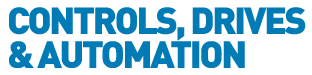
![]() |
Charlotte Stonestreet
Managing Editor |
Home> | POWER TRANSMISSION | >Bearings | >iglidur on tour |
Editor's Pick
iglidur on tour
27 March 2014
To celebrate 30 years of its iglidur materials, igus has sent a small car equipped with iglidur plain bearing components on a round-the-world tour.
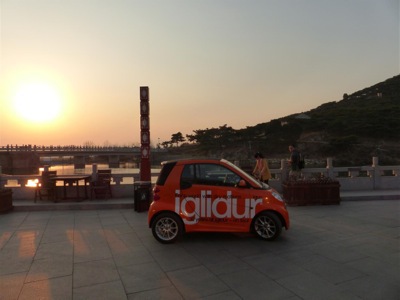
Putting the resilience and potential of its tribo-polymers to the test, the car, with its recognisable igus orange livery will travel across four continents on different road conditions, ranging from the smooth tarmac we’re used to in the UK to muddy tracks.
"Low-friction and self-lubrication is the modern solution for a wide range of moving applications,” says Rob Dumayne, director at igus. "To continuously improve our products, we have been conducting research in this area during these three decades using our in-house test laboratory, the largest in the sector.”
The iglidur equipped car will help spread the company’s motto – ‘plastics for longer life’ – throughout the world, travelling first to India, then China. Further Asian countries of Japan, South Korea and Taiwan will then follow before the car makes the crossing to North America for a coast-to-coast tour through Canada and the USA. The route plan then returns to Europe. Every stop and every kilometre can be tracked in detail at: blog.igus.co.uk
Specific features insensitivity to dust and dirt, pressure resistance and attenuation make iglidur plain bearings especially suitable for the use in the chassis, engine compartment and gearbox. For door hinges and other moving applications, iglidur is equally well-suited as it is corrosion-free, self-lubricating and silent. Meeting industry demand for lightweight construction, these low-weight, plastic parts also help contribute to reducing overall fuel consumption. In addition to this, they are cost-effective and offer economic solutions for mass production runs.
To prepare the car for this ambitious practical test, it was first retrofitted by a team from Cologne University of Applied Sciences under the leadership of Johannes Thomé and the igus bearing developer Michael Krug. The aim was to replace everything possible with igus plastics – in so far as technically feasible and permitted by TÜV regulations. The metal bearings on the brake pedal, windscreen wipers and window lift mechanism, along with the shift unit, seat console, handbrake and alternator were replaced with pure polymer iglidur bearings. Also replaced with the iglidur bearings was the throttle valve and the convertible roof mechanism.
Many modules had to be disassembled and rebuilt to factory and functional specifications. Although standard plain bearings could often be used, in some cases CAD modules were needed to create carefully customised spare parts. The components were then milled or turned from iglidur stock bar; this involved the use of several of the 45 different iglidur catalogue materials being installed at a total of 56 bearing points. Attention was even paid to ensuring visual likeness, for example in the case of the seat locking mechanism.
"More and more manufacturers supplying the automotive industry are discovering the qualities and potential of these high-performance components made from igus tribopolymers, a trend that will become even greater in the future,” asserts Dumayne. "This is because maintenance and corrosion-free polymer plain bearings that require no external lubrication, and weigh seven times less than metallic rolled bearings, speak for themselves - they are kind on both the environment and the pocket as they reduce production costs and offer a longer service life thanks to their wear resistance.
"In vehicle interiors, they are the ideal solution for dampening noise,” continues Dumayne. "At the same time, however, their robust structure and resilience make them equally predestined for ‘outdoor use’, which will be clearly manifested when they encounter the many weather conditions, high altitudes and road types along their journey. The range of potential uses has far from been exhausted and perhaps the polymer-bearing-packed car’s demonstration trip around the world will inspire developers to come up with further new and exciting ideas and concepts.”
- Two-component injection-moulded bearings
- igus makes e-chain recycling even easier
- From AI to heat recovery – igus launches 190 new products
- Low-priced delta robot
- manus award 2023 open for entries
- Lighter linear guide
- Connect & go
- Lubrication-free bearings for heavy industry
- Automated coupling
- The rise & rise of linear robots