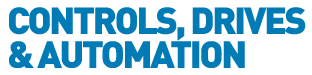
![]() |
Charlotte Stonestreet
Managing Editor |
Home> | INDUSTRY FOCUSES | >Automotive | >Drive to improve efficiency & reduce emissions |
Drive to improve efficiency & reduce emissions
29 April 2014
As the automotive sector looks to encourage growth and sustainability, CDA takes a look at comes of the latest developments in both the manufacturing processes and the vehicles themselves
If there is one industry sector that never seems short of investment or the resulting innovation, it's automotive. With brands that are amongst the most recognised worldwide and a truly global market in terms of both manufacturing and customer base, there are plenty of high profile news stories around to spark interest in not just the business side of the industry, but also the technology side as well. Think, for example of Googles's autonomous car, or the Terrafugia TF-X flying car (yes, really!)
In common with all industries, development in the automotive sector today is being driven by the rising costs of fuel and the need to reduce environmental impact. Addressing these issues, the UK government, alongside alongside automotive manufacturers Ford, Cummins, GKN and JCB will invest £133 million in powertrain development projects to improve fuel efficiency and reduce carbon emissions.
The investment, part of government and industry’s £1 billion Advanced Propulsion Centre (APC), was announced by Business Secretary, Vince Cable on a recent visit to Ford’s Dunton facility.
Cable said: "The next generation of cars, buses and diggers will be powered by radically different technologies and I want them to be developed here in Britain.
"Over the last few decades the British car industry has been transformed and today a new vehicle rolls off a UK production line every 20 seconds.
"To capitalise on the success of our motor industry these projects will be the first of many to receive funding from the new £1 billion Advanced Propulsion Centre (APC) which we set up to turn technologies into products."
The APC aims to transform the UK into a propulsion nation, working as a hub of excellence for advanced powertrain technologies. The initiative has the potential to secure up to 30,000 jobs currently linked to producing engines, while creating many more in the automotive supply chain.
Electric drive module
Although by no means achieving the ubiquitousness of the traditional IC engined vehicle, hydrid electric models have non-the-less entered the mainstream and are a fairly common sight on the roads. Indeed, according to research carried out by the Centre for Solar Energy and Hydrogen Research Baden-Württemberg (ZSW) the number of electrically powered automobiles worldwide climbed to just over 400,000 in early 2014, with the vehicle count doubling last year alone.
Addressing this growing market, searings and automotive component and systems supplier Schaeffler has developed a range of innovative systems for future passenger vehicles equipped with onboard high-performance 48-volt electrical systems.

Schaeffler asserts that the drive module paves the way for the economical hybridisation of vehicles. The low-voltage design reduces costs compared to high-voltage solutions with their associated requirements. This economical hybridisation allows significant advances to be made in terms of increased drive efficiency, as the use of a 48V electric system opens up operational possibilities that were previously the exclusive domain of vehicles equipped with high-voltage hybrid components, including "crawling” in traffic jams – electrically powered driving in dense inner-city traffic, i.e. moving off, driving at low speeds, and parking using electric power. In addition to electric ‘boosting’ during starting and electric ‘sailing’ – a driving mode in which the electric motor ensures constant speed while the internal combustion engine is switched off – the system also enables recovery and storage of energy during deceleration, which is key in terms of reducing fuel consumption.
The electric drive, which has an output of up to 12kW, acts as the hybrid vehicle‘s sole source of power when "crawling” in stop-and-go traffic. The electrically generated propulsion of Schaeffler‘s 48V drive module is also sufficient for driving in residential areas, parking in garages and for other low speed driving situations. This is also true of the comfortable driving mode known as "sailing”, in which the electric motor ensures virtually constant speed across a wide operating range while the internal combustion engine is switched off. The electric drive assists the internal combustion engine by providing additional torque, or "boosting”, for example, when moving off from traffic lights.
The high performance of the 48V system also means that the drive element opens up new potential for energy recovery. Due to the higher recuperation capability, the kinetic energy released during deceleration is now no longer converted into heat that subsequently dissipates – as was previously the norm – but is instead fed back into the onboard electric system in the form of electrical energy. Therefore, a hybrid solution with combustion engine and 48V system proves to be advantageous when generating electricity from braking energy.
Fuel economy increase
Developer of magnetic transmissions and ultra compact motors, Magnomatics has announced successful evaluation results for its innovative MAGSPLIT device.
Tested by a number of global car, bus and truck manufacturers, results in smaller vehicles have shown a fuel economy increase between 3% and 5% compared to current hybrid technologies. Testing has also shown a reduction of up to 35% in fuel consumption in some larger HGV vehicles.

