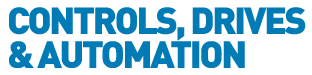
![]() |
Charlotte Stonestreet
Managing Editor |
Home> | IIot & Smart Technology | >Connectivity | >Bringing the edge & cloud together |
Editor's Pick
Bringing the edge & cloud together
06 August 2020
Chris Evans, Marketing & Operations Group Manager at Mitsubishi Electric, looks at why the future of network infrastructure balances edge and cloud capabilities.
Edge and cloud computing technologies might on the surface be seen by some as competing platforms, in fact they are synergistic: by harnessing the strengths of both of them and by distributing the intelligent analysis in the appropriate way, businesses can maximise productivity, efficiency and reduce costs.
Machines and automated systems on the plant floor generate colossal volumes of time-critical data. This data needs to be analysed and processed in “real time” as in the world of automated production, the operating time base is in seconds, milliseconds or even microseconds. Edge technology operates in real time and is able to perform data processing using Advanced Analytics (AA) and Artificial Intelligence (AI) and carry out predictive and preventative modelling.
Additionally, by processing this operational data at the edge, it is possible to reduce the number of data points that need to be processed in centralised, cloud-based locations, resulting in substantial cost savings.
Edge technology can provide seamless data co-ordination between the Operational Technology (OT) and Information Technology (IT) layers. Edge technology that follows the guidelines laid down by the Edgecross Consortium1 will support multiple network protocols enabling data to be collected from plant level assets regardless of which automation vendor equipment is used to control them, thus removing the age old issue, somewhat eased by the adoption of open network technologies, of communicating between disparate automation platforms.
From the Edge to the Cloud
The key to unlocking the power of both edge and cloud based platforms is to decide which operational or business driven task is best suited to either environment. As previously discussed, it is clear that time critical operational tasks and production based analytics sit better in the real time processing capability of the edge layer. However, business drivers such as continuous improvement analysis, whole life cost measurement, overall asset performance analysis, scheduling and the management of costs, whereas still related to production, are non-time critical activities and sit better at the enterprise level, in either a centralised or cloud based environment.
We often hear the term “Digital Twin” when discussing the IIoT and Smart Manufacturing, so where should this reside in our plant topology? The digital twin put into simple terms is a virtual model of a process, product or service, which then allows the logical comparison and analysis of “what we should have” against “what we have actually got.” It could in point of fact, reside either at the edge or the cloud but in true process terms the ideal model is often created at the enterprise level and the logical comparison carried out at the edge. Another way of considering this is, knowledge is developed in the cloud and put into action at the edge.
Therefore, by leveraging the benefits of both edge and cloud computing technologies, businesses can maintain optimal operational efficiencies and drive productivity up.
Limitless possibilities
As arguably it has always done, technology, especially in this space is evolving at a very fast pace. Innovations such as Virtual Reality (VR), Augmented Reality (AR), natural language understanding and speech recognition, not readily associated with automation, could easily migrate to the plant floor for further process intensification.
As these innovative opportunities are fast becoming practical realities, it is important for manufacturers to choose the right solutions partner. By selecting future-oriented automation specialists, such as Mitsubishi Electric, businesses can rely on high-quality technologies and solutions. In this way, it is possible to benefit from these new technologies as soon as they are available and implement Smart Manufacturing strategies effectively to boost operations as well as optimise processes.
- Robots help drive quality control in high-speed inhaler testing line
- Flexible food safe robots feature a greater working area
- New partnership offers a competitive Edge
- Terminal block technology guide
- Shop Floor To Top Floor Connectivity
- Production line efficiency drive
- Robots make the cut
- 25 things you may not know about drives
- TSN-driven IIoT solutions to take centre stage
- Robots help keep people safe in the workplace
- The digital future has begun
- Transmission of Data to Cloud
- Makes IoT available in practice
- Education key to unlocking I4.0
- Complete solution for IO-Link
- Cables for data-intensive IIoT environments
- Smart sensor technologies
- Easing entry to smart manufacturing
- Serial-to-Ethernet server
- How well is your smart farm running?