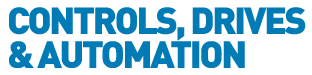
![]() |
Charlotte Stonestreet
Managing Editor |
Home> | AUTOMATION | >Robots | >Robots for machine tending |
Robots for machine tending
30 August 2017
Making good with out of date equipment won’t bring about a more prosperous future for the UK’s machine shops. It’s time to consider smarter technologies. Paul Williams, Sales Manager, ABB’s UK Robotics business, explains how machine tending can involve robot technology
In the UK, the Manufacturing Technologies Association (MTA) estimates an annual turnover of around £1.75 billion within the UK machine tool industry, of which 75% is exported. Within this sector, machine tending is vital to the creation of products.
The opportunity to improve performance is already knocking on the door of the machine tool sector. The big game changer – smart factory technology – is already evident in the automotive industry, where thousands of robots are used in manufacture every day.
Compared to many other countries, the UK is reluctant to adopt robot technologies. The tendency in machine tending is to rely on human operators to manually load and unload, to start and stop machines rather than recognising the potential to reassign these operators and develop their skills to add greater value in other areas of the business. This in turn creates a safer, more rewarding working environment for employees.
Other countries embracing robot technology include South-Korea, Japan, Germany, China, and the USA, where not only the automotive industry enjoys the benefits of smart factory technology, but food, plastics, electronics and others. Just within the machinery industry last year, German manufacturers bought 2,415 robots, compared to the UK’s 216.
Robotics is also a powerful way to help address the growing shortage of skilled staff. As fewer young people opt for Science Technology Engineering and Maths (STEM) career paths and the older generation of engineers retire, the answer lies in deploying modern technology so that fewer operators are required.
Robotic machine tending provides this opportunity. ABB’s machine tending robots can process batches large and small, with program switchovers made simple using an intuitive Human Machine Interface (HMI).
Single operator
Operators need only to load a batch of parts onto a conveyor, select the suitable program and leave the robot to process them. This approach means that just one operator - who need not be an engineer - can supervise many machines.
It is not true that using human operators is the only way to maintain flexibility. A benefit of smart technologies is that data can be quickly communicated between machines when a change is required. The HMI informs each element within the cell when a new program is selected, from the conveyor belt and vision system through to the robot and its end tooling.
Castings PLC is one example of a UK manufacturer that has successfully used robot machine tending to increase flexibility and productivity. The company specialises in the production of 2500 different metal components for vehicles.
Previously, the company’s CNC grinding machines were loaded and unloaded manually, with one operator assigned to handle two machines. An ABB robot machine tender was introduced which incorporated a feedline conveyor belt and imaging system.
Since its introduction, flexibility has increased through the ease of operation which the robot cells offer. Operators can change the cells to handle different component types within 10 minutes. Productivity has also significantly improved with a 50% increase in output. This is due to some of the fettling processes being performed by the robot as well.
Finally, the machine cells need not be supervised as closely as before. Now, one operator supervises four machines allowing improved worker efficiency and safety.
Key Points
- ABB’s machine tending robots can process batches large and small, with program switchovers made simple using an intuitive HMI
- Operators need only to load a batch of parts onto a conveyor, select the suitable program and leave the robot to process them
- The HMI informs each element within the cell when a new program is selected, from the conveyor through to end tooling
- Savings Galvanised
- High performance PLC
- ABB merges drives & motors networks
- Borehole pump costs cut
- Solar inverter helps reduce energy costs
- Touchscreen data recorder
- Extensive motors, drives & controls offering highlighted in new guide
- Maintenance costs cut
- New industrial cobot delivers speed, accuracy and safety
- Bearing Compass makes swap-out easy
- Balls to Gravity
- ROBOTS GIVE FASTER CELL TOOL CHANGE TIMES
- ROBOT FOR DELICATE ASSEMBLY
- NUMBER OF ROBOTS IN UK ON THE RISE
- The future is bright - The future is automation!
- High Demand For Grant
- More Capacity, Less Space
- FREEBIRD - THE THIRD DIMENSION
- PRECISION ROBOT CELL FOR THE PHARMACEUTICAL INDUSTRY
- ROBOT SALES REACH ALL TIME HIGH