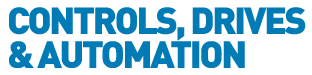
![]() |
Charlotte Stonestreet
Managing Editor |
Home> | AUTOMATION | >Condition Monitoring | >Diagnostics from a distance |
Home> | AUTOMATION | >Monitoring | >Diagnostics from a distance |
Editor's Pick
Diagnostics from a distance
01 November 2013
Remote Diagnostics – the act of diagnosing a given symptom, issue or problem from a distance – is a service which is widely becoming an area of interest for machine builders, system integrators and customers alike, says Paul Wilkinson of Pacepacker Services.
What used to be a value-added feature is quickly becoming a requirement from customers and a competitive necessity – the growth in this service, and its rapid troubleshooting capabilities, is escalating in conjunction with the rising adoption of robotics and automation.
While an automated system should provide a manufacturer with an effective solution which not only suits their products, offers a good payback period and return on investment, it should also have minimal risk attached, and importantly, a good technical backup facility. The latter is becoming increasingly imperative to most, as investing in some of the more complex technology may appear daunting for some and they may have concerns if problems occur as, by its very nature, the more complex the machine, the more difficult it is to determine faults, which might lead to significant downtime, particularly if tight retail timeframes need to be met.
Due to the vast range of robotic equipment readily available today some might say that there has never been a better time to look at making a manufacturing facility more efficient and profitable by investing in packing automation. But what are the key factors that influence machine efficiency? There are many possible answers, however important factors include downtime due to faults, time lost during product changeovers, and reject rates. Fortunately these are all areas where modern technology, such as remote diagnostics, can deliver significant improvements.
Key Points
An automated system should have minimal risk attached and a good technical backup facilityIn the instance of reducing downtime due to a fault, a quick phone call to the support team means that a service engineer, in a remote location, can connect to the system in question to see what’s happening and start diagnosing the issue immediately. Significantly, many types of faults can be diagnosed and corrected this way without the need for the engineer to make a site visit, resulting in big time and cost savings.
Coupled with the fact that broadband connectivity has never been better, some suppliers will even offer remote systems that connect to this medium giving them the ability to view machinery using colour motorised cameras, so that they can visually see exactly what position the machine is in – even while it is in operation. Modern systems should also enable support teams to take control of the machine HMI (touch screen), if fitted, so that they can either work with operators on site to help them through some setting issues or to add new "recipes” remotely should problems be encountered.
While mainly a reactive service, new developments within remote diagnostics will also offer proactive benefits as more and more companies are interested problem avoidance rather than having them solved. Diagnostics now have the ability for the equipment to communicate with you or your managers production statistics including impending issues upstream or downstream that may lead to loss of production time. This feature will be of particular importance to those companies who have multiple lines of automated equipment spread over a large area.
Ultimately, and quite rightly, it is the customer who should reap the benefits of remote diagnostics but a machine builder offering remote diagnostics will also benefit as the service can dramatically increase their competitive edge. It is becoming clearer that remote diagnostics can drastically cut your costs of engineers labour, a reduction in travel, faster response to problems and offer a more efficient use of technical personnel.
While there is a small initial investment to build in the diagnostics and HMI screen and integrate the data to a central control system it can give your system solutions the added edge over a standalone machine without connectivity.
Key Points
- Remote diagnostics can help alleviate problems arising from downtime due to faults, time lost during product changeovers, and high reject rates
- New developments within remote diagnostics offer proactive benefits as interest grows in problem avoidance rather than solving
- Modern systems should enable support teams to take control of the machine HMI (touch screen), if fitted
- Cost effective Cartesian
- Automation awareness workshops
- Easily programmed robotic palletising
- Pick & place robots
- Automation for the people
- LOCAL MP LAUNCHES ROBOTIC PACKING INNOVATIONS
- The food factory cobots are coming … or are they?
- New-generation robotic palletiser
- Cost effective pick & place
- Versatile robot packing solutions
- EXTEND MOBILE INTO MAINTENANCE
- Complete XY Measuring Chain
- MONITORING FOR AUTOMATION
- IO-LInk Now Included
- As Long As The Wind Blows
- CONDITION MONITORING FOR THE COMMON MAN
- Central management of IP-based communication networks
- Breakdown Avoided Thanks To Condition Monitoring
- Magflow Meters
- Gas and Oil Automated