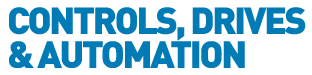
![]() |
Charlotte Stonestreet
Managing Editor |
Home> | INDUSTRY FOCUSES | >Off Shore | >Fathoming out solutions |
Fathoming out solutions
14 January 2014
When it comes to applications in the marine sector, industry is anything but all at sea
Encompassing naval, commercial, leisure and offshore renewable energy sectors, the marine industry has grown exponentially with the event of globalisation and continues to do so. The rapid development of the so-called BRICs countries and the resulting change in social attitudes combined with increased individual wealth has driven supply and demand in terms of resources, technologies, goods and services.
As a result, the marine industry experiences demand for additional tonnage to transport, at one end of the supply chain, bulk commodities, and at the other, finished manufactured goods for export all around the world. Of course, all this results in increased energy needs, and great demand being placed on offshore gas and oil drilling operations along with marine-based renewable technologies.
As in any other sector, companies operating in the the marine sector rely on the latest technology and products to retain a competitive advantage. However, developing products and equipment for use in this sometimes hostile and often inherently unstable environment is not without its challenges.
A recent project carried out at the University of Southampton addressed the issue of vibration experienced by the crew and casualties on inflatable boats used by the Royal National Lifeboat Institution (RNLI).
Ocean waves cause almost all high-speed planing vessels, including inflatable boats (IBs) and rigid inflatable boats (RIBs) widely used by RNLI, to vibrate in a nonlinear manner called boat motion. Boat motion exposes those to vibration, which can potentially cause long and short-term injuries with physiological and psychological effects.
In 2002, European Union directive 2002/44/EU set limits on maximum human exposure to whole body vibration in the workplace – small high-speed planing craft rapidly exceed these limits. Peter Halswell, Engineering Doctorate Student University of Southampton is investigating new strategies to reduce human exposure to these harsh vibrations.
"A RIB with inflatable sponsons has lower response amplitude operators than a RIB with rigid foam sponsons," says Halswell. "We performed a quasi-2D hydroelastic slamming experiment to show that hydroelasticity could change the peak acceleration and impact duration. Our findings indicate that hydroelasticity could reduce boat motion and thus reduce the vibration experienced by the crew. We wanted to study the effects of varying the hydroelasticity to reduce the vibration experienced by the crew and casualties."
The D class inflatable boat used for the study had many inflatable and flexible components, including the hull, sponsons, keel, deck, and deck hinges, which led to a very complex hydroelastic interaction. Each component could potentially affect the hydroelasticity and the vibration experienced by the crew in a number of ways.
Boat motion was measured using 52 sensors through 74 channels attached to various parts of the boat including triaxial accelerometers, rate gyroscopes, strain gauges, string potentiometers and pressure transducers. Analogue signals from these sensors were converted into digital signals and saved during each experiment.

Data logger
"We needed a rugged and reliable data logger that was flexible enough to accommodate a huge variety of sensors. The data logger would experience vibrations up to 20g in 0.1 seconds. It had to be a stand-alone system, meaning no mains power or connection to a laptop, with a minimum sampling rate of 2,500 Hz. Finally, the data logger had to be small enough to fit inside a waterproof case in a restricted space. After careful consideration, we chose the National Instruments (NI) cRIO-9074 embedded controller to meet all these requirements," says Halswell.
"We reconfigured the flexible CompactRIO system to operate as a data logger. We could swap eight input/output (I/O) C Series modules depending on the requirements of the system. The I/O is controlled and synchronised using the onboard Field Programmable Gate Array (FPGA) chip. The conventional method for using a CompactRIO system as a data logger was to feed the output signal from the FPGA chip into a real-time controller in which the data is saved to either the internal flash memory, a USB stick, or an SD card C Series module. However, the SD card module was accessed through the FPGA chip for the highest possible reading/writing speed of 2 MB/s with the real-time controller removed. We did not find any examples of a data logger application in which the real-time controller was not used, so this method is potentially novel.
The benefits include increased reliability, simplified coding and reduced compilation time.
With the wide range of C Series modules, we could wire almost any signal into the CompactRIO system. We chose the NI 9236strain gauge module because it matched the 350 ohm quarter-bridge strain gauges used on the deck and deck hinges. The NI 9234dynamic signal acquisition module was suitable for the triaxial accelerometers and the NI 9205 voltage module was flexible enough to support our other sensors (string potentiometers and pressure transducers). We developed the coding for this data logger usingNI LabVIEW software, which made programming simple and fast."
Specialist bearings
With water power set to make a significant contribution to future supply of renewable energy, Schaeffler is increasingly finding its expertise being called upon to provide custom bearing solutions for water turbines, floating bodies, buoys and oscillating hydrofoils.
The ambient conditions in water and subsea environments place special requirements on the bearings. In these applications, the water itself acts as the lubricating medium. The rolling bearing rings can be made from special, corrosion-resistant steel, with ceramic rolling elements (balls). Bearing cages that guide these rolling elements can also be manufactured from special, water-resistant plastics.

