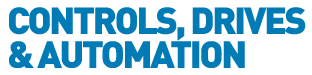
![]() |
Charlotte Stonestreet
Managing Editor |
Home> | IIot & Smart Technology | >Industry 4.0 | >More work ahead for Industry 4.0 |
More work ahead for Industry 4.0
15 August 2023
Recent media talk of Industry 5.0 and even 6.0 is premature, according to Marta Pieńkowska

DESPITE WIDESPREAD support for the use of data in manufacturing, according to research from the World Economic Forum in late 2022 just 39% of manufacturing leaders said that they had successfully scaled data-driven use cases beyond a production process for a single product.
Even so, mentions of Industry 5.0 or 6.0 have already cropped up across the media and in reality, these calls are speculative and premature. While Industry 4.0 is not a nascent concept, there hasn’t been widespread adoption of its core principles and it is still yet to be realised.
It is true that the technologies that power Industry 4.0 can greatly transform the way products are designed, analysed, and produced. But in order to fully capitalise on its potential, manufacturers must first understand and adopt the design principles needed to make Industry 4.0 a reality.
Implementation of Industry 4.0 will take time and this will vary for each business, depending on current levels of adoption and company structure. The needs of manufacturers are naturally varied and unique, with no one-size-fits-all approach to growth or technology adoption. There are also several common challenges when it comes to introducing Industry 4.0 into a business, such as cybersecurity considerations that come with added interconnectivity between systems, or having the right skills in place to introduce new technologies successfully.
Reaching Industry 4.0 starts with understanding and identifying the business goals, before assessing the quality of your data by auditing and analysing your current systems, processes and assets. There are a number of core design principles that provide a framework for creating a more sophisticated and efficient production process.
1. Smart communication
At the core of Industry 4.0 is the interconnectivity and automation of manufacturing through the collection, analysis, and exchange of data between cyber-physical systems. This is called smart communication, which is made possible by advances in machine learning and artificial intelligence. Smart communication provides solutions that can process and analyse large amounts of data at a speed and accuracy beyond human capabilities. These solutions allow for necessary decisions to be made with little or no human assistance.
2. Quality data
Creating a smart network requires high-quality data, as it influences the network’s intelligence and communication. However, data quality is not the same as data quantity. The volume of unstructured data output is at an all-time high. It’s crucial to focus on collecting data that’s relevant rather than use any data that is available, since low-quality data can unnecessarily consume valuable resources.
3. Digital transformation
Making the switch to Industry 4.0 can’t take place without first completing digital transformation. A transition from analogue to digital methods or from digital processes to automated systems throughout an organisation’s entire manufacturing process, so that systems can be interconnected, is one of the first steps and must be done in a considered way. In order to increase reliance on data and base decision-making on it, the process of integrating hardware and software used in production must be thorough and meaningful.
4. Decentralisation
Enabling machines to make simple, routine decisions based on algorithms is another goal of Industry 4.0. It is a crucial step in achieving a production line that is less labour-intensive and less prone to human error. Machines that can recognise patterns and identify errors through artificial intelligence can take on a significant workload, freeing up employees to focus on more complex problems that require human intervention.
What’s next
Adopting Industry 4.0 technologies can lead to increased productivity, profitability, safety and optimisation, as well as improved recordkeeping and traceability. The opportunities that come with successful implementation go well beyond the facilitation and automation of the production process.
Introducing Industry 4.0 means technology plays a part in every step of the development process and predicts any potential challenges ahead. These principles are fundamental in realising the next industrial revolution.
Marta Pieńkowska is product owner at STX Next
- £1b to go to Industrial Strategy Challenge Fund over next 4 years
- Ericsson accelerates 5G for Enterprise with acquisition of Cradlepoint
- Motion control excellence recognised
- Schneider Electric agrees to purchase Invensys
- Merger of PLC, motion control, and robotics predicted to drive global PLC software market
- Automation suite helps to program multi-axis projects
- KC Movers on the move with eCapital
- Tiny magnetic robots could treat bleeds in the brain
- 2022: a watershed year for AI adoption
- Open Industry 4.0 Alliance announced
- Industry 4.0 ready
- Intelligent interlocks
- The digital future has begun
- The smart future of manufacturing
- Partnership integrates freight & warehouse management
- When & where will Industry 4.0 actually happen?
- Education key to unlocking I4.0
- How well is your smart farm running?
- Digitalisation, automation & electrification
- Industry 4.0 guidance platform