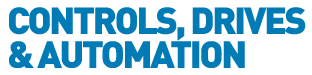
![]() |
Charlotte Stonestreet
Managing Editor |
Home> | AUTOMATION | >Condition Monitoring | >CONDITION MONITORING FOR THE COMMON MAN |
CONDITION MONITORING FOR THE COMMON MAN
06 November 2012
Condition monitoring has been slow to take hold in traditional machine manufacturing. Now, B&R proposes to bring its advantages to the masses
As the power density and functional density of production machines continue to increase, fewer machines are required to produce the same quantity and complexity of products, which lowers production costs and makes machine manufacturing more competitive.
However, this increased efficiency also makes producers more dependent on fewer machines. Each hour of downtime – something which can never be totally avoided – is more expensive.
In a traditional, reactive, damage-oriented maintenance strategy, components are driven to exhaustion and only replaced when they fail. Machine availability is assured by a stock of replacement parts and qualified personnel to fit them at short notice.
Preventive maintenance at fixed intervals, practised widely, makes maintenance downtime more plannable. Here, parts are purchased and replaced although the originals are far from the end of their useful life. But there is no reliable protection against unplanned downtime, such as when certain parts fail prior to the maintenance interval.
THE NEED TO MAINTAIN A STOCK OF REPLACEMENT PARTS IS REDUCED SINCE ONLY THE AFFECTED COMPONENTS NEED TO BE REPLACED
MONITORED PARAMETERS
A better way is to replace the fixed maintenance intervals with condition-dependent, predictive maintenance. This involves scheduling maintenance when changes in monitored parameters indicate impending failure.
Components operate until much closer to the actual end of their useful life, yet the required maintenance can be performed during regularly scheduled breaks in production. The need to main - tain a stock of replacement parts is reduced since only the affected components need to be replaced.
For any of this to be possible, condition parameters throughout the machine must be monitored constantly, and this data must be evaluated correctly. Condition monitoring – which in fact has been around for decades – has been slow to take hold in tradition - al machine manufacturing. The complex mathematics involved expensive computer systems, programmed by experts. Because of this, condition monitoring was limited to systems whose failure would result in immense costs.
Now, moves are afoot to bring condition monitoring into the main manufacturing arena. "Condition monitoring can be based on simple signals and measurement values, such as temperature or pressure, that are collected using X20 or X67 I/O modules,” explains Bernhard Eder, business manager at B&R.
"On top of that, B&R also offers specialised modules such as valve control modules with integrated switching time detection or oscilloscope functions.” Other options for monitoring condition signals are integrated in B&R automation systems: ACOPOS servo drives have built-in motor monitoring and there are PCs equipped with self-diagnostics.
The latest addition to this selection is a new module in the X20 series for vibration analysis.
"The sensor technology used to obtain the signals is indeed important, but the sensors alone are not enough,” explains Werner Paulin, currently B&R’s international sales manager for China. "The key to scheduling maintenance intervals for replacing components at the right time, but not too early, is correct interpretation of the recorded signals. That’s the only way to accurately predict developing problems.” The shrinking scale of microelectronic components has eliminated the need for expensive external wiring. B&R’s analogue input module (X20AI2636) comes as standard with essential functions such as a comparator with hysteresis. The condition monitoring module (X20CM4810) converts signals read from acceleration sensors into more than 70 specific values. This allows even complex oscillation patterns to be monitored on a single channel.
Developers can easily configure which factors should be monitored in B&R Automation Studio without requiring knowledge of complex mathematical functions.
At runtime, significant values are sent to the system CPU and can then be used directly in the application software. "For the first time, machine manufacturers are able to offer condition monitoring not as a premium option, but as a fully integrated standard feature,” states Paulin.
Key Points
• In traditional, reactive, damage-oriented maintenance strategies components are only replaced when they fail
• With condition-dependent, predictive maintenance components operate until much closer to the actual end of their useful life
• The required maintenance can be performed during regularly scheduled breaks in production
- Operator terminal for automotive production
- Master modules
- Hydraulics control software
- Temperature & power measurement modules
- Operator terminal for automotive production
- Internet 4.0, big data & failsafe comms
- Integrated I/O
- 10,000 COMAU robots controlled by B&R
- B&R adds HART modules to X20 I/O series
- Effortless integration
- IO-LInk Now Included
- As Long As The Wind Blows
- Breakdown Avoided Thanks To Condition Monitoring
- "Try & Buy" Offer For Thermal Imaging Camera
- New generation condition monitoring
- Diagnostics from a distance
- Power plant protection
- Real-time monitoring
- Cost-effective protection for smaller machinery
- Bearings & condition monitoring training