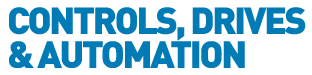
![]() |
Charlotte Stonestreet
Managing Editor |
Home> | INDUSTRY FOCUSES | >Food & Beverage | >Robotic pot swap |
Home> | AUTOMATION | >Handling & Logistics | >Robotic pot swap |
Home> | INDUSTRY FOCUSES | >Materials Handling | >Robotic pot swap |
Editor's Pick
Robotic pot swap
01 October 2015
In response to rising retailer demand for mixed product trays, FANUC has collaborated with integrator Pacepacker Services to engineer a robotic pot swap tray loading system.

The robotic pick and place unit combines FANUC’s LR Mate200iD robot with Pacepacker’s new Mixed Tray Loader (MTL) technology, providing a flexible and compact solution for generating the assorted trays of product that are increasingly being requested by retailers.
"The trend towards pallets of mixed products, driven by retailers requiring smaller, more frequent deliveries, is now being extended to case level. Mixed trays or cases allow supermarkets to offer a broader choice of product sizes, flavours and variants and to keep their shelves replenished without having to hold a lot of stock. Equally, convenience and inner-city stores are finding that mixed cases or trays allow them to offer a far wider product range on restricted shelf space,” says John Rainer, regional sales manager, FANUC UK, explaining the rationale for the launch of the robotic product swap unit.
The unit is based on Pacepacker’s MTL technology, which was developed last year for a private-label dip producer looking to generate mixed trays. Until now, the MTL has only been supplied in conjunction with a cartesian pick and place system. The development of a robotic mixed tray loader will give potential users far greater flexibility owing to the freedom of movement afforded by a robot arm.
"If producers want to swap pots between three, four, or five different trays, a larger working envelope will be needed, and that is only viable with a robot. A robot is also more future-proof as it offers far greater programming flexibility and movement control than a cartesian arrangement. Say a producer wants to introduce a new pot design or has a range of tray or pot sizes, our LR Mate200iD robot will easily accommodate this,” explains Rainer.
Indeed, one of the main reasons for selecting the LR Mate200iD for this project was its dexterity; the six-axis articulated arm can tilt, twist and rotate single or multiple products with ease at speeds of up to 80 packs per minute. This dexterity combines with a reach of up 900mm to offer a "best in class" work envelope and unrivalled breadth of application - the robot can even place products in deep trays or cases with lipped edges.
Another feature that made the LR Mate200iD particularly suitable for integration with the MTL was its diminutive dimensions; the ‘mini’ robot arm is human arm sized and the lightest mechanical unit in its class, weighing in at just 25kg. When supplied with FANUC’s DCS safety software, which is demonstrated combined with Rockwell’s laser scanner technology to produce a small-footprint solution offering very flexible configuration to suit what might be limited factory floor space, with the added benefit of portability if required.
"The LRMate 200iD was designed as a versatile solution for manufacturing operations that require access into tight spaces. It is the smallest of all articulated arm robots, making it ideal for compact cells such as the mixed tray loader,” says Rainer.
Space saving isn’t the only advantage of FANUC’s DCS safety software, which combined with safety scanners to monitor human activity around the robot, can safely allow for operators to enter the robot motion area to load or unload parts to the part tray, or to insert a layer card into trays, for example, with minimal impact on production time.
"The robot moves at normal speed when no operator is in the monitored zones. If an operator approaches the "slow down zone”, area sensors detect the intrusion and the robot slows down. If the operator enters the robot motion area or "stop zone”, the robot comes to a complete standstill,” explains Rainer.
FANUC expects the dairy category to be one of the first food industries to adopt the robotic pot swapping system, as products such as yogurt, cream and soft cheeses are usually available in several different variants, and the LR Mate200iD was engineered with this industry’s hygiene demands in mind. The robot is IP67 rated as standard, enabling it to endure frequent washdowns as part of a daily routine. An optional upgrade to IP69K is available for operations that require equipment to be able to withstand high pressure washing.
However, the system is by no means exclusively for dairy applications, with ready meals, pasta sauces, jam and salad dressings all potential application areas. In testing it was shown to be especially effective in handling plastic pots, glass jars and other rigid, flat-topped containers, since it relies on vacuum to grip and manipulate product.
The robotic pot swap system can be configured as either an offline or an online system. The system developed and installed by Pacepacker Services at the UK dip producer was an offline execution, positioned over twin lanes of filled trays. The picking heads remove one line of product from the first tray, and place it into the second tray. The process is then reversed to swap items in both trays. In an online configuration, the MTL would typically be fed by multiple product lines, with a robot picking a row from one conveyor and placing it in a tray, then picking a row from another conveyor and so on.
- Robotics competition to inspire Gen Z
- Real-world robotic innovations
- Extra reach for high speed applications
- Getting a taste for robotics
- FANUC joins industry calls for UK manufacturing strategy
- Software Options Build Up Basic Robot Profile
- Putting safety first
- Robot palletising partnership
- Plug & weld robot cell
- Long reach robot
- Balls to Gravity
- ROBOTS GIVE FASTER CELL TOOL CHANGE TIMES
- ROBOT FOR DELICATE ASSEMBLY
- FIRST FASTBOX
- NUMBER OF ROBOTS IN UK ON THE RISE
- Tailor Made For Automated Warehouses
- Number of Operators Reduced
- Prevents Potential Material Release
- Integrated or Standalone
- The future is bright - The future is automation!