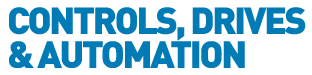
![]() |
Charlotte Stonestreet
Managing Editor |
Home> | AUTOMATION | >Controls | >Safety when the chips are down |
Home> | AUTOMATION | >Machinery Safety | >Safety when the chips are down |
Home> | MACHINE BUILDING & ENGINEERING | >Machinery Safety | >Safety when the chips are down |
Safety when the chips are down
19 October 2015
Zweifel Pomy-Chips near Zurich uses Pilz PSS 4000 automation systems to monitor and control the automation and safety functions on nine upgraded packaging lines for potato crisps.
Zweifel is in the process of modernising nine packaging lines. The company has a marked expertise when it comes to building processing equipment. As a result, it prefers to undertake planning and expansion of production equipment and plant programming itself. Zweifel put the necessary packaging and conveyor systems out to tender and the plant control system was specified.
The interconnection between individual plant sections meant that the interfaces and logic connections of the emergency stop functions had to be assessed and transferred into one overall case of compliance. So the Machinery Directive 2006/42/EC comes into play: Machinery must be constructed in such a way that man and the environment are sufficiently protected from harm. Under bilateral agreements, Switzerland has undertaken to comply with this directive. Manufacturers of machinery, and those that place it on the market, must give binding confirmation that their plant meets the minimum requirements in the form of a declaration of conformity.
Gerhard Meier, team leader of technical services at Zweifel, comments: "It was clear to us that we needed support from a competent partner. As we have enjoyed a longstanding partnership with Pilz, we were aware of its expertise in risk assessment and development of reliable safety concepts, right through to CE marking."
Safety-related control
Pilz worked with the company to produce a safety-related control concept, which involved development of mechanical, electrical and other technical engineering solutions for machinery safety. Essential elements are the application of standards and directives, the definition of safety integrity levels (SIL) or performance levels (PL) and the consideration of machine availability and productivity, including safety aspects.
Zweifel wanted a high-performance safety control system to link and monitor the exchange of safety-related signals separately and in parallel with the plant control system. Essentially the requirement was this: the device was to be highly network-capable, reliable and simple to program as well as easy to use in day-to-day operation.
Conveyors transport the baked crisps to the new packaging lines. A pneumatically controlled flap opens, allowing the crisps to access the fully automatic packaging machines; the crisps are soon bagged and on their way to market. The Pilz PNOZmulti modular configurable control system, which had been used previously, had been responsible for the plant's safety management. However, the bigger the plant and the more complex the requirements, the more efficient and economical complete, modular systems such as the PSS 4000 become. That is because this system also offers the option to combine and practically merge safety and automation.
As the central component in the new packaging line, the PSS 4000 system for safety and automation monitors all safety-related functions: the packaging line includes safety gates and an intelligent access concept. Gates have Pilz PSENmag magnetic safety switches and PSENcode coded safety switches. The latter are used to monitor the position of guards in accordance with EN 60947-5-3 and also for simple position monitoring. Pneumatic cylinders are also monitored: flaps must be locked during cleaning, otherwise there is an increased risk of injury. The emergency stop pushbuttons along the packaging line are also monitored using the PSS 4000. The company attached great importance to having four autonomous safety circuits; it must be possible to clean one section of the plant without bringing the entire plant to a standstill.
The PSS 4000 optimises interactions between hardware and software, network devices and the real-time Ethernet. As it is possible to distribute and transfer control functions consistently to the periphery, Pilz says the system enables a wide range of projects to be implemented more easily and with greater flexibility than with conventional solutions. Rather than having a centralised control system, a modular user program is made available within a centralised project. This enables standardised and therefore simple handling.
Meier concludes: "When selecting PSS 4000, the deciding factors for us were its simplicity, the drastically reduced cabling work, clear communication, clear responsibilities and the excellent price:performance ratio."
Communication between the plant control system and the Modbus TCP bus system is running smoothly. Another key factor in the decision to choose the automation system was the ability of the PAS4000 software platform and its graphics editor to link into the existing structure of the PNOZmulti Configurator. Parameter setting therefore remains transparent and simple should future changes be needed.
Key Points
- Pilz worked with Zweifel Pomy-Chips on a safety-related control concept, developing mechanical and electrical engineering solutions
- The device was to be highly network-capable, reliable and simple to program as well as easy to use in day-to-day operation
- The PSS 4000 system for safety and automation monitors all safety-related functions