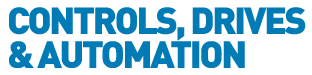
![]() |
Charlotte Stonestreet
Managing Editor |
Home> | IIot & Smart Technology | >Industry 4.0 | >When robots and saws take over the night shift |
When robots and saws take over the night shift
02 October 2024
AUTONOMOUS AND without statutory break times – robots can offer real value to carpentry workshops and boost production. However, acquiring such machines is often associated with high costs. Used machines might offer a viable solution.

Carpentry has been a traditional craft for centuries. Yet, this trade is not exempt from digitalisation and automation through the use of robots. The development of digitalisation in woodworking began in the mid-1970s with the introduction of the first CNC and electronically controlled machines. By the late 1990s, the first high-performance assembly lines with robotic loading had hit the market.
State of the art
A modern cutting station now comprises an automatic board storage system, a pressure beam saw, a handling robot, and several stacking stations. The board storage continuously delivers half-format boards. The program slider seizes the boards, performs precise cuts, and automatically disposes of the offcuts. The robot takes over the processed strips, rotates them as needed, and positions them for further cuts. An integrated labelling station provides each cut with the necessary information. The finished cuts are distributed to various stacking stations, with an automatic switch occurring when a pallet is full.
Unlike a carpenter, the robot does not tire. And the automated cutting station is not bound by statutory break times. Thus, the machines can now take over the night shift. In the dark workshop of Carpentry 4.0, robots and saws perform their precise work and can autonomously produce more than 1,000 boards in a shift.
Efficiency, flexibility, and sustainability: the benefits of automation
Thus, automation and the use of robots offer numerous benefits in carpentry. Furniture and kitchen manufacturers, who often switch between batch and custom production, particularly benefit from the flexibility of modern machines. These technologies enable precise and efficient woodworking, significantly improving the quality and consistency of products – a crucial factor in supply contracts with large furniture stores that demand consistent product quality. Another significant advantage is time savings, as automated machines substantially reduce production time. Depending on the product range and production processes, up to 25% more boards can be produced per shift.
Robots can also help alleviate the skills shortage by taking on tasks that would otherwise require skilled workers, thereby maintaining continuous production.
Last but not least: Another important aspect is sustainability. Digitalisation enables more precise cutting plans, allowing the machines to utilise material down to the last board remnants, resulting in less waste and more economical resource management. Additionally, during production, the offcuts are automatically disposed of through a waste flap in the machine table and sent for recycling.
Drawbacks: expensive and unfamiliar
Despite the many advantages, there are also drawbacks to automation and the use of robots in carpentry. One of the main reasons why many businesses have not yet digitalised as much as they could is the high cost of investment. Particularly for small and medium-sized enterprises, which include most carpentry and box furniture manufacturers, this can be a significant financial hurdle. For woodworkers willing to embrace digitalisation, there are options to acquire high-quality used machines. For example, a HOMAG SAWTEQ b-300 flexTec saw (year 2020) with robotic handling from the production of a Belgian kitchen manufacturer is available for direct purchase from the Surplex used machinery market.
Frequently cited drawbacks include the need for employee training and the risk associated with increased dependency on technology. While the introduction of automated machines and robots does require staff training, it is an investment in the future that pays off quickly through higher productivity and lower error rates. It's true that any new automated technology brings a degree of dependency, and failures can delay production. However, this challenge is not exclusive to automated systems but applies to all state-of-the-art machines and can be minimised through preventive maintenance.
Conclusion: the future of carpentry is digital
The future of carpentry will be shaped by digitalisation and automation, with their advantages increasingly outweighing the drawbacks, gradually eliminating the negatives. Especially for small and medium-sized enterprises, technological progress offers tremendous potential to become more efficient and competitive.
- Engineering recruitment exhibition
- Ask the expert: the fundamentals of motor gearbox selection
- Benshaw acquires Aucom Electronics
- Exotec builds 4000th robot
- Automation of entire 3D printing production process
- Call for urgent action to decarbonise
- Electric & autonomous lighting the way
- UK manufacturers feeling cybersecurity heat
- Humanoid resource management
- Infrared thermal camera performance boosted
- Industry 4.0 ready
- Intelligent interlocks
- The digital future has begun
- The smart future of manufacturing
- Partnership integrates freight & warehouse management
- When & where will Industry 4.0 actually happen?
- Education key to unlocking I4.0
- How well is your smart farm running?
- Digitalisation, automation & electrification
- Industry 4.0 guidance platform