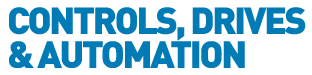
![]() |
Charlotte Stonestreet
Managing Editor |
Home> | MACHINE BUILDING & ENGINEERING | >3D Printing & Prototyping | >AM goes mainstream |
Editor's Pick
AM goes mainstream
20 June 2022
Mike Bray looks at how growth of the additive manufacturing industry is paving the way for mainstream application

ADDITIVE MANUFACTURING (AM) has come a long way since the concept emerged in 1945, and its primitive practice in 1971 – with the first commercial machines following in the 80s. Fast forward almost 50 years and technology and adoption have exponentially increased, not least as a result of significant pandemic-induced disruption – where supply chain issues led industry players to find solutions such as rapid prototyping to fulfil their production requirements.
According to McKinsey & Company, the AM sector had grown by 2020 to a £13.4 billion industry with a 22 per cent annual growth rate. The explosion in its application means this dynamic sector now has more than 200 players developing hardware, software and materials to meet the growing demand. The growth in technology, access to cost-effective solutions and increasing adoption across many industries, providing inspiration, will further its appeal and adoption.
RS recognised how AM was fast becoming relevant to key industry developments including the connected world, sustainability, democratisation of manufacturing and hyper-personalisation. It recently developed a partnership with digital manufacturer Protolabs, as part of its Design and Manufacturing Solutions suite, in recognition of the importance of providing access to services that can facilitate the fast provision of prototypes or parts for a wide variety of applications.
Endless applications
While 3D printing of components in large quantities can be cost-prohibitive, as materials available in a suitable form for processing using AM equipment are expensive, it is ideal for producing frequent low-volume, low-cost custom tools and fixtures. Being able to 3D print components to aid rapid prototyping also gives engineers and designers unrestricted creative freedom, and they can use the rapid prototype testing to develop part that generate more revenue – so there’s no doubt that AM technology has dramatically changed the landscape and industrial space.
A sector that has really capitalised on the advances in AM is the medical devices industry. In the case of products such as implants and prosthetics – where high customisation is required - and aids such as anatomical models for educational use, AM is widely and routinely used. While in the automotive sector, Audi has used the technology to create tools to support manufacturing processes. 3D printers have even been used in old and classic car maintenance, to produce replacement parts that are no longer available.
At RS, we have worked with many customers to help them innovate using 3D printing – including sound level reduction systems provider Preventec, which operates in a competitive industry where standards are changing rapidly. Most of its products include a sonometer with a tip, the quality of which determines the quality of noise measurement and ultimately the safety of users. Using 3D printing services for rapid prototyping enabled them to further develop their product, without the high cost of previous in-house development where conventional machining forms took time and proved expensive.
And in our own business, not only have we used the technology to print rubber-tip grip products for our robot picking tools – increasing efficiency and reducing downtime and costs through the on-site ability to print spare parts as needed – but we also used our DesignSpark engineering platform to help with the production of NHS-accepted protective visors in 2020, when the pandemic spurred high demand that could not be fulfilled. We reached out to the 930,000-strong community, urging members with access to a 3D printer to join the urgent campaign to produce the protective visors to help shield medical and care professionals at high risk of contracting the coronavirus. This was a partner initiative with the non-profit social enterprise National 3D Printing Society (N3DPS), and we teamed up with our RS PRO supplier to donate 400kg of PLA filament to N3DPS from end-of-reel-supplies, to facilitate the production of up to 20,000 visor frames. We also set up a 3D printing farm in Corby, Northamptonshire, to help produce more than 1,000 3-D printed visors per week for the initiative.
Rapid prototyping
An industrial scale AM solution is beyond the reach of many end users. Integrating machines into production workflows and vendor-specific control software into systems used in the wider plant can be barriers for manufacturers who may struggle to even seen how AM can benefit them. Access to the right training and support beyond installation can also be a challenge. However, working with AM service providers is a viable approach for those who want to access the technology. From research conducted across the RS customer base, together with the DesignSpark community, it became apparent to RS that AM services were a real desire for customers: in fact, it highlighted that 3D printing services were in their top three ‘most wanted’. This led to the creation of a partnership between RS and Protolabs which enables us to support our customers in their adoption of AM through our product range, with the major benefit for customers being access to a service that negates equipment investment or skills training.
The Design and Manufacturing Solutions suite service enables users to upload a file, materials are ordered, and then automated systems employed by Protolabs enable fast production of parts – which can be in as little as one day. By utilising an outsourced service such as this from a specialist, high precision is guaranteed. The 3D printing technologies offered by Protolabs include Selective Laser Sintering (SLS), Stereolithography (SLA), Multi-Jet Fusion (MJF), PolyJet (3D printed silicone) and Direct Metal Laser Sintering (DMLS). The parts can be produced in a wide range of plastics and metals.
There are few limitations in complexity of 3D geometries that can be achieved with 3D printing, and in comparison with traditional prototyping methods, waste is significantly reduced. The speed the technology offers enables designers to experiment and still achieve a quicker design cycle phase, with precision, quality and consistency.
But while there is little perceived benefit for many manufacturers to move to AM over conventional manufacturing techniques for the production of regular, high volume parts, the advantage comes when the AM capabilities are used to integrate multiple features into a single component, to reduce the number of parts or process steps. Using an outsourced service allows players to dip a toe to see how the technology could benefit their production.
So while AM has largely been a slow burner since its inception in the middle of the 20th century, the advances in recent years in terms of the availability of faster machines, improved materials, and more intuitive software are factors contributing to the growth of AM as a more viable solution for a wide range of production applications. Manufacturers should embrace the concept in order to capitalise on the opportunities of this ever-evolving and exciting landscape.
Mike Bray is group lead – innovation, R&D and DesignSpark at Electrocomponents
Key Points
- AM has fast become relevant to the connected world, sustainability, democratisation of manufacturing and hyper-personalisation
- AM capabilities can be used to integrate multiple features into a single component, reducing the number of parts or process steps
- Using an outsourced service allows players to dip a toe to see how the technology could benefit their production
- Free 3D CAD Models
- First to market with NFC timing relays
- Distribution agreement
- New Raspberry Pi 3 Compute Module (CM3) designed for professional engineers
- Ex connectors for intrinsically safe circuits
- Desktop 3D printer
- Supporting engineers for 80 years
- RS PRO enclosure range extended
- Making better sense of sensors
- RS Components & Weidmuller in global distribution agreement