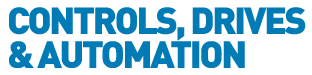
![]() |
Charlotte Stonestreet
Managing Editor |
Solving the productivity puzzle
13 February 2017
Although the UK economy might be expanding overall, levels of productivity remain worrying low. CDA editor, Charlotte Stonestreet, looks as the issue, some of the reasons behind it and explores whether Industry 4.0 could have a role to play in providing a solution
While the UK government’s 2016 Autumn statement has highlighted issues surrounding the country’s low levels of productivity, sadly this is not a new problem for the British economy. Indeed, 19 years ago in his pre-budget report, then Chancellor Gordon Brown stated: “The first challenge is to increase our productivity. Britain today is some 20% less productive than our main competitors and has been for years.”
Last November it was current Chancellor Phillip Hammond, addressing the issue. “The productivity gap is well known, but shocking nonetheless,” he said. “It takes a German worker four days to produce what we make in five, which means, in turn, that too many British workers work longer hours for lower pay than their counterparts.”
The statistics are stark. Addressing an audience at the Advanced Engineering 2016 event, David Bailey chief executive of north west aerospace alliance highlighted the fact that since the financial crash in 2008, productivity in the UK has pretty much flatlined and drew attention in particular to the differences in productivity between the UK and other developed economies.
“In the last quarter of 2015, the UK economy expanded by 0.5%, but the total hours worked increased by 1%, so that means our productivity fell,” said Bailey. “We are now 18% behind where we were predicted to be pre the financial crisis.
“And every year since 2010 the Government has forecast that we are going to get back to that curve, that the UK is going to go back to the productivity that we have achieved previously. But actually that has not happened and we have continued to grow very slowly since 2008.”
And although there have been times when UK productivity growth has reached 5% and moved towards the levels achieved by other major economies - for example the 1990s and early noughties saw intermittent periods of strong growth - the reality is that productivity in the UK has never really recovered from the financial crash. Indeed, If the economy had maintained its 1997-2007 course, an hour's work would be worth 17.9% more than it is today.
A British phenomenon
What makes this all the more worrying is that it does seem to be a particularly British phenomenon. “If we were as productive as the average of the other G7 countries - Canada, France, Germany, Italy, Japan and the US – we could all take every Friday off,” said Bailey. “And actually, if we were as productive as the US, we could also take Monday morning off as well.”
Of course, comparing one country’s productivity to another’s is not without issues, particularly as the value of goods and services fluctuates with currency values. Also, there can be variations in the way different national statistics authorities measure labour and capital contributing to a unit of production (the commonly used measure of productivity is the rate of output per unit of input). But whichever way you consider it, things have not been great for the UK in terms of productivity.
While there are many underlying factors influencing the productivity gap in the UK – a conundrum often referred to as the ‘productivity puzzle’ in the UK media – many economists have identified a comparative lack of investment in the latest technology and research and development as a major contributor. For example in Germany there are 1034 R&D staff for every 100,000 people; in the UK there are 883. Bailey points to the fact that Germany has invested 10 times what the UK has in robotics and automation, and Italy four times. He also asserts that seemingly small increases result in some very large numbers, for example a 0.1% increase in productivity each year equates to £35b.
The UK Government is, however, making steps to address the productivity gap in the form of the recently announced National Productivity Investment Fund, which is to be funded though additional borrowing. Amongst the £23 billion spending plan some £2 billion has been earmarked for technology and science research and development, which can only be a good thing.
According to Lee Hopley, Chief Economist at the EEF, “A company looking to increase productivity will be looking to extract evermore value from their output for every unit input to their business. So that’s really important for business because if a company is doing that systematically and successfully, it’s going to be more competitive and that means it’s going to have more success in boosting sales both at home and overseas markets and it’s going to bring bottomline benefits as well in terms of improved profitability.”
No magic bullet
As Hopley asserts, there is no magic bullet for improving productivity, however part of the solution most definitely lies in investing in new ideas, innovation, technology and modern machinery, and people. “If improving productivity is all about increasing value and improving efficiency, key ways to do that are by investing in technology, innovation and modern machinery. And the sectors that are more likely to do that, and therefore have an edge when it comes to improving productivity, are sectors in industry and manufacturing.”
Indeed, an EEF report from spring 2016 indicates that UK manufacturing’s growth has outperformed services and the economy as a whole, suggesting that manufacturing may not be the source of the UK’s productivity problem, but that’s not to say that manufacturers aren’t concerned about falling behind competitors. There are also vast variations in productivity between different sectors within manufacturing. For example, the UK pharmaceutical, automative and aerospace sectors are as good, if not better than their global counterparts when it comes to productivity.
And while investment is a good place to start, on its own it won’t necessarily reap the productivity rewards needed. “Machines alone won’t give you the productivity, the edge,” said Hopely. “You’ve got to have the new ideas, the new products, new processes and also new services that can give you increased sales in new markets. And complementing that, underpinning that is the skills of the workforce, so having great technical skills and great management and leadership skills are the things that really pull all these investments together.”
One way businesses can increase productivity is by employing technologies associated with the much touted Industry 4.0. Whether you see I4.0 as a revolution, or simply an evolution, there is little doubt that adopting elements of it can have a beneficial effect.
Predictive maintenance
According to research from the European Parliament, by using advanced analytics in predictive maintenance programmes, manufacturing companies can avoid machine failures on the factory floor and cut downtime by an estimated 50% and increase production by 20%. Some companies will be able to set up 'lights out' factories where automated robots continue production without light or heat after staff has gone home. Human workers can be used more effectively, for those tasks for which they are really essential.
Data gathering and analysis associated with Industry 4.0 can be an incredibly valuable tool in increasing productivity. For example, global management consults McKinsey & Company refers to an oil-exploration company which collected more than 30,000 pieces of data from each of its drilling rigs—yet 99 percent of that data was lost due to problems of data transmission, storage, and architecture. The tiny trickle of data it did capture was incredibly useful for managers. But so much more can be done. The executives we surveyed said that correcting these data inefficiencies should improve productivity by about 25 percent.
Analysis carried out by The Boston Consulting Group indicates that in Germany Industry 4.0 will be embraced by more companies, boosting productivity across all German manufacturing sectors by €90 billion to €150 billion. Productivity improvements on conversion costs, which exclude the cost of materials, will range from 15 to 25 percent. When the materials costs are factored in, productivity gains of 5 to 8 percent will be achieved.
- Partnership to accelerate development of AI solutions for future mobility
- Ford teams up with Agility Robotics for final delivery step
- Why your business needs thermal condition based monitoring
- Overcoming counterfeits
- Research project for the use of hydrogen in aviation
- Inteq becomes new name for Invar Group
- Ruggedisation and miniaturisation converge in connectors
- It's all about data
- Simulation used in humanoid robot development
- Energy sector becomes UK's top target for cyberattacks
- Robotics & Automation 2013
- Automation on the upswing
- Amendment to Commission Regulation (EC) No 640/2009
- Confidence returning to UK manufacturing technologies
- A national success story
- Automation: plan to succeed
- EPTDA expands in the Middle East & Africa
- Innovating for the recovery, innovating for the future
- A system-oriented approach to assessing energy efficiency
- tGARD IN ACTION