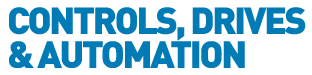
![]() |
Charlotte Stonestreet
Managing Editor |
Home> | POWER TRANSMISSION | >Bearings | >Things It's Worth Bearing in Mind |
Things It's Worth Bearing in Mind
19 October 2012
With engineers often having to specify suitable rolling bearings for a variety of rotating machinery and automated production systems, Dr Steve Lacey, engineering manager at Schaeffler (UK) gives some tips on selection
Whilst some engineers may think they have the required experience and knowledge to design the shaft bearing arrangement, this could result in an over-engineered solution that is not cost effective. Or worse, the bearings may simply fail to fulfil the functions required of the shaft.
In order to determine the correct shaft bearing arrangement, several factors need to be considered. First, engineers need to consider how precisely the shaft needs to be guided. Are there any external constraints or forces that could be eliminated by the correct shaft bearing arrangement using appropriate degrees of freedom? Is shaft deflection likely? Will there be significant thermal elongation when the operating temperature is reached? Is the shaft itself driven or does it drive another component? Will the shaft be affected by vibration? Should allowances be made for any shaft misalignments?
For example, a different bearing arrangement with two tapered roller bearings or angular contact ball bearings, mounted in either "O” or "X” arrangement, may offer precise shaft guidance, but may also exert additional forces on the shaft and bearing system due to the internal axial forces caused by manufacturing inaccuracies in the housing, internal and external spacer and shaft components.
The designer may be able to solve this by using "NJ” type cylindrical roller bearings with a defined axial clearance. The classic locating (fixed)/non-locating (free) bearing arrangement on the other hand, may be able to compensate for manufacturing inaccuracies, as well as any thermal expansion that may occur between bearing centres due to differences between the housing and shaft temperatures.
OPERATING CONDITIONS
The type of application and the conditions in which the bearings are expected to operate will usually determine the bearing arrangement and the types of bearings that are selected. A bearing arrangement with tapered roller bearings, angular contact ball bearings or even "NJ” type cylindrical roller bearings can support unidirectional axial loads.
The locating/non-locating bearing arrangement will require a bearing at the locating or fixed position that can support axial loads in both directions. Where this is the case, the designer can select radial ball bearings, spherical roller bearings or "NJ” type cylindrical roller bearings used in conjunction with an angle ring. The function of the non-locating i.e. "free” bearing position is to support radial loads only. This can be achieved by the selection of a radial ball bearing or a spherical roller bearing mounted in a housing that will allow the bearing outer ring to move axially, i.e.
"float”. It is also possible to achieve axial movement at the nonlocating bearing position by the use of bearings such as an "NU” type cylindrical roller bearing and certain needle roller and drawn cup type bearings.
For any application, the design envelope and load direction are not sufficient as a means of selecting a suitable bearing. The required life and operating conditions raise numerous questions that can either confirm or reject the bearing selected. Other important questions need to be asked such as: How long must the bearing last? Will it support the necessary speeds? Do the lubricants used for the shaft system fulfil the requirements of the rolling bearings? This is where a good bearings supplier can advise the customer into selecting the best bearings for the application. The designer can learn how load, speed, internal stresses in the bearing material, lubricant viscosity and cleanliness, as well as the size and hardness of contaminant particles, additives and environmental conditions, affect the expected life of the bearings.
Key Points
- To determine the correct shaft bearing arrangement, several factors need to be considered
- The type of application and the conditions in which the bearings are expected to operate will usually determine the bearing arrangement and the types of bearings that are selected
- Schaeffler destroys fake bearings
- Linear profile rail system replacement
- Increases bearing life
- Innovations for all-electric & hybrid vehicles
- Innovative components for LWRs and cobots
- New generation of rolling bearing housings
- Schaeffler supplies its largest spherical plain bearing
- Sensor technology integrated into spindle bearings
- SBTi validates Schaeffler Group's emissions targets
- Optimum lubrication for linear guides results in longer machine operating times & reduced maintenance