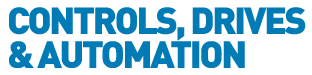
![]() |
Charlotte Stonestreet
Managing Editor |
Home> | INDUSTRY FOCUSES | >Aerospace | >HIGH FLYING AUTOMATION |
HIGH FLYING AUTOMATION
31 October 2012
The recent Automated Britain event, sponsored by Intellect and GAMBICA, included a joint presentation from Siemens and Rolls Royce. CDA Consulting Editor Andy Pye reports on the event, looking at the latest developments and their implications for the aerospace sector
The Automated Britain conference set off in ebullient mood, coinciding as it did with the announcement of Nissan's investment of £125m into Britain, for the unveiling of a new concept model to be manufactured at a state of the art factory in Sunderland.
A good opportunity for keynote speaker Mark Prisk MP, the Minister of State for Business and Enterprise, to present a positive spin in his opening address. Mark Prisk told the conference, "Nissan estimates that the investment will create and safeguard 2000 jobs. That news is, in my book, a real vote of confidence in the UK automotive sector. It vindicates the decision we took to put manufacturing back at the heart of our economic strategy.
"Modern manufacturing requires a continuing commitment, not only to technological investment, but to a culture of innovation. There are several examples here today, so we already have British firms leading the way. Despite difficult spending decisions elsewhere, we took the decision to ring-fence and maintain a science and research budget at £4.6 billion, and to increase capital investment by £500 million.
"We have taken on the principle of the Technology Innovations Centres to ensure that we smooth the path from original research to commercial success. We call them ‘Catapults’ for the simple reason that they are about propelling ideas into commercial ventures. The first is funded at £140 million over the next six years and focussed on high value manufacturing.”
AEROSPACE CHALLENGES
But automating the high volume manufacturing techniques used in aerospace brings different challenges to the automation of high volume manufacturing techniques typical of, for example, the automotive industry. However, it is no less important for that, so how can the Catapult Centres help? "The very first Catapult, in high value manufacturing, and one of the most relevant to the aerospace industry, opened for business in October 2011. Two more Catapults, in cell therapy and offshore renewable energy are on schedule to open by summer 2012. The Catapults in Space Applications, and Connected Digital Economy, were both announced in January and are due to open in the autumn, bringing the total of Catapults announced so far to five. Then on Budget Day, the government revealed plans for two new Catapult centres to improve services and quality of life in cities and develop integrated, efficient and sustainable national transport systems - the Future Cities and Transport Systems Catapult centres.
Catapult centres are intended to create a critical mass for business and research innovation by focusing on a specific technology where there is a potentially large global market and a significant UK capability. These centres will be an important part of the UK's innovation system, making a major long-term contribution to UK economic growth. They will allow businesses to access equipment and expertise that would otherwise be out of reach, as well as conducting their own in-house R&D. They will also help businesses access new funding streams and point them towards the potential of emerging technologies. The new centres will also aim to bridge the gap between universities and businesses, helping to commercialise the outputs of Britain's acknowledged research base.
ACHILLES HEEL
But following the Minister's keynote speech, the stage at Automated Britain was taken by Juergen Maier, managing director of Siemens UK Industry, who forewarned that automation could become UK manufacturing's Achilles heel, if we don't take full advantage of the technologies available in the same way that other European countries do.
"What we are excellent at in this country is process improvement,” he said. "We do not invest in the best automation and capital equipment, such as robotics, which Mr Prisk mentioned earlier. There are two reasons for this. One is that we do have an issue about getting finance, particularly to SMEs, despite numerous initiatives like Project Merlin or the growth funds.
"The other is that in the UK, we have an engineering culture of sweating our assets. We should be investing about €22b into our manufacturing capability in the UK compared to the €57b spent in Germany. We are a good 35% below that in terms of the amount that we invest in automation. We are still at levels of 2009 and nowhere near the pre-recession rates of €18.3b.
AUTOMATED FIBRE PLACEMENT
The UK's National Composites Centre (NCC) has announced the first use of its multi-million pound, twin headed, robotic, automated fibre placement (AFP) machine - the first of its kind in the country. This initial use of the machine is by NCC member, GKN Aerospace, as part of a UK funded and Airbus-led research programme focused on the next generation of super-efficient aircraft wings.
Conventionally, composites are hand laid up from plies which is very time consuming and can introduce problems with variability in the finished product. Automated Tape Lay up has recently been introduced and is being applied currently in the manufacture of aircraft structures.
And the forecast is that we are not going to lift out of it this year, whereas you can see Germany reinvesting, so its competitiveness will be better than the UK's.” It tends to be the larger companies that invest in automation and robotics.
