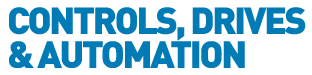
![]() |
Charlotte Stonestreet
Managing Editor |
Home> | AUTOMATION | >Robots | >Transforming manufacturing |
Transforming manufacturing
17 June 2015
For a long time there has been a need by the manufacturing industry to address the inefficiencies associated with the way that humans and robots work together, and FANUC is at the forefront of this thinking as this article from managing director, Chris Sumner, shows
Up until recently robots and employee were separated by large industrial metal cages, as machines did not have the ability to distinguish between objects and workers during the production process. Subsequently this led to downtime during loading and unloading which had an impact on the speed and efficiency of production output.
As a way of solving these inefficiencies, last month saw the launch of the world’s first heavy lifting collaborative robot, the FANUC CR-35iA. Previously only witnessed in the works of science fiction, the robot makes it possible for robots and humans to work hand-in-hand, bringing a variety of benefits to the manufacturing plant floor. Let’s have a closer look at some of these benefits below.
Improvements in safety
Collaborative robots improve the safety of employees removing the need for external safety devices such as metal fences, creating a safe environment for humans to work in collaboration with robots. Safety is ensured through the use of intelligent sensors which automatically stop the robot if it touches a human operator. Safety zones (DCS) within the robot’s workspace are shown clearly and throughout processes. At the same time, the robot retains its full functionality and humans retain full control over robot operation, with its soft coating providing additional protection.
Cost savings
Servicing a variety of manufacturing industries, collaborative robots can perform both simple and complex tasks, allowing cost savings to be made through automation. The removal of metal fences within the manufacturing plant floor eliminating a large cost associated with the amount of space used to house the robots and human workers.
As a result of this, closer working practices increase manufacturing output and productivity, enabling production to be carried out in one long fluid activity, rather than a stop-start process.
Increased versatility & improved human welfare
In cases where simple handling manoeuvres have been carried out by human muscle power, these can now be performed by the robot. Human workers can then be upskilled opening up better and more desirable employment opportunities.
These tasks could involve the application of toxic substances, or the reduction in stress from lifting heavy loads. This improves the welfare of human workers, enabling activity to be executed at a safe pace, decreasing the risk of injury.
Collaborative industries
The automotive industry leads the way in its interest for harnessing the power of collaborative robots, with engine manufacturers and assembly stations key areas where they come into play.
Opportunities currently exist in the areas of loading and offloading machine tools, as well as at packaging stations, where robots can take over handling tasks and human workers can perform inspection, testing, or shipping tasks.
The future
As collaborative industrial automation is implemented across the manufacturing industry, developments will continue to be driven by technological innovation. At the same time, complex adaptive systems and multi-processing will take over from real-time systems, further increasing productivity and profitability for manufacturers.
Improvements in collaborative working practices can make vast improvements to labour conditions, making it healthier and cleaner to work. This gives workers better access to pursue skilled jobs in different areas of the business, providing access to training and career development.
Collaborative robots open up a new era for manufacturing as an indispensable part of production, offering advancements in industry productivity. Further enhancing these machines with vision, force sensors, and artificial intelligence, greatly improves the rate of industrial production making it more cost and energy efficient, and at the same time reduces waste and drives sustainability.
Key Points
- The FANUC CR-35iA makes it possible for robots and humans to work hand-in-hand, bringing benefits to the plant floor
- Collaborative robots remove the need for external safety devices such as metal fences; intelligent sensors which automatically stop the robot if it touches a human operator
- Servicing a variety of manufacturing industries, collaborative robots can perform both simple and complex tasks, allowing cost savings to be made
- Software Options Build Up Basic Robot Profile
- Food handling robots
- Lifts payloads of up to 1.7t
- Hottest automation trends for 2024
- Commitment needed to change UK culture around automation
- Wake-up call for UK manufacturing
- Robotics curriculum to inspire future engineers
- Building a successful partnership
- UK Government warned about lack of automation in manufacturing
- FANUC’s chief technical advisor elected IFR president
- Balls to Gravity
- ROBOTS GIVE FASTER CELL TOOL CHANGE TIMES
- ROBOT FOR DELICATE ASSEMBLY
- NUMBER OF ROBOTS IN UK ON THE RISE
- The future is bright - The future is automation!
- High Demand For Grant
- More Capacity, Less Space
- FREEBIRD - THE THIRD DIMENSION
- PRECISION ROBOT CELL FOR THE PHARMACEUTICAL INDUSTRY
- ROBOT SALES REACH ALL TIME HIGH