Non-hermetic, lightweight seals can be fitted to the bearings, which enable water to enter the bearing, but which prevent small particles from reaching the rolling contacts.
Schaeffler does not use heavy seals as these can cause too much friction in the bearing. This enables water power plants to operate in a much more energy-efficient manner. It is also not necessary to use lubricating oils or greases, as the rolling bearings are lubricated by water. This results in savings in lubrication costs, as well as being kinder to the environment.
Reliability and low maintenance requirements also play an important role in all water power systems. Once the plants are installed under the surface of the water, access is clearly very limited. To enable maintenance work to be carried out, for example, the plants would have to be lifted to the surface of the water, which is both time-consuming and costly.
The first prototypes of media-lubricated rolling bearings are already in use in pilot projects in North America.
Schaeffler’s latest development for wave, tidal and other marine applications is the ELGOTEX WA series of plain bearings. Originally developed for use as rudder and stabiliser bearings in marine applications, these bearings provide a high load carrying capacity, are maintenance-free and suitable for dry running in fresh water and seawater. The bearings are also certified to MCM-0112 by Germanischer Lloyd.

The design of ELGOTEX WA plain bearings is optimised for slow swivel movements and high forces that are commonly found in wave and tidal energy applications. The bearing is designed specifically for water lubrication and so does not require seals of the type normally found in conventional rolling and plain bearings. As the bearings do not require oil or grease when used in water, there is no risk of lubricant leakage that may contaminate the environment.
Another benefit of ELGOTEX WA plain bearings over alternative marine bearings is its increased load carrying capacity. While the industry standard to date has been a maximum contact pressure of 10 N/mm2, ELGOTEX WA can support loads of up to 25 N/mm2. Germanischer Lloyd has certified ELGOTEX WA for loads of up to 15 N/mm2 in marine applications. This higher power density ensures that the operating life of the bearings can be significantly increased for the same operating conditions. Alternatively, ELGOTEX WA bearings can support higher loads throughout the same operating life. This opens up opportunities for downsizing of new designs and for reducing the number of bearing variants used in a particular application.
The ELGOTEX WA material comprises two layers that are wound onto each other. The internal sliding layer, which is embedded in a resin matrix with fillers and solid lubricants, is made of continuous synthetic and PTFE fibres. The external layer also comprises continuous glass fibres (glass filament) in epoxy resin. A specific winding angle stabilises the layers, significantly increasing the strength of the bush.
This combination of materials enables ELGOTEX WA plain bearings to resist corrosive media and allows a constantly low friction value with low wear and zero maintenance. The bearings have a high radial load carrying capacity, can be used for axial movements, and are insensitive to shocks and edge pressures. Although the bearings are not sealed, if required, they can be supplied with internal seals for additional protection against abrasive contaminants. As well as marine applications, ELGOTEX WA plain bearings are also suitable for use in ocean engineering, hydraulic steel constructions, hydro-electric power plants, water pumps and water turbines
Electro-magnetic clutches
Another company which includes products for use in the marine sector in its portfolio is Engine drives specialist, Centa Transmissions, which has launched a new range of electro-magnetic clutches (EMC) intended to make life easy for designers and manufacturers in the marine industry and other sectors where remote clutching of ancillary drives or equipment is required.
With seven different sizes from 250 to 10600, the Centa EMC can be fitted directly to the engine SAE flange via a torsionally flexible coupling onto the flywheel, or assembled as a stand-alone unit for auxiliary drives, from the non-flywheel end.
Given the correct application factors, all items of drive can be accommodated from high inertia fan drives to hydraulic pumps and its versatile design allows generators or hybrid motors to be added to the clutched or drive end and all PTO requirements can be accommodated with this one compact unit. This means that countless diverse control applications can managed through the specification of this adaptable and flexible clutch.
The benefits of the design, which combines versatility and practicality, include easy integration into any propulsion drive and application, with varying power for large capacity operations. The control electronics are fully sealed in a watertight unit, which means that the EMC can be utilised on all types of applications, including potentially volatile atmospheres and can be operated in all weathers.
Key Points
- NI's CompactRIO reconfigured as a data logger in study of vibration in high-speed planing vessels
- Schaeffler provides custom bearing solutions for water turbines, floating bodies, buoys and oscillating hydrofoils
- Centa Transmissions has launched a new range of electro-magnetic clutches (EMC) intended for the marine industry
- Perfect packaging – a recipe for success
- Mesh network of sensors guides vehicles autonomously
- UK Space Agency to invest £374m per year in European Space Agency
- 'Flexoskeletons' mean insect-inspired robots are faster & cheaper to make
- OF ANIMALS AND THINGS
- Collaboration to accelerate 5G industrial automation
- On the right track for efficiency
- Wearable robot
- Cyber threats to industrial control systems
- Rail industry innovation centre planned