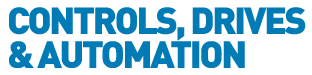
![]() |
Charlotte Stonestreet
Managing Editor |
Home> | INDUSTRY FOCUSES | >Off Shore | >The harsh realities of offshore applications |
The harsh realities of offshore applications
30 June 2014
When it comes to difficult applications, there can be few more arduous than those found in the offshore oil and gas sector. CDA highlights some of the products and technologies that are proving to be worth their salt
With the rise of electrical drive systems, power resistors are now commonly used in offshore drilling, particularly on mobile rigs and marine vessels of all types. When electric motor driven machinery is stopped, the braking energy needs to either be put back into the power supply or dissipated as heat. However, the sheer size and force of drilling in marine applications means power resistors need to be extremely reliable, rugged and durable.
Cressall has extensive experience of designing and manufacturing external braking resistors for the oil and gas industry. The company's comprehensive range of resistors provides compact, robust and cost effective solutions that allow controlled braking and excess energy dissipation in applications such as cable tensioners, remotely operating vehicles like submarines, davits used in lowering and lifting lifeboats and the drilling applications themselves.
Depending on the nature, voltage and installation area of the application they are used in, power resistors can be designed using earth potential Incoloy-sheathed mineral insulated elements, which protect the equipment against physical damage from environmental factors and prevent accidental contact with live voltages. Alternatively, the resistor can be designed using live element technology, which is suitable for operation at more than 2kV by using double and tertiary insulation levels.

When considering the requirements of a power resistor, the cooling method is crucial. Depending on the layout and resources of the system, resistors can be forced, naturally-cooled or water cooled. Forced-cooled resistors have a smaller footprint and use a fan to dissipate more kW in a smaller space. Naturally-cooled resistors are larger but more robust as there is no need to protect a fan. They can also take more overload capacity, meaning they have higher power ratings. Water cooling can be used depending upon whether an existing water cooling system is operational and the extra flow required to cooling the resistors is available.
Power resistors can be used on oil rigs in the main drives that move the drill up and down. In an environment where space is limited and time is money, the rapid deceleration of the drill is essential and drive overvoltage protection is a key part of the process.
A couple of years ago, Cressall started work on an ENSCO 120 project in the North Sea. The company supplied four forced air cooled braking resistors for the drives system of the rig. Each resistor has a 1200kW capacity and the enclosures, fittings and fan are constructed from type-316 stainless steel, which is perfectly suited to outdoor use. As is the case with all Cressall fan cooled resistors, the cable box is IP56 rated and comes complete with an automatic anti-condensation heater, a PT100 temperature sensor and an airflow sensing switch.
Offshore plastics
In an increasing number of mechanically and environmentally challenging applications, such as those found in the offshore oil and gas sector, steel is being displaced by plastic, not least because modern plastics are superior to steel in terms of performance, life and cost-effectiveness.
When steel is exposed to weather extremes and salt spray, it is susceptible to corrosion that greatly reduces its life, it is also heavy and, while strong, it can be bent and distorted if exposed to impact or unusual loads. Plus, systems with moving parts are fabricated from steel need regular lubrication.
Offering an alternative are modern high-performance engineering plastics. Many of these are stronger than steel for a given size and are much lighter. They are also inherently resistant to corrosion and weathering, and the best types are unaffected by exposure to virtually every type of chemical and petrochemical, as well as by exposure to UV light from the sun.
One subgroup of these new engineering plastics – the triboplastic polymers – also provides a complete answer to the lubrication problem. Developed for optimal frictional properties, it is possible to construct systems and products from triboplastics that require no lubrication throughout their working lives, even in the presence of high levels of soiling and contaminants. Not only does this dramatically reduce or even eliminate the need for routine maintenance, it also means that the life of the product can be accurately predicted, as it no longer depends on how well it is maintained.
The properties of these new plastics clearly make them well-suited to use in offshore applications, but there is one further factor that needs to be addressed. Plastics are inherently non-conductive. This makes them, under certain conditions, susceptible to the build up of electrostatic charges, which can lead to electrostatic discharge (ESD). In areas where explosive vapours or gases may be present – that is, those areas where the ATEX Directive applies, as it does to many areas of offshore petrochemical installations – this is potentially a very dangerous situation as it can provide an ignition source.

