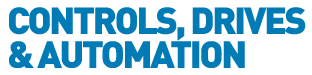
![]() |
Charlotte Stonestreet
Managing Editor |
Editor's Pick
When two-speed motors are the best solution
22 July 2014
Two-speed motors are an often-overlooked technology, but they can be the ideal choice of prime mover when robustness, simplicity and low cost are required, alongside operational flexibility. Jerry Hodek of Rotor UK explains where they fit into the spectrum of drives solutions.
Variable-speed inverter drives have done much to improve machine design since they became commonplace about 30 years ago. They have allowed operational optimisation through speed trimming and enhanced controllability, and contributed massively to saving energy.
However, they have also been responsible to a degree for engineers forgetting the benefits of two-speed motors. On the face of it, an infinitely variable motor and drive combination appears to be better than a motor that provides only two-speed settings. However, in certain circumstances, a two-speed motor is still the better choice, and likely to remain so for a long, long time. Indeed, industry-wide sales figures suggest that their take-up is actually growing at a rate faster than industrial motors in general, so we can conclude that engineers are already beginning to recognise their advantages.
It seems likely that they are finding favour on fan and pump drives to give ‘high’ and ‘low’ flow rates. There are also any number of situations where predictable peaks and troughs are experienced: for instance, a passenger lift or escalator may have a normal running speed and a rush-hour speed; a conveyor feeding raw material into a piece of process machinery may have two speeds to even out light and heavy loading; water and wastewater supply have definite peaks at certain times of day; cranes and winches can benefit from a choice of fast or slow speed, as can ventilation fans.
There are two basic types of two-speed motors: dual winding and pole changing, plus a third ‘hybrid’ type.
A dual wound rotor appears at first glance to look just like a conventional fixed speed motor, most notably by having a single winding. But closer inspection shows that there are in fact two windings, each individually connected to the power supply. A pole changing motor looks even more like its single-speed cousin, but has twice the usual complement of magnetic poles. The wiring is such that alternating magnets are arranged into two separate sets, therefore either half of the poles or all of them can be energised at one time.
A hybrid motor combines both twin pole sets and dual windings, a configuration that gives four set speeds. However, this type of motor is rare, because a standard inverter fed motor will be cheaper to buy and maintain, and will have the enhanced functionally of an electronically controlled drive.
Let us look at the construction of dual rotor and pole change motors in more detail.
Dual rotor
The dual winding motor is the simpler to understand and also simple – and therefore cheaper – to make. The motor has two separate windings, whose polarities are opposite, within a single lamination pack. It should be noted that the windings don’t have to be equal in size; they can have markedly different power ratings. The two-speed capability is achieved by having a switch that energises one or both windings.
Pole change
Like many slightly unusual engineering components, the pole change motor has many alternative names including switch pole, tap wound and Dahlander; essentially they are all different names for the same thing. A pole change motor consists of a single winding with two stators (sets of poles). One set of poles is permanently connected to the power supply; the other uses tapped leads so that they can be screwed in and out of connection with the power supply. In operation, the high-speed setting is double the revolutions per minute of the slow-speed setting.
Selection
When selecting a two-speed motor, there is an issue of potential misunderstanding that has confused many a good engineer! It is simply that they are specified with one of three types of output: constant torque, variable torque, or constant power. Users must identify the type of load to be driven, and then select the appropriate motor.
A constant torque load is one where the speed may vary, but the torque demand is always the same. Perhaps the most common constant torque load is to be found on a conveyor whose speed can vary markedly, but whose torque is (largely) constant. It is also found on extruders, positive displacement pumps in closed-circuit hydraulics and some types of specialist machinery.
Variable torque is typified by fans and centrifugal pumps, where the torque requirement is low value at slow speed and high value at high speed. In fact, the torque requirement increases far faster than the speed, so on a fan, for instance, doubling the speed will quadruple the torque (which increases the power requirement eightfold – 2 x 2 x 2 = 8).
The third type of load is the constant power load, and is seen by many as the most logical. If the speed is doubled the torque is halved so that power remains constant. Perhaps oddly, this is quite difficult to achieve with a two-speed motor, and in most cases an inverter setup is probably going to serve the application far better.
In conclusion, we can say that there are many niches where a two-speed motor is a good choice. Many engineers already know this, but others should not fall into the lazy habit of assuming an inverter is the only answer. Likewise, there are occasions when two-speed motors should not be considered.
- Roller table motors for harsh applications
- EXTENSIVE STOCK & RAPID DELIVERY
- Motor starting methods
- Washdown Motors
- Are inverter-rated motors essential: YES or NO?
- Surpass European Efficiency Levels
- Drip-proof motors
- Trouble shooter’s guide to motor maintenance & repair
- In it for the long run
- Grease: how to avoid economic meltdown