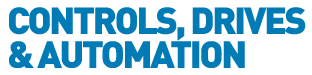
![]() |
Charlotte Stonestreet
Managing Editor |
Home> | INDUSTRY FOCUSES | >Aerospace | >INTEGRATING MOTORS INTO MACHINE DESIGNS |
Home> | DRIVES & MOTORS | >Brushless Motors | >INTEGRATING MOTORS INTO MACHINE DESIGNS |
Home> | INDUSTRY FOCUSES | >Manufacturing | >INTEGRATING MOTORS INTO MACHINE DESIGNS |
Industry Update
INTEGRATING MOTORS INTO MACHINE DESIGNS
06 November 2012
Frameless brushless torque motors allow designers to exploit direct drive technology to create in-house innovative machine designs, essentially out of the box
Traditionally, a designer starts by defining a machine’s movement sequences, and then looks for a suitable motor.
This largely restricts the designer to the motor manufacturer’s specifications in terms of length, diameter, feedback system, bearings and power supply. An alternative is to create an integrated design with encoders or special bearings to suit. The ability to attach the drive directly to the load eliminates bearings, mounting and gears, increases reliability, lowers energy consumption and noise levels, and extends service life.
By using fewer, more effective components, the integrated approach also avoids issues with system compliance, vibration and frequent system maintenance. A hollow shaft direct drive motor drives high inertia loads with large inertia ratios between the rotor and load, with improved dynamics, resulting in a degree of efficiency that is typically 15% greater than with a motor-gear.
This approach is aided by having a large range of available sizes, such as the 14 frame sizes in the KBM series from HT Servo. Diameters range from 60 to 825mm and each frame size comes in three to four lengths, with 150 standard windings. The range provides power from 550W to 18.5kW.
KBM motors can achieve speeds from 105 to 18,600rpm at rated power and require no lubrication.
Special designs are available for aerospace applications, such as the LEMV hybrid airship. KBM motors are configured with a yoke made of cold-rolled and uncoated steel, but can be supplied with stainless steel or other materials suitable for varying environments.
The same applies to the stator sleeve, which comes as standard in uncoated aluminium but can be delivered with stainless steel.
SIMPLE MODIFICATIONS
Other relatively simple modifications include motor windings, which can be optimised to reach the desired speed and torque performances; and rotors which can be delivered with different hole patterns and attachments, or with a smaller inner diameter.
The machine designer is able to fully integrate the motor using the machine’s bearings as the motor’s bearings, avoiding overdetermination.
The machine itself can act as a heat sink, although external air or water cooling can be integrated. Such a setup increases the motor’s available continuous torque, providing faster continuous operation and higher performance.
The KBM series provides maximum torque density with minimal cogging to deliver highly dynamic operation over a broad speed range. The electromagnetic design provides an optimum ratio of torque density to space required.
The smooth rotation, minimal cogging and low total harmonic distortion (THD) significantly reduce latching torques and vibration. Neodymium iron boron magnets provide continuous torque from 1.45 to 3445Nm, and peak torque from 4.91 to 12,812Nm.
A standardised feedback system is based on Hall-Effect sensors – wear-free, contactless position sensors providing commutation signals on the strength of the magnetic field. Pre-set digital latching Hall-Effect sensors are factory-installed. As the feedback system is attached directly to the indexer, measurement takes place directly on the moving part.
HYBRID AIRSHIP USES INTEGRATED DESIGN APPROACH FOR STEERING AND CONTROL
Terrorism, sharply increasing recruitment costs, and energy security are leading military authorities toward lighter-than-air vehicles or hybrid airships.
The Long Endurance Multi-intelligence Vehicle (LEMV) is a state of the art hybrid military airship developed by Northrop Grumman for the US Army. This hybrid air vehicle (HAV) has advantages over fixed-wing unmanned aerial vehicles (UAVs): operating at 20,000ft above sea level, it has 21 days of on-station availability, can fly for a 2000 mile radius and be runway independent. In addition to surveillance, the LEMV can also be used to move heavy equipment, a massive advantage over competing UAVs. The LEMV’s skin – a blend of Vectran, Kevlar and Mylar – is also able to cope with a "reasonable amount of small arms fire.” It gains lift from three different sources. The first is helium, the second is aerodynamic lift with the utilisation of lightweight composite hull designs, and the third is vectored thrust from diesel engines and vector vanes.
HT Servo was selected to supply multiple-axes of motion for the control and steering mechanisms on the LEMV system.
Key Points
- On integrated designs, the ability to attach the drive directly to the load eliminates bearings, mounting and gears, increases reliability, lowers energy consumption and noise levels, and extends service life
- By using fewer, more effective components, the integrated approach also avoids issues with system compliance, vibration and frequent system maintenance
- Customised Force Sensors
- EMC Centre Of Excellence
- Enhanced Performance From Asynchronous Spindle Motors
- Online Customer Support Centre
- HIGH FLYING AUTOMATION
- £16 MILLION BOOST FOR UK ROBOTICS
- PCR Series drives aerospace power testing
- Benefits For Aerospace Sector
- Ask not what your planet can do for you.....
- Brushless Servo Motors