The first study of automation within SME manufacturers has confirmed the relatively low use of automation in UK SMEs and has identified the main barriers to take-up as a lack of knowledge, skills and confidence. The study commissioned by members of the Engineering and Machinery Alliance (including BARA) with support from the Department of Business Innovation and Skills benchmarked UK companies with competitors in Germany, Spain and Sweden.
Chris Buxton, chief executive of the British Automation & Robotics Association (BARA), speaking at Automated Britain, said, "Customers are always looking for product repeatability. Automation and robotics leads to better manufacturing flexibility, and not only do you get improved consistency of quality but also an increased level of quality, because the performance of the machinery employed is repeatable.” Industry needs more and better engineers and engineering managers in industry – and that in turn necessitates a significant cultural shift in the UK, according to Brian Holliday, divisional director at Siemens Industrial Automation and Drives, who co-presented with Chris Biddle, manufacturing systems executive at Rolls-Royce.
PERCEPTION CHANGE
"Siemens ran a survey and found that only one in 10 thought of engineering as important, while four in 10 thought it was dirty and smelly. So we need to change the perception at a very early age,” explained Holliday. Siemens is helping to drive change by encouraging young people into engineering through the University Technical College scheme.
"However, one of the other key challenges in engineering is that engineers in the UK don't have enough of a voice, when it comes to making capital investment decisions.” He cites, for example, transformational automation projects on factories and plants – and the comparison with Germany, in terms of engineering input, is stark. "Also, whereas 20 years ago, automation systems were all about the latest hardware, today it's all about software: digital product design and digital factory design.” Chris Biddle heads the Rolls-Royce Centre of Competence that sits between manufacturing and IT and partners heavily with Siemens on automation systems. He talked about the company's approach to connect the top floor to the shop floor using PLM. In the past, according to Biddle, Rolls Royce ran a multitude of custom systems and interfaces. The goal is now to reduce this to four enterprise systems: ERP (Enterprise Resource Planning), SDM (Service Data Management), MES (Manufacturing Execution Systems) and PLM (Product Lifecycle Management).
Biddle's company is currently working on the CAPP project (Computer Aided Process Planning) and closing the loop from planning to shop floor. "The integration of automation and people is key: our shop-floor systems all link into SAP ERP and Siemens PLM, so there's a fully joined up flow of data from the master model to the product.” Biddle concedes that, for many, the ROI of this kind of development is difficult to assess – and hence some manufacturers' reticence to investing in appropriate systems and automation.
Rolls-Royce is now working with HP and Siemens on the Manufacturing Technology Centre Catapult, which is all about providing a forum for UK manufacturers to accelerate projects from proof of concept to finished goods.
NEXT GENERATION COMPOSITE WING
GKN Aerospace is researching support work within the UK's Next Generation Composite Wing (NGCW) development programme. This is the largest project within the country's National Aerospace Technology Strategy (NATS) and is sponsored by the UK government's Technology Strategy Board (TSB). The programme is led by Airbus and involves a consortium of UK-based academic, public and industrial partners including GKN Aerospace, Umeco, GE Aerospace, Bombardier and QinetiQ. NGCW research and development is focused on ensuring the UK remains at the forefront of global aircraft wing technology and wins a significant share of the growing global aircraft market – predicted to reach 26,000 aircraft sales over the next 20 years.
Early indications suggest that aircraft structures created using this AFP machinery could be some 20% lighter than comparable metal structures, lowering aircraft fuel consumption and emissions. And there is also a potential 75% reduction in material wastage.
Key Points
- Investment is taking place in a network of world-leading technology and innovation centres, called Catapults
- Rolls-Royce is now working with HP and Siemens on the Manufacturing Technology Centre Catapult
- GKN Aerospace is researching support work within the UK's Next Generation Composite Wing (NGCW) development programme
- Robot dog joins BMW Hams Hall team
- Solving the productivity puzzle
- BBC to give all year 7 pupils free pocket-sized computer
- First new ventilators to roll off production line this weekend
- Sophisticated end of arm tooling enhances automated manufacturing
- Ultra-low-power microcontrollers
- Are you ready for the changes to EU Authorised Representatives?
- Maintenance in the era of 4.0 - it's still all about the people
- Amazon invests €400m+ in cutting-edge robotics
- Expanding electrical engineering talent
- Customised Force Sensors
- INTEGRATING MOTORS INTO MACHINE DESIGNS
- £16 MILLION BOOST FOR UK ROBOTICS
- PCR Series drives aerospace power testing
- Benefits For Aerospace Sector
- Ask not what your planet can do for you.....
- maxon motor has QMS EN 9100 certification.
- The new maxon motor magazine is here.
- Automated Passivation
- Demand going sky-high