To provide a solution, plastics such as igumid ESD from igus have been developed. These plastics are made permanently conductive by the incorporation of special additives and are thus able to dissipate electrostatic in a controlled manner, thereby eliminating the risk of sparking. These materials should not be confused with plastics that use applied layers of material to achieve antistatic properties, as such layers are susceptible to damage and in any case have limited effective lives.
These latest plastics are widely used in energy chains, providing articulated support systems for the cables that provide power and communication to the moving elements of systems, such as crane carriages and extending boom conveyors. On offshore drilling platforms, for example, the igus E4.350, which is the largest plastic energy chain in the world, is used to carry large cables and hoses 15 metres up and down during the drilling head stroke, or lateral rig-skidding.
In such applications it is also essential to use cables that are equally well suited to operation in demanding conditions and to satisfy this need, special cables, such as those in the igus chainflex range are now available. These offer excellent flexibility of both their copper cores and their insulation over a very wide temperature range, and are also exceptionally resistant to abrasion and other forms of mechanical damage.
While suited to use with energy chains, these durable cables can also be used alone, as is demonstrated by a recent example on an underwater boring machine, the Vibrocorer VKG-6 produced by Wissenschaftlicher Gerätebau Thomas Schmidt of Rostock in Germany. This drill operates in the most demanding conditions in water depths of up to 200m. For energy supply and to deliver control signals to the drill head, as well as for the transmission of data relating to the penetration depth of the drill, igus chainflex servo cables, with two shielded control pairs, are used.
Maximum reliability
Schaeffler UK has custom designed a set of maintenance-free spherical plain bearings to support a newly constructed process module extension column, which is fixed to the main offshore platform located in the North Sea.
The function of the bearings is to provide a flexible support between the mono column and main rig allowing for movement of the column caused by waves and tidal current relative to the main rig. The bearings, which have a bore diameter of one meter, are designed to transfer these loads from the column to the main rig.
Chris Head, application engineer at Schaeffler UK commented: "After several meetings with the customer and its main contractor for the extension column, it was clear to us that the customer would require a unique design of bearing that offered both a very high level of reliability and zero maintenance. We therefore proposed Schaeffler’s range of ELGES spherical plain bearings, but customised with extra sealing features and low friction sliding layers. These would ensure maximum reliability and zero maintenance.”

Schaeffler’s standard ELGES spherical plain bearing is fitted with only one seal on each side of the bearing, so a special sealing arrangement was discussed with the customer. The custom bearings are therefore fitted with additional seals and designed with an extra sliding layer in the bore. This ensures low friction when the extension column moves relative to the main rig due to the ocean waves.
As Chris Head states: "We offered additional sealing features in the form of a grease layer, which would allow us to lubricate the outermost lip seal, added a special seal, which acts as a barrier for the grease, with another seal to prevent the grease from contaminating the bearing sliding layer.”
The bearings were manufactured according to strict customer specifications, with all bearing materials, components, manufacturing and quality processes all fully traceable.
Alan Stewart, regional sales manager North at Schaeffler UK commented: "This is a first for the oil and gas sector. This project is the first one in which a process module extension column of this type is supported by bearings. The customer deemed the bearings to be a high priority on this project, as their function is absolutely critical in supporting the extension column.”
Pumping heart
In Brazil a petrochemical refinery is turning up the steam to meet increased domestic demand, becoming the first crude oil refinery to be entirely built with Brazilian technology. This includes WEG motors at the heart of one of their core processes.
The eleven three-phase induction motors, suitable for operation in explosive atmospheres will be used to drive the centrifugal pumps feeding water into the cooling towers at the Petrobras Abreu e Lima Refinery in Ipojuca, Pernambuco.

The pumps and motors are to be located in the refining area and will be used to feed the cooling towers associated with the site's main steam turbines. The pumps will operate to provide water for circulation and for cooling the plant and equipment which is critically important within the refining process. The pumps are being supplied by KSB, which has been manufacturing in Brazil for over 50 years.
"These KSB pumps and associated equipment require special motors that offer a high degree of reliability," explains WEG engineer, Marcelo Vedana.
To enhance their reliability the motors are designed to be robust and use the best quality bearings and ancillary components. The windings are precision made and balanced, whilst advanced thermal management ensures cool running.
Explosion proof motors are designed to contain an explosion if it occurs within the motor. This is to prevent the release of explosive gases and to minimize internal sparking within the motor. They are most commonly used in the chemical, mining, textile and petrochemical industries, but also find applications in many other fields.
Not only must an explosion proof motor be designed to reduce the likelihood of exploding, it must also be capable of completely containing an internal explosion so that it does not propagate to the surrounding area. Thus their bodies tend to be more robust than standard motors and to be able to maintain integrity at highly elevated temperatures. They must also resist corrosion and to have flame-tight joints and flanges with minimum tolerances so that hot gases from an internal explosion will cool down before exiting to the wider environment.
Key Points
- Cressall supplies forced air cooled braking resistors for drives system of North Sea rig
- Modern high-performance engineering plastics offer an alternative to steel in offshore applications
- Maintenance-free spherical plain bearings support process module extension column on offshore platform
- WEG supplies explosion proof motors for use in petrochemical refinery
- Architectural vulnerabilities detected in Siemens SIMATIC S7-1500 Series
- How automation is transforming manufacturing efficiency
- Red Dot 2022 for transport robot
- Real-time visibility
- Drones could help save endangered species
- UniversalAutomation.Org welcomes new members
- Government moves forward on advanced trials for self-driving vehicles
- Controls, Drives & Automation to host digital conference
- Digital innovation supporting new business models
- Modular belt solutions