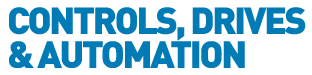
![]() |
Charlotte Stonestreet
Managing Editor |
Home> | IIot & Smart Technology | >Connectivity | >Wireless signals from ceiling lighting for connected manufacturing |
Editor's Pick
Wireless signals from ceiling lighting for connected manufacturing
24 March 2020
WLAN and Bluetooth have limited bandwidth, making conventional wireless communication problematic in the production environment. Addressing this, a team of researchers at Fraunhofer IOSB-INA in Lemgo is working with the Ostwestfalen-Lippe (OWL) University of Applied Sciences and Arts on solutions that involve machines in factory buildings communicating with one another using light pulses. The technology is not new, but now it needs to be adapted for use in industry.
Image: © Fraunhofer IOSB-INA
In the connected factory equipment – such as driverless transportation systems, conveyor belts, engines, robots, sensors, drones, monitoring systems, and mobile devices – are installed and operated in different locations, making a wireless connection indispensable. This has to work smoothly if production downtimes are to be avoided.
In manufacturing, conventional wireless communication is now nearing its limits: WLAN and Bluetooth have a limited bandwidth and the growing number of users, receivers and devices mean the wireless spectrum is becoming overloaded. While 5G technology will alleviate this problem, the researchers at Fraunhofer IOSB-INA in Lemgo, the Industrial Automation Branch of the Fraunhofer Institute for Optronics, System Technologies and Image Exploitation IOSB, believe there is a more effective and license-free way to overcome the challenges of communication in the manufacturing environment. They are taking a different approach and have chosen the visible light spectrum for wireless data transmission. Experts call this technology visible light communication.
“The light spectrum is about 4000 times wider than the entire available wireless spectrum. It ranges from wavelengths of 380 to 800 nanometers,” says Daniel Schneider, a researcher at Fraunhofer IOSB-INA. Together with his colleagues and OWL University of Applied Sciences, he is working on bringing VLC to industry. Research work on the “Visible Light in Production” project funded by the German Federal Ministry for Economic Affairs and Energy (BMWi) – an industrial collaborative research project led by the German Research Society for Automation and Microelectronics (DFAM) – which began one year ago.
Lack of studies on conditions for VLC in the industrial environment
VLC is already used in offices, homes and laboratories and, more recently, it is also being used to implement indoor navigation systems in shopping centers. Factory buildings, however, where there are far more sources of interference, present significant challenges for communications technology which haven’t yet been studied in sufficient depth.
“As an alternative to conventional wireless network access, we will use commercially available, energy-efficient LEDs for our visible light communication solution. The key is being able to establish a system that proves resistant to as much interference as possible,” says Schneider. This kind of system is reliable when coverage problems due to walls, metallic objects, machines and other interfering signals can be overcome.
“Artificial lighting, shadowing effects and reflections can influence data transmission by light. In collaboration with five industrial companies, we carried out measurements to analyse the extent to which they do that, and in which areas and amounts.”
Among other tools for the tests, they used a spectrometer that can be rotated about two axes and that measures the spatial distribution of the sources of interference. The measurement campaign focused on a total of three influencing factors: ambient light, particles and ambient reflections, which experts also refer to as multipath scattering.
Light reflections interfere with data transmission
The tests showed that dust particles pose no problem for optical signals. “Factory buildings are normally well ventilated, so the typical particle concentrations don’t absorb the light signal to any relevant extent,” says the researcher. People and vehicles that move slowly (0.2 m/s) likewise don’t hamper signal quality.
Ambient light, on the other hand, affects the entire optical spectrum. The project partners identified a total of ten models whose lighting conditions influence VLC systems. Among them are welding processes and fluorescent tubes, as well as optical tracking systems, but the effects of these are strictly local and don’t affect the surrounding area. Therefore, according to the test results, VLC systems must be capable of responding adaptively to lighting conditions to minimise these types of interference factors.
The researchers also identified multipath scattering as an interference factor: “A lamp emits light in multiple directions, and this light reaches the receiver via reflections. If these reflections vary greatly, then the light reaches the receiver at different times and with varying degrees of absorption. This distorts the useful signal in the nanosecond range and lowers transmission quality,” the researcher explains. Based on the quantitative measurement results, Schneider and his team are developing environment-adaptive VLC systems for industrial use.
No chance of data theft
VLC not only offers greater bandwidths than WLAN, it also ensures data security. Wireless signals travel through walls, so communications can be intercepted and manipulated outside of factory buildings. This is not possible with light. Potential attackers have no chance here. Another advantage is that VLC makes it possible to wirelessly connect more than 1000 devices with each other.
“Once we establish the ideal design for our VLC system based on our measurement campaign, we will be able to operate more than 1000 devices in one location in a way that saves energy, is secure against interception and is non-sensitive to electromagnetic fields,” says the researcher from Lemgo.
Apart from the ceiling lighting, the required hardware is expected to be limited to an Internet connection and a transceiver connected to the terminal device. The existing demonstrator is currently being tested under real-life conditions in the SmartFactoryOWL in Lemgo. Both, major companies and SMEs, are expected to benefit from the completed system as early as the middle of 2021.
For further information: www.smartfactory-owl.de
- Siemens UK awarded Cyber Essentials Plus (CE+) certification
- Dalsa GEVA 400
- Flexible warehouse automation
- Beyond the manufacturing plant
- Minimising machine safety risk
- Improving supply chain management with blockchain
- AI-driven waste robotics company secures funding
- Wearable system allows engineers to 'see' with their hands
- New digital skills grow North West manufacturing
- Parents support engineering career ambitions
- The digital future has begun
- Transmission of Data to Cloud
- Makes IoT available in practice
- Education key to unlocking I4.0
- Complete solution for IO-Link
- Cables for data-intensive IIoT environments
- Smart sensor technologies
- Easing entry to smart manufacturing
- Serial-to-Ethernet server
- How well is your smart farm running?