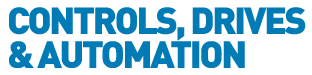
![]() |
Charlotte Stonestreet
Managing Editor |
Home> | INDUSTRY FOCUSES | >Food & Beverage | >Serving up technology |
Serving up technology
10 September 2021
Charlotte Stonestreet looks at what's on the menu when it comes to the latest developments in the food and drink sector
If you ever consider the size of the UK’s various manufacturing sectors, and which constitutes the most sizeable piece of the jigsaw, you would probably recognise that the food and drink sector has got to be amongst the biggest. But did you know that, according to the Food & Drink Federation at least, food and drink manufacturing contributes more to the economy than all other manufacturing sectors, including automotive and aerospace? In fact, in 2018 manufactured food and drink contributed almost £29bn to the economy, or 2.3% of national GVA, and in 2019 the industry had a turnover of more than £104.4bn, accounting for almost 20% of total UK manufacturing.
Of course, the most up to date figures will have been somewhat skewed by the challenges of the global pandemic and Brexit, but beyond these trials there still factors which remain constant, such as the need to meet stringent regulatory requirements and the ongoing quest to increase sustainability.
As Gerard Bush from INMOCO points out, food manufacturers are acutely aware of the need to follow stringent production regulations. It's also important that they follow the obligations of hygiene and safety, not only to ensure the well being of consumers and provide a high quality product, but also to protect their brand and consumer confidence.
As a result of food safety demands, food manufacturers rely on inspection systems. The inspection process is used both to identify and remove imperfect products from the line to ensure batch quality, but also to capture and share data to improve upstream quality control over the long term, as well as enabling downstream product traceability.
Today's demands mean inspection of every single item in a batch, and for food manufacturers to ensure safety but maintain throughput, inspection equipment such as machine vision systems, X-ray, metal detection and weighing sensors are automated to the production line. Imperfect products are then using flaps, pushers and arm diverters. Control over the motion required to actuate and accurately position equipment such as sensor gantries and inspection systems is vital in order for the detection and rejection systems to effectively operate.
Direct drive motor technology is often favoured in these applications because of the high dynamic performance it provides. Not requiring a coupling between the motor and the load, a direct drive motor minimises lag or backlash associated with a device such as a gearbox. Resulting performance advantages include load acceleration, reduced system inertia, and higher precision, as well as reduced power consumption.
Direct drive motors are available with a housing, enabling them to be easily installed into an existing machine. Alternatively, a frameless direct drive motor comprises the rotor and stator alone, meaning that they can be designed into a machine to reduce footprint and improve flexibility.
Kollmorgen specialises in direct drive motor design and the company's engineers combine with partners such as INMOCO, as well as directly with OEMs, to develop motion solutions for applications including food manufacture safety systems. Kollmorgen's framed motor range includes both housed and cartridge models that combine the advantages of direct drive in an easy to install package. Combined with high torque density, control is ensured with an integrated high resolution feedback device.
Alternatively, Kollmorgen's frameless designs are embedded directly within a machine, using the machine's own bearings to support the rotor.
Conveyor belts
In open conveyor systems, food debris can contaminate surfaces and get into crevices and internal support structures over time. While effective cleaning reduces contamination, equipment and components designed specifically for hygiene can take less time, water and cleaning agents to clean and sanitise.
Equipment and components should be appropriately hygiene certified for food. This includes meeting minimum hygiene standards in accordance with industry guidelines such as 3-A, NSF or EHEDG, as well as being compliant with the food contact regulations by the FDA or EU 1935/2004, and other national regulations.
However, in a recent webinar delivered jointly by Bernd Roser from conveyor and power transmission belt specialist Habasit, and Niels Vindsmark from hygienic component manufacturer NGI, Vindsmark explained that "Applying hygienic certified components will not avoid an outbreak, but the more problems you can eliminate and the more certified hygienic components you have in your production facility, the less places you have to look at and worry about if you have an outbreak."
Bernd Roser pointed out that food plant managers should consider three areas when using open conveyor systems: choosing the right conveyor design, choosing the right food contact material to match the process conditions and selecting belts that support ease of cleaning.
A conveyor design supporting sanitary needs is one that provides easy access to belting from all sides, to allow operators to inspect, clean, sanitise and validate effectively. When selecting the right food contact material, it’s important food processors choose a belt that doesn’t change its mechanical properties or wear quickly when regularly exposed to harsh, chemical-based cleaning cycles, at elevated temperatures and with extended contact times.
To support engineers in identifying the chemical resistance of various belt types and materials, Habasit has created a free online tool to help users decide the best belt for them. For applications exposed to very demanding hygiene conditions, Habasit has also developed Super HyCLEAN, a plastic modular belt that minimises the use of rods and hinges to aid cleaning, ideal for applications such as fish and poultry.
Packaging automation
Based in Italy, Martini srl produces high-precision weighing and packaging machines for the food sector. Its new MCRS-VD packaging system enables the packaging of up to 180 packs of pasta per minute. At the heart of the solution is an OMRON NX701 1600 machine controller. This manages the movements of the MCRS-VD. OMRON’s NX-TC Perfect Sealing technology enables the end user to improve the stability of the thermoregulation involved and reduces the costs associated with the use of packaging films.
