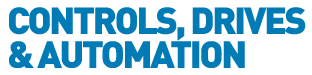
![]() |
Charlotte Stonestreet
Managing Editor |
Home> | IIot & Smart Technology | >Industry 4.0 | >Future trends in Industry 4.0 |
Editor's Pick
Future trends in Industry 4.0
13 April 2023
Industry 4.0 has the potential to impact industrial production in ways we cannot yet envisage. Matt Dentino, Alexandra Rangel and Barry Turner look at the trends

INDUSTRY 4.0 refers to the deployment of digital technologies and automation to transform the performance of manufacturing facilities. Based on three fundamental streams – automation; data technologies; and the integration of machines, software and people – Industry 4.0 makes it easier to optimise production, make better use of assets and boost labour productivity. It is essentially the seamless interaction between software, equipment and people designed to improve the speed and reliability of information that flows between a manufacturer’s systems and those who operate them.
Matt Dentino, Industrial Internet of Things channel manager for Farnell partner Advantech North America, enthuses about the benefits that Industry 4.0 technology can deliver: “Industry 4.0 is the integration of multiple technologies in the industrial space. By integrating relevant, real-time data direct to the decision-makers on the top floor of an organisation, and now into the cloud, we’re blowing the roof off. Industry 4.0 involves machine-to-machine data, KPIs and enhanced insights that offer much tighter operational integration. It can be interpreted in different ways, but at Advantech, we see Industry 4.0 as the integration of the shop floor to the top floor, and beyond.”
High speed connectivity
With the explosion of data from connected machines and devices, connectivity methods will need to adapt to handle the growing amount of traffic. Systems and solutions that produce huge streams of data, such as drones, video cameras with self-recognition, and augmented reality require at least 5G connectivity. Depending on the applications, 5G is expected to play a major role in the development of IoT in the coming years.
And there is good reason for that. Among 5G’s benefits is faster network speed, lower latency, enhanced provisioning to allow more devices to be connected, lower power consumption, and network slicing that will give manufacturing companies their own secure network with guaranteed quality of service (QoS). Network slicing enables different zones in a factory to operate at different speeds and latencies, allowing administrators to reassign valuable bandwidth from non-critical systems to areas that are more data intensive.
Augmented reality
With time being of the essence in a production environment, especially when facilities are offline or out of production due to maintenance or failure, rapid access to maintenance information is vital. Engineers and process operators will benefit from augmented reality, which offers more knowledge in formats that people can readily understand and use. This will enable them to make better, quicker decisions based on factual evidence and hard data.
Advantech’s Dentino says: “I think the augmented reality technology that already exists in the metaverse and in gaming is going to move into the manufacturing space. Already, doctors are training using augmented reality headsets and haptic gloves so that they can perform operations and develop skill sets in an augmented reality-type situation – long before they ever stand over a live patient in a real operating room.”
Easier and faster coding
One of the needs as Industry 4.0 develops is to take account of the changing skill sets of the modern workforce. Older engineers are leaving the industry and taking their skills with them. These skills might include a more traditional approach to programming. This means that simpler ways of programming devices and systems are needed, ones that take account of newer employees being ‘digital natives.’
“An important aspect is the low coding app platform, which has led many software engineers to emphasise the need to get familiar with this low code technology and capability,” says Dentino.
“Where it used to take perhaps a couple of weeks to flesh out an automation routine using ladder logic and getting your programs all set correctly across the line, it can now take minutes with drag and drop configuration technology. That means that even though older skills are fading in the workforce, we will see adoption of automated processes speed up because the part of the coding that traditionally took the longest can now be done automatically much quicker without the specialist knowledge that had previously been required.”
Artificial Intelligence
AI is being used throughout manufacturing in a number of Industry 4.0 use cases, including collecting and analysing data for predictive maintenance; in machine learning to optimise processes and thus improve quality; drive efficiency and energy savings; and in real-time optimisation and tracking of production. It can also be used to train new employees by learning the skills of the company’s experienced machinists, operators and engineers and passing it on in virtual or augmented reality training sessions.
Alexandra Rangel is a National PowerXpert application engineer from the power components division of Eaton, a Farnell partner. “I think we’ll see a lot more of AI,” she says.
“Big corporations like Eaton are devoting a lot of resources to hiring data analytics experts. Artificial intelligence, where you can take this data and not only have a machine figure out what's needed and present options but also make a highly-informed decision with it, will lead to a lot more autonomy in manufacturing plants.”
The autonomy Rangel describes will cut down the time needed to arrive at decisions on improvements and the tasks required to optimise processes. The result will be lower wastage, a faster response to events, and an improved overall quality from more finely tuned processes.
Barry Turner, technical business development manager, Red Lion Controls, emphasises the flexibility that AI will bring. “Red Lion's customers are using AI, for sure,” says Turner.
“Our products can communicate with virtually anything, pulling out data, aggregating it, and then sending it wherever it needs to go, including the cloud. This means that customers using Red Lion's FlexEdge, our HMIs, and our other products that support our Crimson software can pull data from anything on the plant floor, process it using edge device computing intelligence, and then send that information up to the cloud. The cloud can do whatever you need it to do with that data, including using artificial intelligence or machine learning to analyse the effectiveness of existing processes or suggest new ways of doing things.”
Better integration of OT and IT data
Another trend is that the traditionally separate domains of operational technology (OT) and information technology (IT) will become closer. OT systems monitor events, processes and devices, and make adjustments in enterprise and industrial operations, while IT systems are used for data-centric computing.
Industry 4.0. will produce a convergence of mechanical machinery, electromechanical devices and other industrial equipment with the more recent digital world of servers, storage and networking. When properly implemented, this IT/OT convergence will in turn lead to the merger of business processes, insights and controls in a fully coordinated and uniform system.
Red Lion’s Turner adds: “I think the biggest change is going to be acceleration and adoption. As more people understand that Industry 4.0 is all about connecting OT data with IT data to improve a business outcome, we’ll be able to resolve many of the issues associated with the supply chain today.
“We'll figure out ways to take OT data, connect it with IT data, and create better business models. Beyond even that, we'll eventually move into Industry 5.0. Where Industry 4.0 is all about squeezing additional value out of our industrial applications, 5.0 is taking that value and reinvesting it, with interest.”
The need to meet the increasingly divergent needs of customers; compete on both quality and price; be more efficient; cut back on energy use; and deal with an increasingly unpredictable business environment means that manufacturers across industries have to be more flexible and responsive if they are to be successful in an Industry 4.0 future.
If the top floor is receptive to the real-time information they receive about what’s happening on the shop floor, the sky is the limit.
Key Points
- Depending on the applications, 5G is expected to play a major role in the development of IoT in the coming years
- Augmented reality will enable engineers to make better, quicker decisions based on factual evidence and hard data
- The traditionally separate domains of operational technology (OT) and information technology (IT) will become closer
- Power Integrations portfolio expanded
- Simple & reliable USB connectivity
- New Industry 4.0 eBook
- Farnell boosts e-mobility power portfolio
- Farnell expands offering of energy-saving products
- Fully integrated pressure sensing solution
- Survey shows willingness to deploy AI
- Products for automation and Industry 4.0
- Farnell celebrates Earth Day with announcement of environmental award
- Security challenges & opportunities for manufacturing
- Industry 4.0 ready
- Intelligent interlocks
- The digital future has begun
- The smart future of manufacturing
- Partnership integrates freight & warehouse management
- When & where will Industry 4.0 actually happen?
- Education key to unlocking I4.0
- How well is your smart farm running?
- Digitalisation, automation & electrification
- Industry 4.0 guidance platform