified
08 May 2013
Rockwell Automation has released a configuration and design tool to help machinery automation system engineers save time when designing safety systems. The Rockwell Automation Safety Automation Builder (SAB) configuration software helps users navigate the safety-system design process and apply global best practices.
With better designs and enhanced machine intelligence, manufacturers are finding they no longer have to make a false choice between productivity and safety.
It wasn’t too long ago that machine safety meant something physical, such as putting guards on a press or a cage around a robot. These mechanical barriers, not surprisingly, were often seen by managers and operators alike as a productivity impediment. This helped fuel the view that safety and productivity were in conflict. And often meant that guards were circumvented or disabled.
The new view of safety and productivity is that they are complementary. Machine designs that integrate safety and the use of manufacturing intelligence are combining to provide manufacturers with machines that are not only safer to operate and maintain, but that actually enhance throughput and minimise downtime.
Intelligent safety functions
Builders can now incorporate more intelligent safety functions into machines so that they minimise the impact on production. For example, printing machines require periodic maintenance where rollers need to be wiped down. In a traditional setup, an employee would lock out a machine, wipe down a third of the rollers, exit and re-energize the machine, jog it along to the next third, then repeat the steps.
Current safety standards allow "safe speed” and "safe direction” to be used during maintenance. This allows the operative to slow the machine down to a speed where someone can reasonably get away from a hazard if something happened. It also utilizes safe direction, which reverses the direction of the rollers so that someone is pushed out of the machine, not pulled into it.
The SAB software tool, available as a free download from the Rockwell Automation website, guides engineers through the safety-system design process by providing options for layout, safety Performance Level (PL) analysis and product selection using Allen-Bradley products. The PL analysis uses IFA’s SISTEMA software tool (Safety Integrity Software Tool for Evaluation of Machine Applications) which is based on the globally accepted standard EN ISO 13849-1.
Process automated
Traditionally, engineers needed to go through an extensive process of printing machinery-layout drawings, drawing hard and movable guarding, identifying potentially hazardous access points and required safety functions, selecting safety input, output and logic devices, and calculating the achieved Performance Level (PL) for the safety-related control system. This resulted in a list of required materials and safety calculations that engineers had to transfer into documents, drawings and reports.
The SAB software automates the safety-selection process to help speed system design and minimize human error. With the SAB tool, users import an image of the machinery they wish to safeguard and answer questions using a drop-down menu and help screens to identify and select the necessary safeguards. The software then compiles all product selections, generates a bill of materials, and compiles necessary data to populate SISTEMA. SISTEMA indicates the attained PL of the safety system using EN ISO 13849-1 principles through an automatic calculation. As part of the process, users also receive a SISTEMA project file.
Rockwell Automation has also released new Safety Functions, which are pre-engineered design documents containing detailed information for many safeguarding methods, including specific functionality, Performance Level category data and required input, logic and output components. These documents also include parts lists, electrical drawings, a SISTEMA project file, and verification and validation plans.
Key Points
- Machine designs that integrate safety and manufacturing intelligence combine to provide machines that are safer to operate and enhance throughput
- Rockwell's SAB software tool guides engineers through the safety-system design process
- The SAB software automates the safety-selection process to help speed system design and minimize human error
- Addresses bandwidth requirements
- Reduced lead times
- CORPORATE RESPONSIBILITY REPORT ONLINE
- Next generation edge gateway to accelerate IT/OT convergence
- Rockwell's ethical credentials recognised
- Cloud-based software underpins digital transformation
- SCALABLE CONTROL SYSTEMS FOR SMALLER APPLICATIONS
- Easing entry to smart manufacturing
- Irish PM addresses industry leaders
- Taking on the challenge