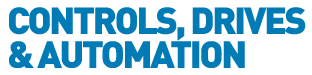
![]() |
Charlotte Stonestreet
Managing Editor |
Home> | AUTOMATION | >Systems | >When is the right time to automate? |
Editor's Pick
When is the right time to automate?
17 March 2025
WITH RISING operational costs and an increasingly competitive landscape, businesses across the manufacturing and industrial sectors are increasingly turning their focus to automation to drive efficiency, asserts Phil Coleman.

With the National Insurance rate and National Minimum/Living Wage increases looming, adding an extra financial burden to employers, companies are seeking smarter ways to optimise their processes. But when is the right time to automate your systems and facilities? And how can businesses overcome the challenges of stepping into automation? According to Phil Coleman, business development manager at adi Lean Manufacturing, the timing and approach to automation are crucial.
He said: "We’re seeing a renewed focus on efficiency, especially in the first two quarters of this year.
“With recruitment at its lowest levels in years, many companies are looking inward, trying to streamline processes rather than add headcount – and automation is the right answer for many."
Why automation looks different for every business
“Automation isn’t a one-size-fits-all solution,” explained Coleman. “Businesses often fall into one of three categories when considering automation. There are the early adopters, companies already using automation and ready to expand their capabilities. For them, it's often a case of upgrading existing systems or integrating new technologies. These companies are, or are on their way to becoming, completely future proof. But not everyone is that far ahead just yet.
“Then there are the cautious first-timers, companies that recognise the need for automation but require extensive guidance. They need a partner to hold their hand through the process, ensuring they understand every step from planning to implementation. For these businesses, now’s the time to consider automation, but of course, knowing where to start is crucial, which is where having the right partner becomes vital.
“Finally, there are companies that have tried automation in the past – often five or six years ago – only to be left with failed systems, unfulfilled promises and costly mistakes. It’s easy for these businesses to remember the pain and be hesitant to try again. Even if technology has dramatically advanced since then, the scars from over-promised, under-delivered projects linger.
“Rebuilding their trust is imperative because, ultimately, refusing to automate will only become more damaging in the long term.”
It’s instrumental that a bespoke approach is implemented – every facility is different, depending on the industry, the size of the business and a range of other factors.
He added: “Sometimes, full automation is not always the answer, and a semi-automated or halfway house approach is a good step. While being cautious and tailoring your approach is important, taking the right steps towards automation will be necessary, now more than ever – and being able to prove it with the right data and evidence to show the impact can be particularly helpful.”
What are the main challenges?
“Automation failures often stem from a few critical issues,“ said Coleman. “Over-promising and under-delivering is a major one. Some providers promise unrealistic timelines or capabilities just to win contracts, leaving businesses stranded when the technology doesn’t work as advertised.
“Another issue is the lack of upskilling – or reskilling. Companies may wrongly assume automation will simply slot into their existing processes. However, new technologies often require maintenance teams to upskill to manage and service the new equipment.”
It’s vital to identify how certain job roles might change and provide training on new technologies, and involving employees in the automation process is a key piece of the puzzle.
“Going from a manual assembly process to a semi-automated assembly process reduces the training time for new operators, allowing them to be productive in a dramatically reduced time period.
“However, poor planning and communication also play a role. Without clear, honest communication from the start, projects can derail. It’s about being optimistic but brutally honest. Telling a business an automation project will take 20 weeks when it’s a 40-week job helps no one."
So, when should businesses take the leap into automation?
“The answer lies in aligning automation with strategic goals,” Coleman explained. “Companies should consider automation when recruitment is challenging and operational efficiency becomes the priority, when processes show signs of bottlenecks or manual errors, when competitors are innovating and staying stagnant risks falling behind, and when there’s a clear understanding that automation is an investment — not just a quick fix.”
The key to successful automation lies not only in the technology but also in how it's utilised. "Automation isn’t about removing human talent — it’s about enhancing it by taking over repetitive tasks and allowing skilled workers to focus on innovation and problem-solving,” he added.
For businesses considering automation, now is the time to start the conversation. With operational costs rising and recruitment slowing, embracing smart, well-planned automation can be the competitive edge that sets a company apart.
Phil Coleman is business development manager at adi Lean Manufacturing
- No related articles listed
- SWISSLOG SECURES MAJOR ORDER
- IMPROVED PERFORMANCE & RELIABILITY
- Engine Facility
- BULK AUTOMATION
- Integrated Packaging Solutions
- INTEGRATING ELECTRIC AND PNEUMATIC CONTROLS
- Rockwell Automation expands Midrange system portfolio
- Yokogawa joins Friends of the Supergrid
- Festo extends reach of VTUG and MPA-L valve terminals
- Siemens extends TIA Portal engineering framework