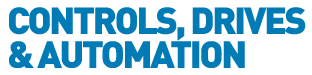
![]() |
Charlotte Stonestreet
Managing Editor |
The smart answer to maintenance management
25 March 2019
Festo broke new ground with the development of its digital maintenance management tool ‘Smartenance’. Product management & marketing manager at Festo, Steve Sands, looks at the process that brought the pioneering technology to market
The digitalisation impetus within Festo coincided with the relocation of the main valves production unit. The brand-new Scharnhausen Technology Plant was conceived with the strong desire to optimise production plant efficiency and reduce all forms of waste. The move made it possible to approach plant maintenance as a greenfield process.
Design Thinking workshop
Development started with an interdisciplinary team working in a Design Thinking workshop. The first ideation for efficiency improvement focused on the smart maintenance topic. The clear target was the elimination of wasteful, error prone, paper-based systems and looked to see how it could look in the new digital world of Industry 4.0. The team created a photo story board of how the day of a maintenance engineer could look in the future. From this kernel, the story board evolved into a MVP – a minimum viable product – that could be developed in a short time and meet the customers’ core needs.
Having a clear picture of both the customer need and how a solution should look enabled the working group to work intensively together. Within a week they were able to develop their thoughts to a point where they could demonstrate a click dummy showing the output of their work. It was clear that ease of use – the user experience – would be critical to the engagement and uptake of the new tool. No one in maintenance would welcome an additional task or process that made life more complicated. Therefore, a thorough market analysis was conducted but failed to identify a suitable product already on the market – so the path was clear for an in-house development.
Once the go-ahead was given the Digital Business Unit set about the internal development of the MVP – to a point where it could be trialled by a customer. After six months the first operating, cloud-based solution was realised and presented at the Hannover Fair. Jakobi Eloxal, specialists in anodising aluminium saw the presentation and were readily engaged as a pilot for the new digital app., willing to test it within a real maintenance environment. Of course, Festo were also able to start testing in-house within our own production plant. The maintenance team users, internally and externally were directly engaged in the further development of the app - so that their specialist requirements could be incorporated in short, agile development cycles.
Previously maintenance plans were created and maintained largely by hand. A paper logbook and tick sheet were kept on the machine with the completion of tasks being acknowledged and signed manually. It was a time-consuming process largely documented using pen and paper.
Cloud-based tool
The concept of Smartenance was to develop a cloud-based tool that could be accessed by members of the maintenance team using mobile devices, tablets or mobile phones. Within the maintenance office environment, supervisors or managers could create, manage and assign maintenance schedules.
For plant operators and the maintenance team this means current maintenance plans and due tasks can be easily seen and if required, viewed remotely anytime, anywhere. Daily and weekly maintenance schedules can be simply viewed with completed, due and overdue tasks clearly indicated. The use of tablets means the full power of digital media is available; complete machine manuals in pdf format, text descriptions, photos drawings and videos are all easily accessible. Once completed tasks can be signed off and clear feedback logged. New images can be simply captured showing what had failed and how it was fixed. In this way experience is shared and the maintenance team can collaborate, between team members, old and new and across shifts.
For production managers all maintenance tasks are visible at a glance through a web browser. All feedback can be analysed; outstanding tasks, time to fix and the status of plant can all be overviewed. New maintenance schedules can be quickly created as new machinery is put into place based upon the manufacturers guidelines. Having all the information in one place also enables the simple export of data for example for external audits, warranty discussions etc.
Maintenance history
There have been some clear changes since the introduction of Smartenance. When approaching a maintenance task, engineers will take the time to check within Smartenance the maintenance history. Armed with the right information, tools and if necessary, spare parts they can make their first approach efficient and effective. As equipment and production lines become more complex this ability to find all relevant information saves time and directly impacts on OEE.
And for the future? The ability to digitally link condition monitoring, predictive maintenance, digital maintenance tools and human-in-the-loop feedback are vital elements to future digital production plants. Learnings can be fed back into the machine learning algorithms so that the AI systems learn, and the quality of their predictions improve.
This means when smart Festo products communicate their status and operating data to the cloud, this information can be interpreted, limits and flags incorporated and then the appropriate information transferred into the digital maintenance system – Smartenance.
- DHL to scale robotics deployment with over 1000 units
- Septentrio starts mass production of GNSS module
- Leading names confirmed for conference
- Metso acquires Tedd Engineering
- Driving Trends & Developments
- Rolls-Royce invests in digital twin technology
- Airbag safety system for robots
- Unlocking the untapped potential of inverters
- Benshaw acquires Aucom Electronics
- New 7-axis cobots
- No related articles listed