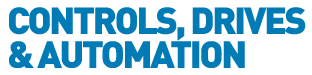
![]() |
Charlotte Stonestreet
Managing Editor |
Home> | MACHINE BUILDING & ENGINEERING | >System Design | >Testbed driveline designs |
ARTICLE
Testbed driveline designs
15 May 2013
Advanced new system capability has made it possible to successfully design drivelines for engine dynamometers by careful selection of the flexible couplings
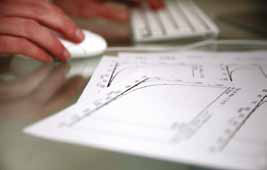
In principle, the connection of an engine to a dynamometer seems a fairly simple thing, but to do it in an engineered way requires some expertise.
As well as sizing the shaft from a torque perspective, other basic requirements need to be fulfilled. The prime consideration after torque capacity is the torsional vibration compatibility between the engine and the dynamometer.
Getting this wrong can lead to dire consequences, the least of which would be failure of the connection shaft, dynamometer or engine.
There are specific mechanical requirements which must also be met, ranging from such factors as the production bed, torque capacity, torsional compatibility, single engine and build variants, and achieving start through the dynamometer. Other requirements include auto docking, height compensation, length compensation and the dynamic movement of engine mounts.
Although all of the above requirements are to be considered, torque capacity and torsional compatibility are the first aspects that must be determined. Other aspects that need to be taken into consideration include development beds and torque capacity, torsional vibration compatibility, different engine configurations and variants, length compensation, and achieving starting through the dynamometer.
Additional factors that also need to be taken onboard are length variation, interchangeability with other driveshafts, auto docking (which is not normally considered a requirement), small changes in height compensation, and dynamic movement due to the engine flexible mounts.
While torque capacity of the driveshaft is relatively straightforward, torsional vibration compatibility requires some effort to get right. A detailed torsional vibration analysis is essential to ensure correct operation of the testbed, which involves start-up transients and steady-state operation.
Where several configurations are to be tested on the same testbed, each engine and build must be calculated. A single shaft can be compatible with similar engine configurations, for example, cylinder in-line engines of different bore/ stroke, where the driveshaft is sized for the largest engine in the series and then checked for torsional compatibility with its smaller series.
Difficulties arise with low cylinder configurations, with one-, two- and three-cylinders proving the greatest challenge. However, with careful analysis, successful installations can be designed and built.
Production testbeds present different challenges and while torsional compatibility is simpler for one engine/one shaft/one dynamometer, the mechanical problems increase. In the case of productions cells, care is required to design the torsional vibration characteristics so that the driveline can cater for poorly/intermittent firing of the green engine. This condition puts significant vibratory torques, and hence heat, into the driveline components and can eventually lead to driveline failure.
To improve cell usage, setup time needs to be minimal. Splines are used as part of an auto-docking system and while the cell retains the driveshaft, the mating port is built onto the engine prior to being automatically delivered into the test cell. Successful design of the spline engagement system is essential for efficient operation in the cell. The spline needs to be of low spline wall pressure, well lubricated, and hardened. Experience shows that high pitch circle diameters and low engagement length work better as there is less edge-loading on the teeth owing to inevitable small misalignments caused by build variance.
In summary, it is possible to design successful drivelines for engine dynamometer systems by careful selection of the flexible couplings that tune them and isolate torsional vibrations from the dynamometer.
As well as sizing the shaft from a torque perspective, other basic requirements need to be fulfilled. The prime consideration after torque capacity is the torsional vibration compatibility between the engine and the dynamometer.
Getting this wrong can lead to dire consequences, the least of which would be failure of the connection shaft, dynamometer or engine.
There are specific mechanical requirements which must also be met, ranging from such factors as the production bed, torque capacity, torsional compatibility, single engine and build variants, and achieving start through the dynamometer. Other requirements include auto docking, height compensation, length compensation and the dynamic movement of engine mounts.
Although all of the above requirements are to be considered, torque capacity and torsional compatibility are the first aspects that must be determined. Other aspects that need to be taken into consideration include development beds and torque capacity, torsional vibration compatibility, different engine configurations and variants, length compensation, and achieving starting through the dynamometer.
Additional factors that also need to be taken onboard are length variation, interchangeability with other driveshafts, auto docking (which is not normally considered a requirement), small changes in height compensation, and dynamic movement due to the engine flexible mounts.
While torque capacity of the driveshaft is relatively straightforward, torsional vibration compatibility requires some effort to get right. A detailed torsional vibration analysis is essential to ensure correct operation of the testbed, which involves start-up transients and steady-state operation.
Where several configurations are to be tested on the same testbed, each engine and build must be calculated. A single shaft can be compatible with similar engine configurations, for example, cylinder in-line engines of different bore/ stroke, where the driveshaft is sized for the largest engine in the series and then checked for torsional compatibility with its smaller series.
Difficulties arise with low cylinder configurations, with one-, two- and three-cylinders proving the greatest challenge. However, with careful analysis, successful installations can be designed and built.
Production testbeds present different challenges and while torsional compatibility is simpler for one engine/one shaft/one dynamometer, the mechanical problems increase. In the case of productions cells, care is required to design the torsional vibration characteristics so that the driveline can cater for poorly/intermittent firing of the green engine. This condition puts significant vibratory torques, and hence heat, into the driveline components and can eventually lead to driveline failure.
To improve cell usage, setup time needs to be minimal. Splines are used as part of an auto-docking system and while the cell retains the driveshaft, the mating port is built onto the engine prior to being automatically delivered into the test cell. Successful design of the spline engagement system is essential for efficient operation in the cell. The spline needs to be of low spline wall pressure, well lubricated, and hardened. Experience shows that high pitch circle diameters and low engagement length work better as there is less edge-loading on the teeth owing to inevitable small misalignments caused by build variance.
In summary, it is possible to design successful drivelines for engine dynamometer systems by careful selection of the flexible couplings that tune them and isolate torsional vibrations from the dynamometer.
MORE FROM THIS COMPANY
RELATED ARTICLES
OTHER ARTICLES IN THIS SECTION