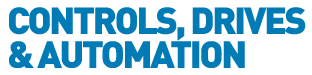
![]() |
Charlotte Stonestreet
Managing Editor |
Home> | AUTOMATION | >Condition Monitoring | >Advanced solutions simplify condition monitoring |
Advanced solutions simplify condition monitoring
21 May 2024
Liz Hill looks at how data-driven reliability improvements can streamline maintenance and cut costs

THE HEALTH of equipment, machines and devices is critical to the operational performance and profitability of modern manufacturing facilities. Organisations want to eliminate unexpected downtime caused by machinery failures and ultimately deploy `always available’ production equipment that optimises plant productivity. Manufacturers also want to prevent underperforming machines impacting product quality that is only identified during the later stages of production. The availability of real-time information and actionable insights empowers predictive maintenance strategies that lead to reduced downtime and helps prevent quality issues. To move towards this outcome, companies are digitally transforming their operations to enable greater access and visibility to much more machinery health data.
A good example of this is the monitoring of the health of valves used to control compressed air in pneumatic systems. Previously, these types of devices would generally have been run to failure, creating the possibility of machinery downtime and interruptions to production. However, diagnostic functionality provided by advanced fieldbus valve system technology now enables valve performance to be continuously monitored, so that developing problems can be identified earlier. If the system detects that the travel time of a valve is increasing, this may indicate valve wear. Early identification of issues supports predictive maintenance strategies, preventing failure during a production cycle and leads to lower maintenance costs, reduced downtime and increased productivity.
Enhanced vibration analysis
Vibration monitoring and analysis is fundamental to online condition monitoring, which has been applied to critical rotating machinery, such as compressors and turbines, for many years. In the past, significant vibration analysis expertise would have been required to understand the data and identify issues and root causes that can guide maintenance before significant damage was incurred. Modern software solutions now analyse data, alert maintenance teams to issues, outline causes and even suggest necessary repairs. The latest asset management software provides a single location where all the various condition monitoring data comes together to identify `troublemakers’ quickly and efficiently. The software collates data from a wide range of monitoring technologies and then predictive maintenance techniques and analysis tools provide accurate assessment of the health of each machine.
Despite the obvious benefits, cost and resource restraints can restrict progress of new condition monitoring programmes, but advanced automation solutions are helping. The availability of wireless technology, less expensive sensors and advanced software that reduces the complexity, have all contributed to manufacturers deploying condition monitoring technology on a much broader range of equipment. Implementing condition monitoring solutions has been made far easier. For example, wireless vibration monitors simplify the installation of automated condition monitoring. The existing wiring infrastructure would previously have been a major consideration and if it was unavailable, potentially a cost prohibiting barrier. The latest wireless devices can be installed directly on the equipment being monitored. Vibration and other useful data, such as temperature, can be transmitted over a wireless network to an asset management system, where prescriptive analytics capture the data and provide accurate diagnostics directly to maintenance teams.
Edge analytics devices also help to reduce the installation expense and deliver the benefits of continuous monitoring to more plant assets. These devices can be mounted out in the field or directly on the plant floor close to pumps, motors and fans, reducing the wiring complexity and cost. Edge computing technology helps to provide greater visualisation at factory floor level, with real-time condition monitoring data collected from the various parts of the production process analysed and presented to the operator on an industrial display right at the machine. This enables them to make informed decisions at the machine that directly impact production efficiency. Conversely, built in web service software interfaces means access to asset health is simple via any browser-enabled device. Cloud-based infrastructure simplifies the sharing of information and provides the opportunity for wider collaboration.
The pandemic saw a behavioural shift, with the acceptance of remote analysis, diagnosis and collaborative environments in which to resolve issues. Modern solutions leverage that shift to democratise data, taking condition monitoring data from equipment in the field or on the plant floor and moving it into the cloud to allow various stakeholders to view the information and make informed decisions about maintenance and operations.
Ensuring health of automation devices
It is not just machines and rotating devices that need to be carefully monitored. Process automation assets such as measurement and analytical instrumentation and digital valve controllers are all essential to the smooth operation of a plant. Intelligent field devices present a wealth of diagnostic data that can be utilised to drive improvements. Continuous automated collection and evaluation of device data supports predictive maintenance strategies. More devices being monitored means there is more data being collected that needs to be processed and analysed. For larger facilities, especially process plants, equipment can be dispersed over wide areas, which presents obvious efficiency benefits from implementing automating condition monitoring.
Most process plants have hundreds of control valves to regulate the flow of process media. Tracking the condition of each valve manually is a time-consuming endeavour that requires a high level of expertise to ascertain valve health and follow-up action. A software tool utilising advanced analytic algorithms is now available that simplifies this monitoring task by providing plant personnel with a fleetwide valve health index along with recommended maintenance actions and recommended timeframes to act. This allows users to prioritise repair and maintenance activities.
Monitoring the health of a growing number of equipment, machines and devices brings with it a few challenges, not least managing the increasing amount and types of data required to analyse, track, trend and support maintenance and operational decisions. Having access to more data is important, but if all an organisation does is dump it into a centralised repository, then positive outcomes are unlikely.
Avoiding this problem is at the heart of Emerson’s Boundless Automation™ vision, which focuses on the implementation of next generation technologies to seamlessly connect intelligent devices and sensors to the edge and into the cloud to drive innovation across all aspects of plant operations. That includes technologies such as wireless asset health monitors, asset maintenance software and device manager data servers, that help to maintain the context around the data so that it is standardised and organised in real-time for use by analytics software. Utilising a data manager device server that supports a broad range of communication protocols prevents data silos and ensures access to device information. Consolidated data can be shared with other software applications beyond the process control system, such as the plant historian, visualisation and dashboard application and advanced analytics software. The aggregation and analysis of this data can provide more insights and help identify trends, such as the most common alerts or issues with specific device types.
- How data analytics can increase manufacturing efficiency
- DCS helps speed new therapies to market
- High-performance HMI design
- Breaking down data silos
- Laser welder enhances manufacturing capabilities
- GenAI-enabled automation for power and water industries
- Visualisation and automation underpin marine demo configuration
- Accurate control for high-precision manufacturing
- Emerson acquires GE's Intelligent Platforms business
- Angle seat valves improve safety, reliability & performance
- IO-LInk Now Included
- As Long As The Wind Blows
- CONDITION MONITORING FOR THE COMMON MAN
- Breakdown Avoided Thanks To Condition Monitoring
- "Try & Buy" Offer For Thermal Imaging Camera
- New generation condition monitoring
- Diagnostics from a distance
- Power plant protection
- Real-time monitoring
- Cost-effective protection for smaller machinery