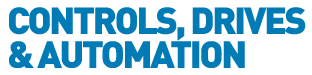
![]() |
Charlotte Stonestreet
Managing Editor |
Industrial robots access AI via the cloud
17 April 2018
Mitsubishi Electric has developed a cloud-based solution for pro-active maintenance based on the AI platform within IBM Watson, which enables the smart analysis of operational data to predict and highlight future maintenance requirements.
The theory is that sometimes service schedule requirements for robots are inadvertently missed which, despite the extended duty-cycles and the general reliability of modern robots, is not a healthy situation for continuous plant operation. By using an innovative predictive maintenance method however, users are engaged with their robots, receive operational and maintenance data and thereby keep them healthy via planned maintenance schedules, reducing operational costs, increasing asset productivity and improving process efficiency.
Today many companies are still caught by surprise when machine failures occur. They tend to fix problems during enforced downtime, or implement preventative maintenance based on set schedules or numbers of operational hours. However, using predictive maintenance techniques production problems can be highlighted long before they result in unplanned downtime or impact on yield. Maintenance personnel can take corrective action before failure or before degraded machine performance results in sub-standard products being manufactured.
The additional benefit of predictive maintenance is that by potentially avoiding some fixed-schedule maintenance tasks you don’t service equipment when it isn’t required, rather on-demand, therefore saving time and expenditure.
This latest solution from Mitsubishi Electric offering predictive maintenance for robots utilises the AI platform within IBM Watson to assess actual maintenance requirements and then suggest actions to take in an efficient and timely manner. The platform uses predictive maintenance models, digital simulation and extrapolation of trends to provide maintenance information based on actual usage and wear characteristics. This is particularly pertinent to robots, where users don’t always appreciate that periodic maintenance is a mandatory requirement.
There are a number of moving parts within SCARA and articulated arm robots, depending on the type and model they include servo motors, gears, ball-screws, belts, bearings and seals. Items will experience wear over time and require eventual replacement while others will need fresh lubrication and a service check on belt tensions etc. Considerations such as duty cycles, operating environment and loading can all play a part in dictating service requirements, so being able to visualise components with a live status and then receive considered advice tailored to that particular machine will match servicing closely to requirement.
Voice command
The system also demonstrates how the speed and efficiency of any necessary maintenance activities taking place can be enhanced using voice commands. An augmented reality platform is used to create a visual overlay which provides live information in real-time interactive screen graphics. Siri for example can then be used to issue simple commands based on the knowledge gleaned from the screen. Increased visibility of live status information is expected to provide opportunities for significant reductions in downtime.
Using augmented reality, system maintenance activities can also be optimised through the use of smart glasses, where the operator receives guidance on what tasks need to be performed. The glasses can show CAD drawings of the various robot parts, superimposed over the robot itself. The glasses can also show the maintenance manual and individual instructions.
This type of next generation human / machine interaction works well with the latest safety solutions that can do-away with the traditional interlocked cage in many instances, relying on smart proximity sensors and Mitsubishi Electric’s MELFA SafePlus feature to manage robot movement safely in the presence of humans.
IBM Watson
Watson is a question answering computer AI capable of answering qy=uestions posed in natural language, named after IBM's first CEO, industiralist Thomas J. Watson.
Initially developed to answer questions and compete in the US quiz show Jeopardy!, which it won in 2011, it has since been rolled out as a commercial on-demand interface that various applications an access online.
Watson on IBM Cloud has evolved machine learning capabilities and optimised hardware available to developers and researchers.
Key Points
- Using predictive maintenance techniques production problems can be highlighted long before they result in unplanned downtime
- Mitsubishi Electric's solution for robots utilises the AI platform within IBM Watson to assess maintenance requirements and suggest actions
- Using augmented reality, system maintenance activities can also be optimised through the use of smart glasses
- Mitsubishi Electric & Radiflow cooperation enhances industrial cyber security
- Partnership secures substation refurbishment contract
- Backup & Restore
- Energy from waste technologies
- The immediate future of automation in the food industry
- 30 YEARS OF VSDS
- Robots help drive quality control in high-speed inhaler testing line
- Control Freaks joins Mitsubishi Electric’s Drive Solutions Centre network
- Leveraging the power of data
- Robot boom to continue says Mitsubishi Electric
- No related articles listed