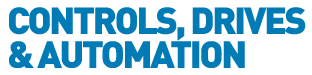
![]() |
Charlotte Stonestreet
Managing Editor |
Editor's Pick
Keep on running
13 January 2022
In this follow up article to Farnell's participation in the CDA Live digital conference, Simon Meadmore, global head of IP&E looks at how to choose the right distributor to keep your production line running

A HUGE amount of engineering effort goes into the implementation of industrial automation applications when deploying new lines or setting up new factories. This work is essential to ensure production lines work as efficiently as possible and meet the requirements of the business and its customers. The decisions taken at this stage of development are incredibly important because they have a long-term impact on the viability of a production line.
However, any subsequent changes that may be required to maintain the efficiency of the line are equally important. Plant managers, production and automation engineers should apply the same level of laser focus to maintenance and upgrades as they did when setting up the original production line. Each discipline has very different requirements for industrial automation installations and professionals must consider different approaches to reap all the benefits of digitally enabled manufacturing.
Understanding setup verses maintenance and upgrade
It’s essential to differentiate between the suppliers chosen to put in a new production line and the preferred suppliers to ensure the line remains up and running. While some suppliers can be the perfect choice for establishing a new factory, plant or production line, other specialised distributors are optimised to keep those systems operational.
Off-the-shelf products are usually sourced from a small number of manufacturers without a great degree of custom engineering taking place when setting up a new production line. The budget is large, with costly equipment purchases required with each supplier. The suppliers themselves are often heavily involved in the setup stage and strategic advice is usually required to ensure the project is implemented successfully. This process occurs over a lengthy period, with all purchases planned well in advance – and if everything is done correctly, it is unlikely there will be any last-minute purchases.
The requirements to maintain or upgrade an existing production line are markedly different. Usually, the work needs to be carried out quickly to minimise any losses caused by equipment downtime. Also, rather than a large financial outlay, maintenance and equipment upgrades usually involve several components provided by several different suppliers. In addition, the plant manager will need tactical advice, such as how a replacement component will work with the existing system, instead of strategic advice. A reasonable degree of custom engineering is usually involved with any upgrade, however with much less supplier involvement than was required at start-up.
Many manufacturers developing products for production lines excel in their deployment and may choose to direct customers to their distribution channel when any issues occur. This reflects how the distribution channel is the optimal choice for the maintenance and upgrade of production lines.
Specialised services & tools to match
When choosing a distribution partner for managing maintenance and upgrades to a production line, there are key characteristics that should be taken into consideration – service level, product range, availability and warranty, as well as scalability.
Service level is essential and can vary considerably depending on whether a distributor is geared up for managing top-quality retrofit projects. Logistics are the core requirement for completing maintenance and upgrades as engineers must receive the required products fast. This is particularly important when parts are being replaced to minimise downtime of a production line. While next-day delivery is crucial, there are only a few specialised global distributors who combine a broad product range with the capability of adhering to short lead times.
Service is also about ensuring the ordering process runs as efficiently as possible. Plant engineers and purchasers of industrial automation systems should work with a distributor that can simplify the procurement process. As a leading distributor of maintenance and upgrade solutions, Farnell offers a suite of value-added services designed to facilitate the ordering and delivery of parts for existing production lines. Customers can easily identify exact or compatible replacement parts and order them quickly using Farnell’s comprehensive resources including images and videos, datasheets, application notes and certifications. Other tools such as e-invoicing simplifies the purchasing process and account management by ensuring invoices are immediately viewable online. Tactical and technical customer support is also offered 24/5 in local language.
In-stock availability & a broad range is critical
The second characteristic that should be considered when choosing a maintenance and upgrade partner is product range, availability and warranty. Spare parts are required by maintenance engineers in the shortest possible timeframe. For this to happen, the distributor must have first-class relationships with global suppliers of all the technologies that will be needed to complete the task. The distributor must also have supplier partners in each of the relevant categories as well as a comprehensive range of in-stock products sourced from franchised suppliers that can be ordered easily.
Farnell meets these requirements by offering solutions from more than 75 suppliers, representing a massive range of products that are immediately available in large quantities and backed by industry-standard manufacturer warranties. Farnell is continually establishing new partnerships with major brands, such as Omega Engineering to satisfy customer demand. As Omega’s exclusive global distributor, Farnell customers have access to a huge global inventory of sensors certified to work with Internet of Things (IoT) ecosystems. Farnell also has the largest market share and availability of single board computers (SBCs), which are increasingly being used to develop new industrial automation and control applications.
Ensuring scalability for future growth
Finally, it is highly likely some form of customisation will be required when upgrading an existing production line to support scalability. It is important for this process to happen as smoothly as possible so that any incremental upgrades do not adversely affect the productivity and efficiency of an operational product line. Businesses must pay special attention when evaluating new hardware and software to enable growth – and the same principle applies to selecting a long-term distribution partner.
Following Farnell’s acquisition by Avnet in 2016, the company has grown exponentially to provide a world-class distribution service and an expanded range of products for new product development, enabling plant engineers to deploy bespoke solutions in the fastest time possible. In addition to this, Avnet’s broad ecosystem can help businesses save time and money when scaling up their production systems by minimising design-to-production time. Farnell customers can take advantage of Avnet’s specialist design services, manufacturing support or life cycle services without having to engage with new partners. Farnell also stocks end-to-end solutions, such as Avnet’s cloud based IoTConnect platform, which enable seamless distribution and analysis of data across the cloud and on-premise systems.
Applying the same degree of rigour
In industrial automation applications, the maintenance and upgrade function should be considered just as important as the design and installation of the original production line. For plant managers and purchasing professionals involved in keeping a facility operating at optimum efficiency, it is essential to select a distribution partner that specialises in maintenance and post-installation support rather than sticking with the provider of the original equipment. Those who can easily access a huge range of products from the world’s leading global suppliers with state-of-the-art ordering systems and customer service support will benefit from the full spectrum of digitisation for manufacturing much faster and maintain competitive advantage.
Key Points
- It’s essential to differentiate between the suppliers chosen to put in a production line and and those to keep it up and running
- Purchasers of industrial automation systems should work with a distributor that can simplify the procurement process
- Businesses must pay special attention when evaluating new hardware and software to enable growth
- Farnell appoints new VP of eCommerce
- Smart sensors whitepaper
- New Industry 4.0 eBook
- Farnell expands range of switches
- Farnell strengthens industrial SBC line card
- Arduino UNO R4 available from Farnell
- Latest products from TE Connectivity available from Farnell
- A landscape of opportunities
- Farnell now stocking INTERCONTEC circular connectors from TE Connectivity
- Fully integrated pressure sensing solution
- No related articles listed