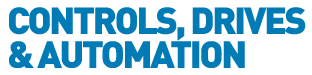
![]() |
Charlotte Stonestreet
Managing Editor |
Home> | DRIVES & MOTORS | >Testing | >Behind the curtain at ABB’s one-stop shop for drive servicing |
Home> | DRIVES & MOTORS | >Variable Speed Motors | >Behind the curtain at ABB’s one-stop shop for drive servicing |
Editor's Pick
Behind the curtain at ABB’s one-stop shop for drive servicing
11 August 2023
Ahead of its grand opening in September Neil Rayns took CDA on a tour of the company’s upgraded drive service workshop in Coalville, Leicestershire

THE FIRST thing you notice about ABB’s drives service facility in Coalville is just how clean and tidy everything is. Not at all how you’d picture a workshop. Neil Rayns, the manager of the facility, evidently runs a pretty tight ship.
“Along with heat, dirt is a drive’s number one enemy,” explains Rayns. “To return a drive to its factory condition, we need an environment that allows us to work efficiently without junk getting in the way. And on a practical level, we can’t have dirt and dust floating about the place and getting on circuit boards”.
Where previously a UK drive in need of comprehensive servicing would be sent back to ABB’s factory in Helsinki, the ABB workshop at Coalville now allows a wide range of maintenance activities to be carried out without the drive having to leave the country. Amid global logistics challenges, this means that repairs can be turned around much faster. It also significantly reduces the environmental impact of repairs carried out by dramatically reducing the amount of transportation required, and the carbon emissions incurred as a result.
Factory quality
The centre is accredited to factory standard, which in layman’s terms means that repairs carried out here are done to the same level of quality that you would get direct from the factory. Drives are returned to the customer essentially as new, with Rayns keen to emphasise the sustainability credentials of a reconditioned drive compared to a replacement.
“Having a Reconditioning or Premium Repair service here in Coalville uses between 55 and 80% less carbon compared to buying a brand new one," he says. "A new drive requires rare earth materials, plastic for the casing and PCBs, and a whole host of other components and electronics that have to come from somewhere, and will therefore have a carbon footprint. You also have to think about how best to dispose of the old drive. With a drive reconditioned here, you get the same performance, at a fraction of the cost of a new drive, while also helping to extend the lifetime of your asset.”
The facility is equipped to carry out several different types of service, but nearly all start off with Inspection and Diagnostics. Here advanced diagnostics tools are used to analyse the drive’s condition at a component level, the environmental impacts from running the drive, and the likely causes of any failure. A report is then produced showing the tests carried out, their results, and any recommended actions – not dissimilar to a car MOT. The report will then be sent back to the customer to help determine the next steps and decide what repairs are subsequently carried out.
Depending on the drive’s condition, there are several options available. For non-functioning drives, there is either Standard Repair or Premium Repair. Standard Repair is used when a major fault needs to be corrected. It includes visual inspection, thorough cleaning, fault finding analysis, replacement of any failed or failing parts, functional full-load test, and service report. Replaced components come with a one-year warranty.
Premium Repair includes everything in the Standard Repair package, along with preventive maintenance, and replacement of any ageing components, as opposed to only those which have failed. The drive or module fault is analysed, and a failure report is supplied. All components in the preventive maintenance schedule are replaced, as well as any components that could potentially suffer from ageing due to the specific loading or environmental conditions in which the drive is typically operated. The drive or module is essentially restored to the same condition as it was in when it first left the factory, with a two-year warranty.
For drives which are still functioning but simply require a bit of TLC, there is either Preventive Maintenance or a Reconditioning service. Preventive Maintenance is carried out based on a drive’s planned maintenance schedule.
“It’s much like changing the oil in your car every 10,000 miles,” says Rayns. “It’s always better to do this before it risks failing, because if it goes suddenly then you might find yourself in a world of trouble. Think of it as an investment in avoiding failures and eliminating production disruption."
