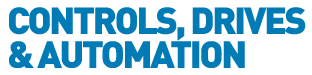
![]() |
Charlotte Stonestreet
Managing Editor |
Home> | AUTOMATION | >Data Capture | >Direct part marking |
Home> | MACHINE BUILDING & ENGINEERING | >Machinery | >Direct part marking |
Home> | MACHINE BUILDING & ENGINEERING | >Monitoring | >Direct part marking |
Direct part marking
14 January 2014
Part tracking or traceability is vital throughout the supply chain - the data is used in production output calculations, inventory control, revenue forecasting and other business operations. This article from Cognex explores some of the basic considerations
Direct Part Marking DPM) reading can be a very challenging application requiring solving difficult image analysis problems.
To track a part through its full lifecycle, manufacturers mark it with a permanent two-dimensional (2-D) code known as a Direct Part Mark (DPM). 2-D codes are used due to their small size, error correction and amount of data that can be stored as compared to traditional 1-D barcodes. 2-D DPM codes also help with anti-counterfeiting measures as they are more difficult to replicate. Automated image-based ID readers are the only technology capable of decoding such marks, as laser scanners are only able to read 1-D linear barcodes.
Code selection
Industry standards groups define codes for a given application like ISO 29158 (formerly known as AIM DPM). The Automotive Industry Action Group (AIAG) has guidelines as do the Air Transport Association (ATA), the US Department of Defense (DoD), GS1, SEMI and others.
When specified, it generally makes sense to follow the industry guidelines because it improves efficiencies throughout product manufacturing and the supply chain. However, if no guidelines are available within your industry, you can use an existing guideline to create your own. The Data Matrix ECC200 is strongly recommended and is clearly becoming the choice for most industries involving metal, glass, ceramic or plastic materials.
The Data Matrix ECC200 is very flexible as it offers 24 square formats and six rectangular formats to encode anywhere between six and 3116 digits in a single code. It also supports Reed Solomon error correction which allows a code to be successfully decoded even though as much as 60% of the code may be damaged. Because this code is in the public domain, marking and reading equipment suppliers have invested significant R&D resources to improve the performance of supporting equipment.
Marking processes & placement
2-D DPM codes are marked on the part using several methods depending upon the material composition, part application and environmental conditions. Important factors influencing the marking process decision include part life expectancy, material composition, environmental wear and tear and production volume. Other considerations include surface texture, the amount of data to be encoded on each part, as well as the available space for, and location of, the mark.
The location of the code on a part can directly impact the readability of the code. It should be clearly visible throughout the manufacturing process and, wherever possible, it should provide a "clear zone” free of part features and edges, noise/texture or other interference. Parts that present some of the most difficult reading situations include cylindrical or shiny parts that can create code distortion and specular reflection.
Data encoding & readability
Data encoding refers to the amount of information that is "stored” within the generated Data Matrix code. Deciding on what information to encode is typically driven by the company specifications and/or the requirements of the traceability project. In selecting what data to encode, one should also consider the amount of available space on the part as code size can affect readability.
The reader must be able to communicate the results to another device, easily integrating into existing plant networks through whatever communications method is required (such as Ethernet, RS-232). For establishing a communications link between a reader and a PC at the enterprise level, the reader should support a broad range of standard network protocols, including: EtherNet/IP, Profinet, MC Protocol and Modbus/TCP.
Key Points
- A permanent two-dimensional (2-D) code, known as a Direct Part Mark (DPM), is used to track a part through its lifecycle
- The Data Matrix ECC200 is very flexible as it offers 24 square formats and six rectangular formats
- Data encoding refers to the amount of information that is 'stored' within the generated Data Matrix code
- View Images & Overlay Graphics
- Breaks down barriers between deep learning & traditional vision
- Vision system makes 3D inspection as easy as 2D vision
- A 3D vision system for all cases
- Optimise tracability
- Entry-level vision system
- 100% accurate barcode verification
- Connectivity For Vision & ID Applications
- Cognex acquires deep learning solutions specialist
- Heinz sees 100% read rates