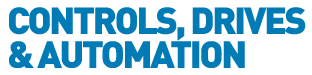
![]() |
Charlotte Stonestreet
Managing Editor |
Home> | DRIVES & MOTORS | >Electric Motors | >Comparing motor efficiencies |
Comparing motor efficiencies
24 April 2015
Many plant engineers are confused about measurement of their motors’ efficiencies and some motor suppliers are making matters worse. Bill Bertram of Marathon Electric, says the problem began seven years ago and has a simple solution
National governments and the European Union are encouraging the adoption of energy efficiency in many fields, including electric motors as a way of battling global warming. Initiatives they have undertaken include passing new legislation, preparing new industry standards and developing new technologies to improve motor efficiency. The reasoning here is that even small gains will reap big rewards because so much power is used to drive electric motors (70% of all power produced is the generally accepted figure).
To this end, a new and more demanding method of testing motor efficiency was introduced in 2007. I think a major mistake was made when its designation, IEC 60034-2-1 : 2007, was chosen, because it is so similar to its predecessor’s designation, IEC 60034-2 : 1996. People tend to speed-read and skip over long numbers, so many will not even have noticed that there is new legislation, while those that have may well assume one is only a minor update of the other.
However, in practice, if you were to test the same motor using both regimes, you would get a discrepancy of generally 1% to 1.5%, but possibly much higher. In the world of motor efficiency, this difference is very significant – given that many motors run long hours over many years, the cumulative effect is the consumption of an enormous amount of extra energy (with a corresponding addition to the user’s utility bill, especially as most industrial plants use a large number of motors).
There is a further complication in that industrial motors are now classified by their energy efficiency and both the nomenclature and the technical specification for the classes has changed. Further the acceptability of the less efficient classes is being phased out in a number of steps. Therefore, plant engineers can find themselves being told that a motor that was say 88% efficient is now 86.5% efficient, or that a different efficiency classification now applies. It can be very confusing!
The main difference between the old Standard and the new is that originally there was a fixed assumption that ‘stray losses’ would be equal to 0.5% for all motors, whereas now, they are individually calculated. Because stray losses increase with the load on the motor, actual losses are nearly always much higher than the old assumption (typically 3 to 5 times higher under the sort of load conditions normally experienced with industrial drive systems!).
The efficiency of an electric motor is the ratio between the output power and the input power. The former is mechanical and is the torque/speed of the rotating output shaft; the latter is electrical. As they are both powers, they are measured in watts (metric) or horsepower (imperial) and so can be directly compared.
ηm = Pout / Pin
where
ηm = motor efficiency
Pout = shaft power out (Watt, W)
Pin = electric power in to the motor (Watt, W)
Pin = electric power in to the motor (Watt, W)
Output power is always less than input due to losses or inefficiencies in the motor’s operation. Electrical power lost in the primary rotor and secondary stator windings due to resistance are called copper losses and vary with the load compared to the square of the current squared
Pcl = I2 R
where
Pcl = copper loss
R = resistance
I = current
Iron losses are magnetic inefficiencies, energy that is dissipated from the motor’s magnetic field during operation.
Mechanical losses include friction in the bearings and air resistance to the cooling fan.
Stray losses account for further inefficiencies after the copper, iron and mechanical losses have been accounted for. These result from harmonic energies generated when the motor operates under load.
Deeper understanding
While the explanation above is likely to be enough for most motor users, a more detailed review will help engineers appreciate the background and anticipate future changes that may occur in the field.
Comprehensive legislation has been passed by the European Union to reduce energy consumption and thereby greenhouse gas emissions. Similar new legislation has also been enacted, or is being brought in, in other regions, in line with the Kyoto Accord and other international agreements.
Prior to these developments, motor efficiency could be low, unpredictable and unregulated. OEMs (original equipment manufacturers) could often get away with fitting the cheapest motors to their equipment and not worrying about efficiency. In other cases many fan and pump drives ran continuously with excess flow being ‘dumped’ by a valve or louvers. Similarly, building service engineers often did not fit variable-speed controllers to ventilation fan motors, so the fans ran at maximum speed at all times (louvers gave local control by allowing occupants to divert local flow, while ‘control panels’ in individual rooms were often simply dummies!).