Martini's Infinity weighing system enables users to dose the pasta quickly and very precisely, with the doses conveyed to the two packaging machines. A digital filter, equipped with the control electronics of each head of the weigher, ensures the accuracy of each dosage.
The MCRS-VD automates all the stages of packaging - including folding, sealing and labelling. The system was created by Martini to meet the growing need for greater speed, efficiency and flexibility from pasta producers all over the world. A key aspect of the structure of the new machine is two continuous, vertical box-motion packaging machines. These are mounted on a segmented belt with intermittent feed and are fed by a double weighing system that uses Infinity - a digital, multi-head model.
The creation of the new system was largely supported by OMRON's automation technology and technical advice. The final performance of the packaging system is managed by the OMRON NX701 1600 machine controller. This coordinates and synchronises the operation of the weighing system with the packaging system. The machine controller was chosen mainly because of its speed capabilities. Thanks to its CPU and available memory, the NX701 1600 can manage up to 128 axes in real time. It supports all of the main industrial communication standards, including EtherCAT (to the field), EtherNet / IP and OPC-UA.
Labour saving
At a time when many businesses are having issues recruiting suitable members of staff, automation help alleviate the problems, as has been the case for a leading UK pork producer which has invested in a UniPAKer robotic crate packer from Brillopak. Having invested heavily in a state-of-the-art line for cutting, portioning and packaging fresh pork into trays, in 2020, the producer turned its attention to the end-of-line crate packing operation. This process was still manual and COVID and Brexit were compounding the issue of labour availability. In fact, the main motivation for automating its crate packing operation wasn’t to reduce head count per se, rather to maximise the potential of existing staff by redeploying them onto more value-adding tasks.
The producer’s brief was for a small footprint system that could pack multiple tray-sealed fresh pork SKUs, ranging in size from 250g up to 1kg, into plastic retail half crates (300x400mm) at a line speed of 66 ppm, with minimal manual intervention. Brillopak proposed a solution with its UniPAKer robot at its centre.
For maximum efficiency, trays have to enter the robot cell in the same orientation. On this line, however, some trays exit the tray sealer narrow-edge leading, whereas others are wide-edge leading, depending on the tooling format. Brillopak addressed this potential issue with the installation of a servo turner that repositions trays after they leave the tray sealer.
The other challenge that this project presented was meeting the customer’s throughput expectations within the available space – the lines in this factory are incredibly close together. A standard single delta robot cell would have fitted into the space, but wouldn’t have been fast enough to make the project viable from a payback perspective. Adding a second robot would have made the system fast enough, but on an unacceptably large footprint.
Brillopak’s solution was to specify its UniPAKer in a dual-pick configuration, in which a single robot performs two picks, then places the packs in the crate, two at a time. This cost-effective and space-efficient option works well for tray-sealed meat packs, which can’t be handled at very high speeds as the film lid may tear. With this approach, the producer’s 60-70 ppm speed target could comfortably be achieved.
Waste handling
Waste is an unavoidable part of the production process at fruit, vegetable and poultry processing facilities. Whether in the form of trimmings, wash residue and by-products, or as a result of off-specification batches, overproduction or expired goods, it must be handled within strict sanitary guidelines and quickly removed from production areas. Not only does this free capacity so that primary processing operations can continue, but waste and by-products can also create an additional revenue stream as animal feed or compost, or to generate renewable energy.
Some waste products are notoriously difficult to handle; large, highly viscous or non-flowable foodstuffs can prove particularly challenging. Some operators still rely on traditional methods to remove them from the production area, and it is not uncommon to find conveyor belts, compressed air systems, vacuums, water flumes, and manual handling via waste containers such as tote bins being used even at large food production factories. These methods can be inefficient, unsanitary and expensive.
The Seepex BTM pump range offers a hygienic and cost-effective alternative. Thanks to an integrated cutting unit that reduces particle size, the BTM effectively chops and pumps in a single operation, reducing the solids volume by up to 60%. This creates a pumpable consistency, without requiring the addition of water, enabling whole vegetables and even entire birds such as DOA or off-specification chickens to be hygienically and efficiently removed off-site.
Key Points
Food manufacturers rely on inspection systems to identify imperfect products and capture data to improve quality control
In open conveyor systems, food debris can contaminate surfaces and get into crevices and internal support structures over time
Some waste products are difficult to handle; large, highly viscous or non-flowable foodstuffs can prove particularly challenging
- VentilatorChallengeUK Consortium
- MAN Group launches MANifesto
- In the frame
- Record growth at Technidrive
- Survey shows net zero skills gap
- UK Government urged to prioritise sustainable AI
- Brexit threat to research & innovation
- New business models & applications; the potential of Industry 4.0
- 3D printed steel smart bridge
- £53 million funding for UK manufacturers
- DEEPER INTEGRATION IN THE FOOD INDUSTRY
- Offering benefits to the food & beverage industry
- Reliable Feeding
- Food & beverage sector benefits
- High hygiene
- Extra reach for high speed applications
- Cut the cost of bearing downtime
- The value of continuous development
- Keeping the milk flowing
- Food handling robots