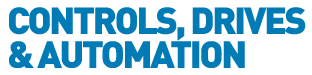
![]() |
Charlotte Stonestreet
Managing Editor |
Home> | POWER TRANSMISSION | >Bearings | >World's Largest Bearing Test Rig Now Operational |
ARTICLE
World's Largest Bearing Test Rig Now Operational
19 October 2012
After less than two years, The Schaeffler Group has successfully completed the design and build of the world’s largest, most powerful test rig for large size bearings at its Schweinfurt plant in Germany

The ‘Astraios’ test rig – named after Greek myth, Titan, who fathered the four wind gods – enables large size bearings weighing up to 15t with outside diameters up to 3.5m, particularly those used in wind power, to be fully tested in realistic conditions using a comprehensive simulation programme.
At a cost of around €7m, Astraios is a significant investment but will enable Schaeffler to help reduce wind turbine development times for customers, as well as improve the reliability, safety and cost effectiveness of future wind turbine designs.
Astraios will be primarily used to test rotor bearings for multi- Megawatt wind turbines and will help to further improve the understanding of wind turbine systems, the influencing factors and the interrelationship between drive train components. The tests will also provide useful insights into wind turbine operation and maintenance, as well as information on how to optimise the design of any adjacent constructions.
The test rig will perform realistic simulations of static and dynamic loads that act on the rotor bearings and slewing rings. All rotor bearing concepts for wind turbines with an output of up to 6MW can be tested on Astraios. Functional tests will provide insights into rolling bearing kinematics, temperature and friction behaviour, loads and deformation.
The data required for these tests will be provided by more than 300 different sensors mounted on the test rig and in the bearings.
The loading frame is the most important part of the test rig. Four radial and four axial hydraulic cylinders are fixed to this frame, which generate the real loads and moment forces that occur in a wind turbine. The radial cylinders simulate the weight of a rotor hub with rotor blades, while the axial cylinders generate the wind loads.
The rotors and hub on a large wind turbine can weigh in excess of 100t.
This weight acts on the bearing and generates a static radial load and a static ‘nodding’ moment. Accordingly, the four radial cylinders have extremely large dimensions, as each cylinder can generate a maximum of one mega Newton of force, which is equivalent to 100t of weight.
At a cost of around €7m, Astraios is a significant investment but will enable Schaeffler to help reduce wind turbine development times for customers, as well as improve the reliability, safety and cost effectiveness of future wind turbine designs.
Astraios will be primarily used to test rotor bearings for multi- Megawatt wind turbines and will help to further improve the understanding of wind turbine systems, the influencing factors and the interrelationship between drive train components. The tests will also provide useful insights into wind turbine operation and maintenance, as well as information on how to optimise the design of any adjacent constructions.
The test rig will perform realistic simulations of static and dynamic loads that act on the rotor bearings and slewing rings. All rotor bearing concepts for wind turbines with an output of up to 6MW can be tested on Astraios. Functional tests will provide insights into rolling bearing kinematics, temperature and friction behaviour, loads and deformation.
The data required for these tests will be provided by more than 300 different sensors mounted on the test rig and in the bearings.
The loading frame is the most important part of the test rig. Four radial and four axial hydraulic cylinders are fixed to this frame, which generate the real loads and moment forces that occur in a wind turbine. The radial cylinders simulate the weight of a rotor hub with rotor blades, while the axial cylinders generate the wind loads.
The rotors and hub on a large wind turbine can weigh in excess of 100t.
This weight acts on the bearing and generates a static radial load and a static ‘nodding’ moment. Accordingly, the four radial cylinders have extremely large dimensions, as each cylinder can generate a maximum of one mega Newton of force, which is equivalent to 100t of weight.
MORE FROM THIS COMPANY
- Plummer block housed
- Bearings On Mars Curiosity
- Deep groove ball bearings
- Coatings prolong bearing life
- Schaeffler acquires controlling share of Compact Dynamics
- World's most powerful wind bearing test facility
- Schaeffler acquires ECO-Adapt SAS
- Schaeffler acquires Ewellix Group
- Schaeffler acquires remaining shares in Compact Dynamics
- Checks bearing authenticity
OTHER ARTICLES IN THIS SECTION