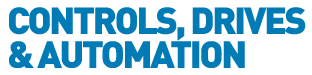
![]() |
Charlotte Stonestreet
Managing Editor |
Home> | AUTOMATION | >Condition Monitoring | >Vibration monitoring for maritime |
Home> | MACHINE BUILDING & ENGINEERING | >Monitoring | >Vibration monitoring for maritime |
Vibration monitoring for maritime
22 February 2024
VIBRATION MONITORING systems are an established tool in helping to achieve optimum safety on board oil tankers and other cargo ships. Leading supplier of turbine supervisory and high integrity protection equipment for maritime applications, Sensonics boasts over 40 years of experience in developing a full range of sensors and API 670 compliant measuring and protection equipment.

So what exactly are Vibration Monitoring Systems, and how do they work?
Today’s vibration monitoring systems are designed to detect and analyse vibrations in various equipment, enabling the early identification of potential mechanical issues, helping to prevent breakdowns and accidents. For example, detecting abnormal vibration patterns in machinery such as; engines, pumps, compressors and generators. Also, identifying mechanical problems like misalignment, imbalance, bearing wear and other issues that can lead to equipment failure. They also provide operators and maintenance engineers with real-time data for timely decision-making and intervention.
What are the key components in Sensonics Vibration Monitoring Systems?
Vibration Sensor, these are strategically placed on machinery to measure vibrations, whilst also detecting vibration intensity, frequency and direction.
Data Acquisition System, which collects data from the sensors and converts it to usable information. Signal Processing and Analysis Software, this collects data which is processed and analysed to determine vibration patterns and deviations from normal conditions. Finally, a Display and Notification Interface, which provides visual displays, alarms and notifications to alert operators and maintenance engineers about abnormal levels
The Benefits?
Implementing vibration monitoring systems delivers several benefits. For example; early detection of vibration anomalies promotes proactive maintenance – before issues escalate. Reduced downtime, timely maintenance based on vibration data can prevent unexpected breakdowns, reducing downtime and associated costs. Preventative maintenance is often more cost-effective than reactive repairs. Safety Enhancement, detecting issues before they lead to catastrophic failures enhances crew safety and prevents accidents. Extending Equipment Life, regular monitoring and maintenance can extend the operational life of machinery. Data-Driven Decision-Making, data collected can inform equipment replacement, or overhaul decisions. Efficiency, machines that run to full capacity produce less emissions and pollution and are much smoother to operate.
Sensonics offers a wide range of proven monitoring systems, which can help to detect potential issues, before things get out-of-hand. By detecting and addressing mechanical issues early our vibration monitoring equipment can make a valuable contribution to efficient operations, helping to prevent accidents and downtime.
- Vibration measurement flexibility provides cost-effective & enhanced protection
- Free vibration monitoring guide
- Free turbine supervisory guide
- Condition monitoring system servicing
- Proximity probe system
- Seismic monitoring & protection
- Fully integrated proximity probes
- Free-to-download overspeed protection guide
- Vibration sensor for low speed rotating machinery
- Critical protection
- Affordable Protection
- WIRE-TO-WIRE
- Easy Integration
- IO-LInk Now Included
- As Long As The Wind Blows
- Monitor Your Compressor Installation With Mobile App
- CONDITION MONITORING FOR THE COMMON MAN
- Breakdown Avoided Thanks To Condition Monitoring
- Increasing machine availability with B&R
- "Try & Buy" Offer For Thermal Imaging Camera