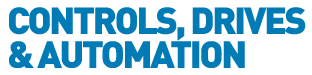
![]() |
Charlotte Stonestreet
Managing Editor |
Home> | MACHINE BUILDING & ENGINEERING | >3D Printing & Prototyping | >3D Printing, CNC Machining or Moulding? |
3D Printing, CNC Machining or Moulding?
14 June 2016
Proto Labs has over 400 CNC mills, more than 70 moulding machines and more than 50 3D printers. So, viewed objectively, which process is most attractive?
Whether the task is to create a first prototype or a do a short production run, choosing the right process can be challenging. At the most general level, computer numerical control (CNC) machining, injection moulding and 3D printing can all be used for short runs, but those technologies each encompass many variations.
For example, stereolithography, selective laser sintering and direct metal laser sintering are all types of 3D printing, but each use different types of materials. Similarly, injection moulding can be used for plastics, silicone rubber or metal.
When presented with so many options, it can be difficult to decide between them. Fortunately, there are several considerations that can help narrow down the choice.
Factors include the number of parts and the material properties that are needed for prototyping or testing. From there, it may go to cosmetics and, of course, parts cost.
Quantity
The number of parts is likely to be the biggest factor when deciding between these three technologies. Obviously, injection moulding is the best bet for several thousand parts, but it is less cost-effective for smaller quantities.
Ordering injection-moulded parts typically involves setup and production fees for the mould, so the total cost, including the mould itself, could be reason enough to choose a different process.
For 20 parts per year, CNC machining or 3D printing come into play provided material properties and cosmetics are satisfactory. 3D printing is typically cost-effective for up to about 50 parts and CNC machining is economical for up to about 200, but typical single-cavity moulds can produce up to 10,000 parts.
Materials properties and cosmetics
As always, there are trade-offs between different production processes in terms of achievable material properties and cosmetics. Secondary processes can go a long way toward improving the cosmetics of a part.
Historically, to perform fit checks and similar tasks, prototyping often involved using different materials compared to the final product. Currently, that same strategy is available thanks to 3D printing technologies, which are ideal for testing fit and form of parts.
Using stereolithography with secondary processes can produce a part that looks like it has been injection moulded. Selective laser sintering provides better material properties than stereolithography, but the process is limited to nylon materials.
With CNC machining it is possible to mill very small spaces. As long as it is horizontal in the machining plane, very small wall thicknesses make it possible to test a "living hinge" in polypropylene. Even with 3D printing, thermoplastic materials like nylon will also work as a living hinge.
Cost
Although it shouldn't necessarily be the deciding factor, prototypes will most likely find 3D printing (or machining if it is possible with the part geometry) will be the best options in terms of cost.
Even for simple parts that do not contain side actions or complicated mould design features, the cost of an injection moulds will be upwards of £1000. Delivery time may also be a matter of weeks in some cases.
It is good advice to design to be manufactured with injection moulding, but then 3D print it. Being able to produce parts that cannot be manufactured using traditional means is usually seen as an advantage of 3D printing, but it can be a double-edged sword if it forces a later redesign of the product.
Key Points
- At the most general level, computer numerical control (CNC) machining, injection moulding and 3D printing can all be used for short runs
- Several considerations can help narrow down the choice, for example the number of parts and the material properties needed for prototyping or testing
- 3D printing is typically cost-effective for up to about 50 parts, CNC for up to about 200; typical single-cavity moulds can produce up to 10,000 parts
- The right chemistry
- ARE YOUR SAFEGUARDS AS SAFE AS YOU THINK?
- All-new mobile browser with complete data encryption
- Ways to reduce waste
- Behind the curtain at ABB’s one-stop shop for drive servicing
- AI-driven efficiency in textile manufacturing
- Construction begins on National Robotarium
- Strategic nuclear robotics partnership
- Six months to comply with new Batteries Regulation
- UK tech that ‘teleports’ humans into robots in finals of global robotics competition