In Preventive Maintenance the drive will be stripped back and thoroughly inspected, and any components replaced either according to the device’s maintenance schedule, or if they show signs of premature wear. As well as preventing the likelihood of unplanned downtime from unexpected drive failures, the Preventive Maintenance service can also help to reduce performance drift over time.
The Reconditioning service is intended for when major components such as IGBTs need replacing due to their ageing, condition or loading profile. Reconditioning includes a full inspection, thorough cleaning, and individual component analysis and replacement, with the drive or module restored to the same condition as it left the factory. Reconditioning also comes with a two year warranty not just on components replaced, but on the whole drive.
Fully load tested
All drives, irrespective of the level of service, are fully load tested before being returned to the customer – something Rayns is particularly excited about.
“Full load testing is something we weren’t previously able to do," he says. "We recently installed a testing rig which means we can test drives under representative conditions. So if you had a drive which was being used for instance on a big grinder at a quarry, previously we were able to test it functionally, but we weren’t able to throw everything at it and fully recreate the conditions it would actually be operating under. Now we can test them until they run hot and really push them to the limit, or throttle the air inlet back to simulate blocked filters. This gives the customer confidence that the drive will perform once it’s back in situ."
A dedicated washing facility is used to clean drives inside and out. This takes place in three stages, starting with a jet wash to remove dirt and grime from modules and casing. The second stage involves using ultra-high frequency vibrations to clean circuit boards and other internal components before the drives finally reach a drying room where the temperature is kept raised to remove all moisture.
For drives which have reached the end of their useful life, either suddenly or expectedly, the workshop is also ramping up its Drive Exchange and Recycling services. The Drive Exchange service provides a solution for sudden failures, and is the fastest way to get a process back up and running. The workshop maintains a fleet of reconditioned drives which can be sent out as an immediate like-for-like replacement for the failed drive. Drives at the end of their life can also be recycled for a small fee, reducing the environmental impact of the device once it reaches retirement.
The workshop is accredited to carry out repairs to a factory-level standard. In practice this means that Rayns and his team have access to advanced diagnostic tools, processes and documentation that are only available to a handful of ABB facilities around the world. Each model of ABB drive has its own suitcase, containing all the spare parts a technician could possibly need to service a particular drive model. Counterfeit spare parts are a growing problem in the drives market, and only genuine ABB components, direct from the manufacturer, are used.
Hands-on training
Aside from the repair facilities, the workshop building also houses classrooms and a demonstration facility for hands-on training for staff or customers. Certification for the factory has been a long time in the making, but Rayns is delighted with the upgrades that have been made.
“It certainly adds some prestige for the UK. It shows that ABB is serious about investing in the talent and facilities here, and also that they believe in what we’re doing. When I started here several years ago there was no workshop to speak of, and we had to start everything from scratch, so I’m delighted to see this journey come to fruition," says Rayns.
“From a drive end user’s point of view it’s all about building resilience, and looking after your assets,” he concludes. “Everything we do here is geared towards safeguarding your investment and minimising the chance of unplanned downtime. At the end of the day, a drive is just a tool used to keep a customer’s processes running. But without it, the costs can quickly add up for every moment that that drive is not in operation. Not only can we now get our customers back on track faster than ever before, but we’re also helping to extend the lifetime of their assets, while improving the sustainability of their investment.”
Neil Rayns is drives workshop manager at ABB
For more information about the services offered at ABB’s drives workshop in Coalville, or to make a service enquiry, visit:
Key Points
- ABB's drives service facility enables maintenance activities to be carried out without drives leaving the country
- Repairs carried out at the facility are done to the same level of quality that you would get direct from the factory
- All drives, irrespective of the level of service, are fully load tested before being returned to the customer
- HIGH FLYING AUTOMATION
- First fully robotic liver transplant
- Robots-as-a-service for manufacturing industry
- All-new mobile browser with complete data encryption
- Automate to remain competitive
- VW tests 5G for production
- New technology lets humans & autonomous robots understand each other
- Ruggedisation and miniaturisation converge in connectors
- Digital innovation supporting new business models
- Mobile-grade solution for higher voltage applications