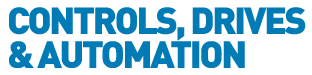
![]() |
Charlotte Stonestreet
Managing Editor |
Home> | AUTOMATION | >PLCs | >PLCs: Constant evolution matches contemporary demands |
Home> | CONTROLS | >PLCs | >PLCs: Constant evolution matches contemporary demands |
Editor's Pick
PLCs: Constant evolution matches contemporary demands
17 August 2015
With the evolution of PLCs being on an upward slope since the early 70s, customer demands are now playing an even bigger role in their capabilities; especially when they are over-designed or under-powered. Heiko Luckhaupt, category marketing manager, Automation & Control, RS Components, reports
There are many laws that govern modern society and many that shape it. Arguably, the one that has had the biggest impact – over the past two or three decades at least – is Moore’s Law. Named after Gordon Moore, the law simply stated that the number of transistors in an IC would double approximately every two years.
The law is starting to waver a little in terms of component count and timescales, but in the interim, this ever-denser IC packaging has helped deliver many of the modern gadgets, machines and technologies that we all seem to now take for granted.
Computational power
Like the consumer market, the industrial arena has not been immune to advances in computational power. Even with longer gaps between product launch windows and longer product service lives, many facets of industry have benefited from a steady trickle of more and more powerful equipment and ancillaries. At the head of the industrial IC-based revolution has been the programmable logic controller (PLC) – so often the processing brains and mainstay of many industrial applications.
Like many contemporary technologies, what we know is the first PLC appeared as a result of a brief from the automotive industry; a 1968 proposal from the automatic transmission division of General Motors to be precise. The first PLC – the winning tender for a suitable replacement for hard-wired relay-based systems – was subsequently developed by Bedford Associates under the still familiar brand name of Modicon, which is now of course owned by Schneider Electric.
Demand for this new technology, which replaced dizzying arrays of individual relays and switches, exploded and many other companies jumped on the bandwagon developing their own models with specific technologies and USPs – all of which steadily grew in capability as IC technology took hold, enabling these suppliers to increase just about every facet of the PLC’s performance.
Over the next few decades, multiple advances were made, many the result of typical product life cycle iterations coupled to new market demands, but jumping forwards to the 90s and it became more and more difficult to choose between high-end PLCs from many of the major vendors; with network architectures and programming languages becoming the primary differentiators.
These were coupled to bespoke USPs, such as a myriad of plug-in option modules, connector types, cable types (and colours), mounting methods and even the physical shape and design of the unit – with easier-to-wire entry points even taking centre stage in the technical press for a short while. At one stage, the number of programming parameters became the next bragging point, swiftly followed by "…the ability to hide 80 per cent of them… making your PLC programming activities even easier”. It was a never-ending cycle of new ideas and functionality all founded on the concept of Moore’s Law delivering the capabilities.
Greater interconnectivity
Moore’s Law didn’t just affect the high end of the market. Simple relays were merged with others to form relay clusters, additional intelligence was then added to create relay-based control modules and then greater interconnectivity, data rates and speeds were deployed, and before we knew it, low-end PLCs had evolved, joining mid-range and high-end PLC families.
It is in the low- and mid-range arenas that some of the most interesting advances have been made in recent years, especially in relation to capabilities. Virtually all of the leading PLC vendors offer higher capability products, which are deployed the world over on production lines and large assembly machines and cells. But the market is changing, not in terms of its need for high-end performance, but instead in terms of a need for agility coupled to what is being dubbed as the next industrial revolution – Manufacturing/Industry 4.0.
With this in mind, many machine designers and end users are looking to create modular, high flexibility, interoperable and ‘migratable’ manufacturing solutions, which can be used in any industrial setting, in any country with the minimum of additional work. For this, they are turning to low- and mid-range controllers to create these modular solutions, which can then be simply plugged into and integrated with a wider plant-wide network – ultimately controlled by higher-end PLCs.
As a result of this extra-capabilities requirement, what we are seeing is a positive move towards greater functionality – an evolution of low- and mid-range controllers (thanks in part to Moore’s Law), which is taking their capabilities into the lower operating envelope of the higher range controllers. This is a real boon for machine designers – especially those that espouse the design-for-purpose mantra. These designers are now able to specify controllers that more closely match their demands. Rather than under using a high-end controller or limiting their capabilities to the top-end performance delivered by previous variants of mid-range controllers, they are instead able to take advantage of the latest range of smaller controllers, without any sacrifice of performance. What is more, it could be argued that these smaller controllers are now, in performance terms, where their larger peers were just a few years ago, but in a more cost-effective package.
Value-add functionality
This greater processing capability is also giving the vendors the ability to add much more useful value-add functionality. Instead of trying to outdo the competition in terms of the number of instruction sets or wiring architecture, they are now listening to the customers and delivering motion, process control and even safety on mid-range devices – opening up an entirely new avenue of operation for more cost effective machine and process control.
Another major development has seen Ethernet and its numerous industrial variants become the primary communications protocol of choice across most vertical industries. This makes it far simpler to leverage the data generated by manufacturing operations and to get a much deeper insight and a "communication tunnel” down to device level – matching one of the demands of Manufacturing 4.0 – the concept of the connected enterprise. These days, the proliferation of Ethernet and Ethernet-based protocols means that almost any device can be visited (securely) on the Web – with their own webpage served up by a mid-range PLC.
PLC development is definitely not static, it will continue to set new benchmarks for some years yet, but it could be argued that we have reached a plateau in terms of function delivery and that there is now very little additional functionality the vendors can add. Sure speeds will increase, data rates will rise and feedback loops will have vital microseconds shaved off them, but what else is there to offer?
Industry-wide standards
The next major step may well revolve around the increased deployment of industry-wide standards, which will allow end users to become PLC agnostic. One example is PackML, a standard originally developed by OMAC (Organization for Machine Automation and Control), which defines a common approach or machine language for automated machines, the idea being to deploy a common "look and feel" across plant floors. Adopted as part of the ISA88 in 2008, PackML is seeing significant take up by many of the world’s largest end users – many of whom created the need in the first place. As a direct result, machine builders and end users are demanding open functionality of their automation suppliers in order to have the ability to effectively hot swap a PLC from one vendor with a PLC from another, safe in the knowledge that their automation/recipe programme will work on both.
If this does indeed become a major driver, we may well see PLC vendors heading back to the heady days of trying to outdo each other on performance terms, however, these will be driven by customer demands, rather than bragging rights, which can only be a good thing.
Key Points
- The first PLC appeared as a result of a brief from the automotive industry for a replacement for hard-wired relay-based systems
- Machine designers and end users are turning to low- and mid-range controllers to create modular solutions
- Evolution of low- and mid-range controllers is taking their capabilities into the lower operating envelope of the higher range controllers
- The next major step may revolve around the increased deployment of industry-wide standards, which will allow end users to become PLC agnostic
- RS Components & Weidmuller in global distribution agreement
- Four supplier solutions for ventilators now available from RS
- Global distribution agreement
- Prioritise reducing the risk
- Unlocking asset data to meet net zero
- Layered defence helps ensure compliance
- RS brings engineering to life
- Exploit the Industrial Internet of Things
- Gravity: The human propulsion flight suit
- AM goes mainstream