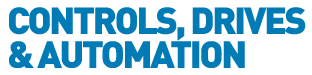
![]() |
Charlotte Stonestreet
Managing Editor |
Batching control system
03 December 2015
Dyer of natural and synthetic fibres DP Dyers recently turned to distributor of pneumatic products and process systems, Thorite, to carry out modernisation of its dye batching system, which offered poor production flexibility, had unreliable back-up functions and no facility for data transfer.
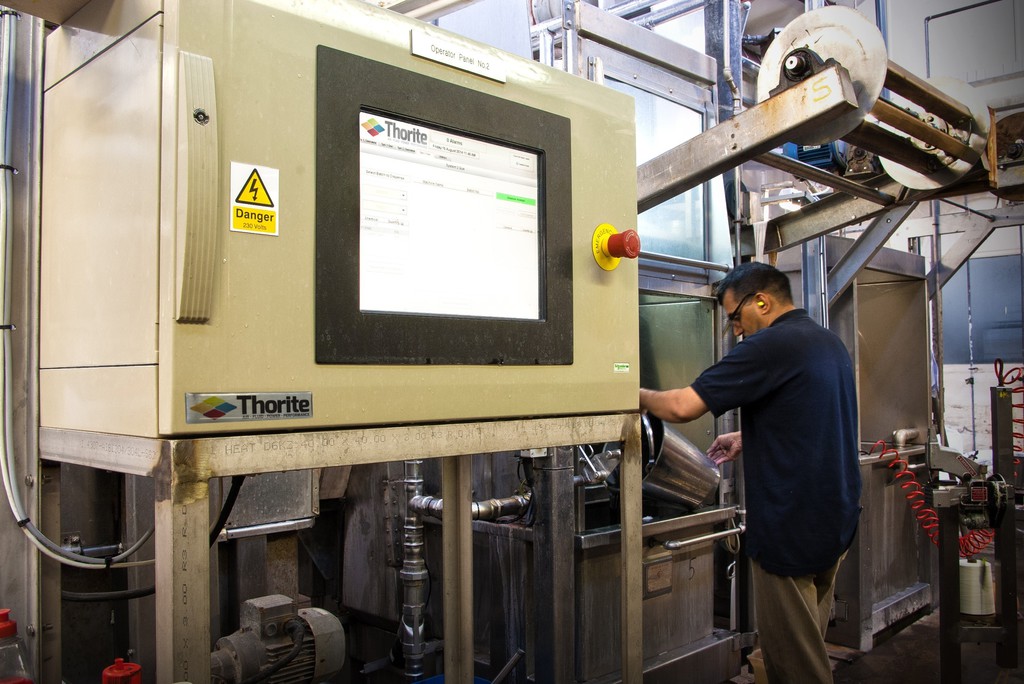
Thorite designed and installed a new dye batching control system using barcode technology to measure and batch fabric dye recipes and ingredients. Each dye recipe comprises of a list of dry and liquid ingredients which are mixed in the dyeing machine prior to the fabric dyeing process.
Dry dye powders are manually weighed in the powder room and the relevant bar codes are entered into the system using the barcode reader, to record the recipe progress and for inventory control. Transfer of the dry ingredients to the dye machine is done by hand.
Liquid ingredients are stored in barrels for safety in a chemical bund area. These include acids, alkalis, bleach, dispersing agents, stabilisers and auxiliaries such as softeners and conditioners. When the recipe barcode is entered via the bar code reader the system automatically measures and batches the correct chemical volumes to fulfil the recipe using specialist flow metres.
Finally, soft Pennine mains water is supplied through the chemical bund pipework and the system stops the supply when the liquid ingredients of the recipe are complete and the dyeing process can commence.
The new control system and associated software enables all the existing dye machines to be retained, but ensures totally accurate dye colours to be reproduced whenever required. The DP Dyers installation also included a new full specification server in the Main Office control room plus 2 PCs fully programmed with Ignition SCADA software.
This is supported by a 19" panel- mounted PC in the Powder Weighing Room with barcode data entry with associated SCADA touchscreen, two operator panels, a pneumatic process manifold operating 20 process valves, 24 barrel level monitoring system and 2 flow meters and electronics in the production hall.
- ELECTRIC DRIVES & VACUUM TECHNOLOGY COMBINATION
- Pneumatically actuated architecture
- No Need For Circuit Breakers
- Raising awareness of unseen energy inefficiencies
- Mechatronics & hydraulics courses
- Energy efficient equipment
- Changing times at Thorite
- Compressor update savings
- Capital equipment & aftermarket solutions
- Thorite seals partnership to supply GWE Eco-Max voltage optimisers
- Reduce Fault Times
- Vision Control Makes The Cut
- MULTIPLE PROTOCOL CONVERSION
- MAKE SURE YOU CATCH THE RIGHT BUS
- Smarter, Faster & More Compact Robot Controller
- What Does Windows 8 Mean For Test & Measurement?
- Thyristor Stack Controllers
- Easy To Automate
- Understanding Thyristor Control
- Introduction to embedded control and monitoring webcast