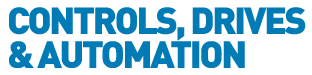
![]() |
Charlotte Stonestreet
Managing Editor |
Home> | IIot & Smart Technology | >Big Data | >The devil's in the data detail |
Home> | IIot & Smart Technology | >Industry 4.0 | >The devil's in the data detail |
The devil's in the data detail
23 June 2022
Industry 4.0 adoption isn’t just about the sexy tech, says Alastair Crawford. Rather, the data that new tech produces rules the roost – and not only the collection of the right data, but its transfer to where we can do something useful, tangible and game changing with it
UK MANUFACTURING SMEs are missing a trick by not linking their critical success factors to the shop floor for gathering all-important real time data relating to productivity, quality and safety.
With so few companies using shop floor intelligence there are significant gains to be made – because the process involves all functions in a business – plus it’s a starter concept that teams are able to get their heads around quite easily.
Shop floor intelligence involves collecting real time, accurate and critical data – like progress tracking of jobs, quality of products, productivity of machines and everything in between– so that it can be processed and analysed to optimise performance and efficiencies.
The majority of our companies adopting asmarter Industry 4.0 approachend up with this as one of their main priorities. In today’s dynamic, fast changing environment, the ability for people or systems to have the right information at the right time is critical to success. People resonate with this dimension and are often frustrated by the lack of timely data preventing them from doing their job.
Industry 4.0 data maturity
They can see how it will impact their role, which is exactly the kind of insight we need people to get to grips with if they are to embark on the journey to Industry 4.0 maturity.
For example, do you know where that critical customer job is right now on your shop floor? Do you know the Overall Equipment Effectiveness (OEE) for your bottleneck machine? Can you see whether the product of your make-or-break process is to spec? If your differentiator is ‘always deliver on time’, then you’re going to need visibility of it within your jobs.
Likewise, engineering leaders are after performance and predictive data, supply chain practitioners are all about certainty and productivity planning, while HR needs to be able to track trends around absenteeism and resource. Sensors might be needed on machines and equipment where data isn’t being collected, especially if you’re looking to measure all-important lead times, downtime and yield, but quite often, the data is already available.
After all, digital transformation is about informed, accurate and consistent decisions being made, before things go wrong – and when building a client’s high-level Industry 4.0 roadmap, we encourage them to engage in a simple yet revealing critical dataexercise.
This involves mapping the process and the data set they should be evaluating – to ensure they have the best possible visibility of those parameters to make informed decisions that will improve their performance.The data gathered helps evaluate current shopfloor KPI maturity and also understanding of any gaps that exist and where they need to be closed.
Data into insights
Manufacturers globally are looking to automate the decision-making processes on the back of information they are obtaining and analysing continually. However, what we’re seeing is a failure to turn the data they’ve currently got into easily digestible insights for their teams to make better decisions faster. The ultimate goal may be to automate decision making, but the first step is to empower teams with the data you currently have.
This is where it’s important to highlight that Industry 4.0 and Lean Manufacturing (and Continuous Improvement, Six Sigma, DMAIC etc.) aren’t different things but part of the same continuum. Where lean looks to measure in order to improve, Industry 4.0 technologies enable companies to measure what they are doing and make decisions about how to improve much quicker, cheaper and easier than ever before.
Shop floor visual management provides the necessary people with up to date information on job progress, job lists, on-going issues and actions, but Industry 4.0 technology aims to deliver the same outcomes with much less latency and reduced administration.
Quality information live
Take quality monitoring for example. Previously, QA team members would manually check parameters; record faults; update spreadsheets and visual management boards, but digital technology can now track quality information live (on vision systems, check weighers, dimensional analysis sensors) and significantly reduce the QA inspection time.
If we then extract this information and transfer it to a suitable database/enterprise system - whereby we can show fault trends over time and display this live to operators and QA staff on the floor - then their time can be better spent problem solving, identifying root causes and resolving them with almost instant feedback.
It’s not just the act of measuring that will improve performance but the associated actions we take as a team to identify causes and resolve them. Greater value can be delivered to the business by the improved quality and speed of the problem solving/feedback loop than simply through the automation of the quality processes themselves.
The next evolution of this is to automate parts of the decision making itself through direct feedback of measurement technology to the machines and processes that influence the parameters they are evaluating. An example here could be a check weighing machine feeding back live information to the packaging machines to constantly adjust and optimise their operating parameters to reduce giveaway and rejects simultaneously.
Automate data collection
When taking this next step, it’s often a requirement to automate the data collection and deliver the insight to teams in order to build confidence in the data being acquired. This helps establish the relationships between the data and the relevant process changes that will deliver the desired outcome.
In terms of change management and cost it often makes sense to stagger the journey, reaching the insights step first before trying to automate any process response. This tends to gain greater buy in from operators and team leaders - so when the second step of process adaptation is automated, we don’t get situations where people are ‘overriding’ the system and circumventing the very solution you have just invested in.
To summarise, identifying what data you should be gathering on your shop floor also brings understanding of any gaps you may have. But knowing what to do with that data once we have it is crucial too. Keeping it locked away will limit the investment value that technology can add to your business, whilst hamstringing the development of team members who could be using live data to optimise the process continually.
Alastair Crawford is MD of LMAC Consulting
- Flame and thermal barrier passes UL 2596 torch and grit test
- Robotics for the nuclear industry
- Physical AI framework enables rapid learning of complex skills in robotics
- Vision of the future
- Can robotics solve supply chain headaches?
- Metso acquires Tedd Engineering
- THE NEWS FROM CATALONIA
- Automation of entire 3D printing production process
- In the frame
- Leading names confirmed for conference
- Industry 4.0 ready
- Intelligent interlocks
- The digital future has begun
- The smart future of manufacturing
- Partnership integrates freight & warehouse management
- Secure data handling
- When & where will Industry 4.0 actually happen?
- Education key to unlocking I4.0
- Trelleborg joins Smart Data Innovation Lab
- How well is your smart farm running?