Energy consumption in relation to the efficiency of induction motors used in industrial situations anywhere in the European Union is addressed in EU Regulation 640/2009. This is based on the International Standard IEC 60034-2-1 : 2007, which itself is subject to updates and developments. This Standard did away with the previous efficiency rates of EFF1, EFF2, etc. and replaced them with a new IE – International Efficiency – system. It defined four classes:
- IE1 (Standard Efficiency)
- IE2 (High Efficiency)
- IE3 (Premium Efficiency)
- IE4 (Super Premium)
As well as the new method of classification, the way in which efficiency is measured was changed to properly account for stray losses. Previously, a figure of 0.5% was used to cover all stray losses under any operating conditions. While this sort of assumption was acceptable in the 1980s and 1990s when people were less concerned about carbon dioxide emissions, it became increasingly inadequate as the new millennium progressed and moves to control global warming gained momentum.
Under the new regime, the stray losses are actually measured for each motor and are often found to be 1% to 2%. This meant that many motors were reclassified as less efficient than previously thought (and adding to the confusion, typical reclassifications could be from EFF1 to IE2 or EFF2 to IE1).
It is therefore difficult to make an efficiency comparison between motors manufactured in the past and newly supplied motors as the efficiencies displayed on the rating plate are not directly comparable whilst different efficiency calculation method was used in the past to the method used at present. Various payback calculators exist on certain websites but again if the efficiency calculation method was not identical, the efficiency comparison and payback calculation would be incorrect. In simple terms old motors would have lower efficiency than the one published on the rating plate if we tested them today.
Another area of confusion has been caused by the apparently simple changes to the information provided on each motor’s rating plate. For instance, a specific rated voltage replaces the previous nominal voltage range (e.g. 400V instead of 380V – 420V); efficiency rating is to the new Standard and in the new nomenclature; the rated current value changes as a result of the lower efficiency value. While this may seem straightforward when discussed academically, it has caused considerable confusion in the field when users or engineers have not fully appreciated the changing situation.
Exceptions
Naturally, no International Standard or EU regulation would be complete without a whole raft of exceptions and special cases, some of which are listed below:
- Submersible motors
- Motors that are completely integrated with the driven machine, such as some pumps and fans
- High altitude motors (+4,000 metres above sea level)
- Motors designed to operate in ambient temperatures outside –30°C +60°C
- Motors designed to operate in ambient temperatures below -15 °C
- Motors operating in officially defined hazardous areas
- Brake motors
- 8-pole motors
- Pole-changing or two-speed motors
- Synchronous motors
- Single-phase motors
While this can all seem to be mind-numbing and pointless, it is worth noting that good quality motors are at least 25% more efficient than they were 25 years ago, so the technology is advancing and new legislation is encouraging this to continue. It is also significant that motors have a very long working life (often measured in decades), so even a small improvement in efficiency will provide a steady contribution to the overall bottom line via reductions in the utility bills – and the savings can be multiplied by the number of motors running in a given plant.
While new legislation is driving the adoption of energy efficient motors, plant owners are of course also free to voluntarily swap old inefficient motors for new more efficient ones. There are real gains to be made in terms of reduced running costs, products may earn a ‘green’ designation and thereby open up new markets and the positive effect on the environment may help in attaining general environmental standards.
Green future
It is inevitable that environmental and energy efficiency requirements will tighten further over the coming years and that new regulations will come into force. For instance, from 2015, inefficient process controls, e.g. throttle valves will have to be replaced by energy-saving solutions by law, while ways to encourage the wider installation of variable-speed drives to existing driven systems will unfold.
Key Points
- Industrial motors are now classified by their energy efficiency – the nomenclature and the technical specification for the classes has changed
- Under new standards ‘stray losses’ are individually calculated, rather than using the assumed figure of 0.5%
- Motors have a very long working life, so even a small improvement in efficiency is significant
- Trouble shooter’s guide to motor maintenance & repair
- Roller table motors for harsh applications
- Washdown Motors
- Drip-proof motors
- Motor starting methods
- Full torque at zero speed
- Surpass European Efficiency Levels
- When two-speed motors are the best solution
- Grease: how to avoid economic meltdown
- For Remote Or Outdoor use
- JOINT WIND ENERGY GENERATORS VENTURE
- Washdown Motors
- Engineering Talent Search
- Cooling System & Frame Optimised
- Sustainable Motors
- WEG motors & drives power high-efficiency air blowers
- Stainless Motors For Washdown Environments
- IECEx Certified
- Configurable Online
- Explaining the different types of AC electric motor