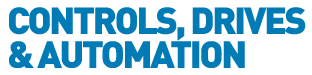
![]() |
Charlotte Stonestreet
Managing Editor |
Home> | IIot & Smart Technology | >Industry 4.0 | >The power of prediction |
Editor's Pick
The power of prediction
15 February 2022
Alexander Hill examines how manufacturers can reduce energy consumption and improve sustainability by implementing a predictive maintenance strategy

MANUFACTURING IS inherently energy-intensive, requiring raw materials to be heated, cut, manipulated, and treated in many different ways to transform them into finished products. For some manufacturing businesses, energy represents up to a third of overhead costs.
Consequently, reducing energy consumption has long been a priority for manufacturers. The principal motivation in improving energy efficiency may be cost reduction, but the carbon emissions associated with generating electricity mean that reducing energy use also has significant sustainability benefits.
Beyond that, governments have begun mandating change, and manufacturers are acting. In the UK, the first major economy to pass net-zero emissions legislation, 20% of UK manufacturers had already taken steps towards reaching the net zero target of 2050 within a year of the bill being introduced . A further 20% had considered what action to take.
The shift to Industry 4.0
The shift to Industry 4.0 and the introduction of more data-driven manufacturing processes offers exciting opportunities to take energy efficiency a stage further.
Instead of viewing energy consumption at a macro level across a facility, manufacturers can now access more granular data at a machine or even a component level.
Such real-time data shows where most energy is being consumed and highlights potential issues before they cause a problem. This enables timely and targeted maintenance interventions to rectify any fault or adjust control settings before machines start to drift out of optimum performance and consume excess energy.
“The key to any successful energy reduction program is first understanding the energy footprint of your business. That requires data. Once you understand when and where energy is consumed in your operations, you can intervene effectively to improve efficiencies,” explains Jim Davison, regional director at Make UK.
How predictive maintenance can help
This constant optimisation is an important way of ensuring machinery is always running as energy-efficiently as possible. Predictive maintenance software does this job continuously, providing information to enhance the understanding of machinery performance and providing a base layer of data against which anomalies can be identified.
Targeting maintenance interventions before faults develop not only means maintaining equipment at optimum efficiency, it also prevents sudden and unplanned downtime. Unpredicted downtime is costly and significantly harms sustainability. Energy is consumed whilst nothing is produced, while restarting certain machines and getting equipment to the correct operating temperature can create a further surge in energy consumption.
Using predictive maintenance technology to improve operational efficiencies and minimise downtime can reduce energy usage in manufacturing operations by up to 15%. This equates directly to reduced costs and reduced carbon emissions.
“Understanding the way machines are operating provides many benefits, including an understanding of precisely where energy is being consumed. Machines running at the most efficient rate and optimal states consume less energy,” explains Rob Russell, CTO at Senseye.
“There are also impacts related to not having to stop and start production lines unexpectedly. If you can keep those machines running for as long as possible in the best consistent states, you’re going to have a direct impact on energy consumption.”
By way of illustration, the predictive maintenance capabilities enabled by Industry 4.0 and implemented by Senseye clients have demonstrated its ability to deliver a:
- 55% increase in maintenance staff productivity
- 50% increase in asset lifespan
- 40% reduction in maintenance costs
- 40% reduction in inventory and waste
Report: Sustainability in Manufacturing
Our report explores the challenges of improving sustainability in manufacturing, the opportunities available, and the bridge built by Industry 4.0 between machine health and sustainability.
We will explore the many ways that real-time data can support business outcomes, leveraging AI-powered industrial analytics to drive the following key sustainability areas with direct reductions in a company’s carbon footprint.
To find out more about how AI powered predictive maintenance helps manufacturers achieve and maintain their sustainability targets, download the full report here.
Alexander Hill is chief global strategist and co-founder, Senseye
Key Points
- Industry 4.0 ready
- Intelligent interlocks
- The digital future has begun
- The smart future of manufacturing
- Partnership integrates freight & warehouse management
- When & where will Industry 4.0 actually happen?
- Education key to unlocking I4.0
- How well is your smart farm running?
- Digitalisation, automation & electrification
- Industry 4.0 guidance platform