MAGSPLIT and MAGSPLIT 2 are power-split devices that combine the functionality of a magnetic gear and a motor generator in one compact unit, for use in a hybrid power train.
Compared to a conventional hybrid engine system that combines the engine with an electric motor and planetary gear, magnetic gears are known to be more efficient and reliable. For this reason, major manufacturers within the automotive sector are reported to have begun to evaluate the benefits of the MAGSPLIT technology.
A contactless system, MAGSPLIT greatly reduces maintenance costs once installed. It also substantially improves the system efficiency and consequently fuel economy of hybrid engines compared to the mechanical gear and motor/generator combination found in many of today’s hybrids.
iProcell
Along with innovation in the vehicles themselves comes development in the way that they are produced, as demonstrated by IBG / Goeke Technology Group at the recent Hanover Trade Fair with its iProcell, a flexible, fully automatic assembly cell for electrical vehicles.
Matthias Goeke, managing partner of the IBG/Goeke Technology Group, explains: "The innovative production process guarantees the entire process chain from unloading of the container to finished assembly. The modular iProcell assemblies are supplied on compact pallets. From this point on, three robots take over the whole final assembly process. The robots identify the assemblies, take them off the pallets and finally assemble them into an electric vehicle.”
Vehicles are assembled with iProcell in an optimised sequence, significantly reducing mounting time, while a stringent system of equivalent parts helps minimise the variety of components and number of required manufacturing tools.
"Through the optimised use of equivalent parts, both CO2 impact on the environment and manufacturing costs of the required secondary production processes can be reduced," says Goeke.
Piston-ring inspection
For the past few years, Renault's site in Cléon, France, has been using Keyence's LJ-G laser displacement sensors on its G9 engine production line. The site chose the sensors for their detection reliability and ease of use.Opened in 1958, Cléon is the Renault Group's main powertrain site, manufacturing the automaker's gearboxes and engines. A cornerstone of the Renault-Nissan Alliance, it has been rolling out the first engine designed by the alliance since 2005. Renault's 2.0 16V (F4R), 1.9 dCi (F9Q), 2.5 dCi (G9U), 2.0 dCi (M9R), 2.3 dCi (M9T), V6 3.0 dCi and 1.6 dCi (R9M) engines are produced at Cléon.

Piston rings have open ends that are spread apart to allow them to be slid into grooves specially machined on engine pistons. At Cléon, this is done by an operator, who then places the fitted pistons on pallets. These pallets are moved to an automated inspection platform where four pistons are simultaneously checked by four LJ-G sensor heads. A profile is generated for each piston and compared against a ringless profile to ensure that the rings are in place. Because piston rings play a crucial role in engine operation, they must be inspected to ensure that they are properly fitted.
In addition to their main purpose of preventing combustion gases from entering the engine sump and causing a loss of gas pressure and thus a loss of engine power, they also must prevent lubricants from migrating from the engine to the combustion chamber and coat each cylinder with a well-defined layer of lubricant. Each piston is fitted with three rings: an oil ring, a sealing ring and a compression ring. The ultra-thin oil ring is the hardest to inspect and the 3 mm compression ring is the easiest to inspect. Each ring must be inspected to make sure it is indeed fitted and properly in place.

"Our priority in designing this inspection was to not be tied down by the measurement conditions and to reduce false defects to a minimum," says Patrick Guehennec, industrial resources officer at Renault's methods department. "We had thought about a vision system, but there were too many lighting issues and it was hard to get a sharp image."
The Cléon site therefore chose Keyence's LJ-G laser displacement sensor. "It was very easy to set up and we liked its user-friendliness," continues Patrick Guehennec. "Overall, the laser profile obtained with the LJ-G allows perfectly stable detection regardless of the lighting conditions or surface type."
The LJ-G is an efficient quality control solution in that detection is stable regardless of reflections and light conditions. It features a unique E3-CMOS sensor that compensates for light intensity and has a dynamic range that is 300 times wider than that of conventional sensors. E3-CMOS (Enhanced Eye Emulation CMOS) technology replicates the accommodation function of the human eye and creates complete digital reproductions of surface profiles despite dark or overly bright areas. This gives the LJ-G unparalleled measurement stability, even with complex surfaces such as elastomers and metals. In addition, the MFL function adjusts the CMOS sensitivity, the laser intensity and the exposure time (the darker the target, the longer the sampling time and vice versa).
It remains simple to use: these functions are automatically set and the LJ-G features a straightforward and easy-to-use setup menu.
Although the smallest ring inspected measures just one millimetre thick, the LJ-G's accuracy of a few microns ensures problem-free detection. Lastly, with a sampling speed of 3.8 ms, the LJ-G boasts ultrafast detection and can handle most production rates.
Turbocharger sensor
Suitable for use in both test cell environments and for on-vehicle testing of turbochargers, Micro-Epsilon has launched a new turbocharger speed and temperature sensor system. Enabling measurements on turbocharger blades made from aluminium or titanium, the turboSPEED DZ140 operates on the eddy current non-contact measuring principle and so is resistant to oil and dirt – a major advantage over optical speed measurement systems.
The system is robust, compact in dimension, with a 3mm diameter sensor and a controller that weighs just 85g. This allows the sensor and controller to be installed in engine compartments where space is tight.

As well as being able to measure the rotational speed of a turbocharger, the DZ140 also enables the user to measure the temperature of the sensor head/tip – said to be an industry first. This new feature is particularly useful as it allows the user to monitor the temperature inside the turbocharger without having to fit a separate thermocouple.
The robust controller extends the maximum distance allowed between the controller and sensor to 10m. During development of the turboSPEED DZ140, the primary focus was placed on resistance to electromagnetic interference, which means the system is more reliable for multiple test cell environments and for on-vehicle testing.
Key Points
- £133m investment in powertrain development projects to improve fuel efficiency and reduce carbon emissions announced
- Schaeffler develops range of innovative systems for future passenger vehicles equipped with onboard high-performance 48-volt electrical systems
- Magnomatics has announces successful evaluation results for its innovative MAGSPLIT device
- IBG/Goeke Technology Group shows iProcell, a flexible, fully automatic assembly cell for electrical vehicles, at Hanover
- Renault's site in Cléon, France, uses Keyence's LJ-G laser displacement sensors on its G9 engine production line
- Micro-Epsilon launches new turbocharger speed and temperature sensor system
- Intelligent automation & personalised healthcare
- Funding for food suply chain automation announced
- Fast and reliable automated tyre inspection
- BCIA releases new Technical Guide: The Impact of Controls on the Energy Efficiency of Buildings
- Robots-as-a-service for manufacturing industry
- IOActive finds security vulnerabilities in home, business & industrial robots
- Multi-axis stepper drives
- Real-time inventory visualisation
- Engineering recruitment exhibition
- Security holes identified in SCADA product