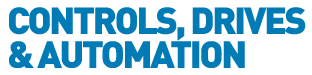
![]() |
Charlotte Stonestreet
Managing Editor |
Home> | MACHINE BUILDING & ENGINEERING | >Cables | >Cabling for robotic manufacturing |
Home> | AUTOMATION | >Robots | >Cabling for robotic manufacturing |
Cabling for robotic manufacturing
14 October 2015
Although robots have been used to assemble cars for 50 years, the pace of implementation is increasing rapidly. New production techniques are being developed by manufacturers as they strive for better productivity and profitability. Justin Leonard, director, igus reports
Auto manufacturers are no longer just replacing the human positions with robots on traditional, straight assembly lines. Manufacturing Engineers are now rethinking the production flow to obtain lower build times and gain a higher level of flexibility. Multiple car models can now be built simultaneously on the same line giving a new level of customisation.
Collaboration between robot stations is now widespread thanks to the ability to integrate different types of functions, ranging from logistical to welding, painting and machining robots. Often multiple sophisticated 6-axis robots can be seen located in these demanding environments, operating in cramped conditions and at very high speeds.
Power and signal wiring to the robot servo motors is provided by the manufacturer and is located and secured internally, while cabling to the robot’s head and grippers is externally mounted and installed during the integrating and commissioning stage of the robot cell. This external cable is normally enclosed inside a protective hose and, with a 6-axis robot, subject to a great deal of rigorous movement. This in turn can lead to premature cable failure and costly production downtime, primarily due to three main modes.
As the robotic arm rotates and moves in and out during the production cycle, the cable management hose can fall into the robot’s working area. This leads to damage to the cables, connectors or hoses. Ideally the cables are kept as short as possible, but with a 6-axis robot rotating up to 360 degrees, a significant amount of slack is needed to allow all possible rotations and positions.
Variety of cables
The wiring harnesses often consist of a variety of cables in addition to traditional current carrying copper types. Fibre optic cables, if subjected to tight bend radii, can crack; this can reduce data rates dramatically. Data bus signalling often needs shielding to protect against electromagnetic emissions that can lead to data corruption.
As robots are increasingly subjected to harsh environments, externally mounted cables and connectors are now more vulnerable. Paint mist, metal splashes from welding operations and sealing pastes can damage cable hoses and clog cable retraction devices.
Manufacturing Engineers are also very conscious of any production downtime due to preventative maintenance, upgrades or machine change-over times. The replacement of a traditional solid, corrugated hose means that copper and optical cables have to be threaded through carefully to avoid damage. Re-attaching connectors will often require special tooling and knowledge.
Plastic energy chains are one solution to the issues with corrugated hoses. As the name suggests, the energy and signal cables are enclosed in a robust, flexible "chain”, made up of plastic links. These chains come with either circular or rectangular link sections depending on the application. Circular versions are designed specifically for use on multi-axis robotic arms. Rectangular links are used primarily where simple two-dimension travel is required, for example in material handling systems or at the base of rotating robots. The use of tribopolymer parts eliminates any need for external lubrication, as they are self-lubricating.
Modular format
The modular format with the igus triflex TRE energy chain system, for example, means that cables can simply be pressed in, without the need to remove connectors. The chain still provides a smooth outer contour to avoid any "snagging” on the robot and can rotate up to +/-10 degrees per chain link.
Cable retention and retraction systems are now more sophisticated. Energy chains can now be purchased with internally fitted pre-tensioned springs for use with smaller robots. This allows a simple, slide mechanism to retract the cable quickly to avoid entanglement with the robot arm. These systems are capable of retracting up to 500mm of cable, yet have a low loading on the robot arm. Response times are extremely fast and can handle the high 800mm/s2 acceleration speeds required, for example, in painting applications. Important too, is that these systems have space-saving designs for confined applications, yet still have less deflection points to avoid stressing fibre optic cables.
New product announcements by robot manufacturers show no signs of slowing down. Although this is great news for the industry, in turn however this may lead to new challenges for the Production Engineers as new applications and installation methods are developed. Fortunately, innovative designers of energy chain systems are also investing in new materials and solutions to ensure these demands are met.
Key Points
- Cabling to a robot’s head and grippers is externally mounted and installed during the integrating and commissioning stage of the robot cell
- Ideally the cables are kept as short as possible, but with a 6-axis robot rotating up to 360 degrees, a significant amount of slack is needed
- With plastic energy chains, the energy and signal cables are enclosed in a robust, flexible 'chain', made up of plastic links.
- Lubrication-free bearings for heavy industry
- The rise & rise of linear robots
- Maintenance free
- manus award 2023 open for entries
- Linear robots for cost-effective automation
- Igus®' Lubrication - and Maintenance-Free Products and Systems Reduce Costs and Improve Technology in Automation
- World's first driven e-chain system
- Wood plastic composite bearing
- Rise in demand drives price down for 3D printed plastic parts
- SolarBuggy with chainflex cables
- Balls to Gravity
- ROBOTS GIVE FASTER CELL TOOL CHANGE TIMES
- ROBOT FOR DELICATE ASSEMBLY
- NUMBER OF ROBOTS IN UK ON THE RISE
- High-Speed Data Transmission
- Cable Glands For Hazardous Areas
- Cable Testing & Manufacture Expertise
- The future is bright - The future is automation!
- High Demand For Grant
- More Capacity, Less Space