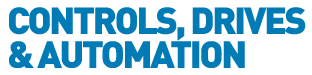
![]() |
Charlotte Stonestreet
Managing Editor |
Home> | POWER TRANSMISSION | >Gearboxes | >Ask the expert: the fundamentals of motor gearbox selection |
Editor's Pick
Ask the expert: the fundamentals of motor gearbox selection
16 December 2021
IAN WILLIAMSON shares expert insight into the important features to look out for when selecting a motor gearbox

In simple terms, a motor gearbox is a mechanical unit consisting of a series of integrated gears, which can alter motor speed and torque. The torque output is inversely proportional to the speed, and gearboxes are mainly applied to motors to increase torque by reducing the speed. While the basic principles remain the same, there are a number of other factors to consider when choosing an appropriate gearbox.
What are the top design specifications to consider when selecting a motor gearbox?
The key to finding an ideally suited motor gearbox is taking a close look at the application it will be put into, right from the beginning of the selection process. This insight allows us to uncover the gearbox’s specific demands and requirements, and this in-depth understanding is what ensures the chosen gearbox, and therefore final product, is successful.
However, there are some essential specifications that must also be studied, including torque, speed, current and operating voltage. These features must be balanced with the customer’s performance aims, preferred price and target quantity to ensure the product works well and is commercially viable.
Customers can choose the best fitted standard gear box to their specific application based on all these factors, but a bespoke solution allows complete tailoring to requirements. Bespoke motor gearboxes can be designed to suit additional factors, such as product space envelope, output drive configuration and product mounting points. Self locking of the motor gearbox and integration of mechanical slipping clutches can also be considered in a bespoke design.
Could you tell us more about the benefits of opting for a bespoke motor gearbox for a product?
When working with a standard component, there is likely to be a compromise on features that means the final product performs well, but not to its maximum potential. A bespoke solution considers all component requirements, and the final product as a whole, right from the beginning of the project.
By tailoring each aspect of the component to the application, more beneficial features can be integrated to tick all of the customer’s boxes in a smaller space. Standard motor gearboxes can require a degree of adaptation to work well in an application, and therefore bespoke gearboxes are often more compact.
Here at EMS, we work closely with our customers from the beginning of the design process to deliver an optimised solution that results in a high performance and uncompromising final product.
Our bespoke services simplify the entire process, reducing the need to procure multiple parts from different sources and providing easier customer assembly and system integration. Detailed technical support from our skilled engineers gives customers a complete solution, from design guidance, to production and beyond.
In what applications is a motor system with a high power density particularly important?
Many of our customers are looking to fit a highly functional unit into a small or complexly shaped space envelope, and this can be achieved with an efficient, high power motor matched with a custom gearbox.
An example of a challenging area to work with is in interior automotive applications, where the space envelope is intertwined with other equipment, making standard components typically unsuitable. This is relevant in car seat AV entertainment systems where screens and displays are deployed via motorised mechanisms.
The systems can open and close at the touch of a button to stow and conceal the media unit from view for aesthetic, safety or security reasons. In the deployment system, the motor gearbox must fit alongside many other components such as the seat chassis, upholstery, media interface and mechanism.
Another beneficial application of high power density motor systems is in the prosthetics industry. The resulting prosthesis must be slim and lightweight to make it comfortable for the user to wear, while also delivering enough power to perform everyday functions, such as opening doors and holding objects.
Small yet powerful motor systems are also advantageous elsewhere in the healthcare industry in stairlifts, for example. In this application, powerful systems are needed to provide sufficient drive to move patients up stairs. However, the system must also be compact so that it can be integrated into the stairlift without negatively impacting its aesthetics or wider performance.
Why is it crucial to choose a motor gearbox that has consistent quality and reliability?
A good quality gearbox ensures the final product performs well in the field. This is especially important in critical sectors such as the medical and healthcare industries, where a performance failure could put the user at risk.
Poor products also impact the manufacturer by disrupting production, causing extra costs and damaging reputation. Investing in a high quality motor gearbox system ensures it will deliver the required loads at the correct speed and reach a sufficient operating lifetime.
EMS develops close relationships with customers to make sure components are understood, designed, tested and validated appropriately before reaching production to safeguard their success.
By only working with reliable suppliers, we ensure our customers are provided with consistently high quality parts that meet product demands. We also use ISO 9001 quality management systems that make sure documentation is well managed from all areas of the business, from project conception to completion.
When should you choose to complement motor gearboxes with an add on, such as an encoder?
There are a number of additional options customers can consider when trying to achieve an optimised solution with maximised functionality. A magnetic or optical encoder, for example, can easily be added to the motor to deliver precise control over speed and positioning.
If accurate sensing is required upstream of the motor or at the output of the gearbox, a bespoke solution can allow integration of the encoder elsewhere in the gear train. Other sensing options include potentiometers for position control or microswitches for endstop detection.
Another potential add on is an electromagnetic brake, which can be fitted to the gearbox to provide holding torque once the power is removed. This allows the system to come to a full stop and hold a position at a reasonably high torque for a long amount of time, and is particularly useful in medical devices.
Mechanical slipping clutches are also a popular option, and are commonly used to protect against overloads. They can be integrated internally or into a product geartrain ― wherever the output of the product is required to slip at a particular overload torque or the internal gear train needs protecting from shock loads.
At EMS, we also manufacture bespoke wiring looms, which allow the motor system to have specific connections that complement existing electrical systems.
Lastly, could you tell us the advantages of working with a UK manufacturer?
Communication is easier between a customer and a local manufacturer, allowing close support throughout the whole project timeline. It also allows physical meetings, when possible, to help the manufacturer fully understand the component’s end application, or to help the customer gain clarity on the production steps needed to make their product.
EMS is UK based, with design engineers at its manufacturing facility in Poole and a sales team around the country. Our design expertise and wealth of experience, combined with our commitment to effective communication with our customers, ensures an optimal motor system is chosen that is ideal for the end application.
EMS is the sole UK supplier of FAULHABER, as well as distributing other high quality brands. Our local manufacturing facility means we can also manage a bespoke product from conception to production, including delivering fully machined prototypes and supporting validation testing.
Ian Williamson is chief design engineer at precision drive system supplier EMS
- Modular belt solutions
- Ai-Da Robot announced as artist in residence at Glastonbury
- Miniaturised 'warehouse robots' for biotechnology applications
- VW's roaming charge
- Space to innovate
- Mapping out automotive developments
- Real-time assistance app
- Final call for women entrepreneurs in STEM to apply for grant
- Ericsson & Porsche rev up for 5G future
- National Engineering & Construction Recruitment Exhibition
- GEARBOX IS CHEAPER TO REPLACE THAN REPAIR
- PLANETARY/SPUR GEARBOXES
- PLANETARY GEARS WELL SUITED FOR RETROFIT
- AGEING WORM GEARS REPLACED BY PLANETARY GEARS IN SEWAGE PLANT
- REHFUSS BRINGS QUALITY AND VERSATILITY TO GEARBOX DESIGN AND SELECTION
- FLEXIBLE COUPLINGS
- GETTING THE BEST OUT OF GEARBOXES
- A Guide to the Selection
- Greater Corrosion Resistance
- Fits existing parameters