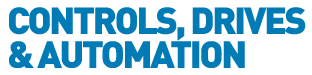
![]() |
Charlotte Stonestreet
Managing Editor |
Home> | AUTOMATION | >Robots | >Cobot innovation resolves redeployment challenge |
Cobot innovation resolves redeployment challenge
11 May 2021
OMRON HAS introduced a fast redeployment solution for machine tending collaborative robots. Incorporating breakthrough fully-integrated landmark functionality, OMRON’s Mobile Cobot Workstation addresses the issue of under-utilisation that can render automation unviable for high product mix manufacturers and SMEs. By enabling cobots to be redeployed on different tasks with minimal reconfiguration, this agile automation solution accelerates return on investment (ROI).
Many machine shops and manufacturers still rely on workers to manually load and unload machines; it’s an area where automation has been slow to take off because conventional fenced robots occupy too much space and restrict layouts. In recent years, cobots have galvanised higher volume operations to improve productivity with safe machine tending, as they can work alongside people without fencing on a very small footprint. However, these units are usually dedicated to a single task, as redeploying them is time-consuming and complex. As a result, cobot investments tend to be cost-prohibitive for low and medium volume operations.
“Cobots are no longer a rarity on the production floor, but they are limited in that they can’t be recalibrated for different tasks without considerable human intervention. This usually means a cobot is purchased to complete one task and is under-utilised – especially by SMEs who do not have the throughput. It is not uncommon for a cobot to be used for as little as 20% of the time, making it a costly investment,” explains Dan Rossek, regional marketing manager at OMRON UK.
Recognising this limitation, OMRON’s engineers have developed an industry first – a mobile cobot workstation that can switch between multiple tasks with minimal reconfiguration. The user can simply move the cobot from station to station, plug-in and ‘play’.
“Our fast redeployment solution allows the cobot to be moved quickly and easily from one machine tending station or task to the next with minimal reconfiguration. This is exciting because if users can maximise cobot utilisation, they can vastly improve both total cost of ownership (TCO) and overall equipment effectiveness (OEE). The bottom line is that instead of buying two or three cobots, they can buy one and redeploy it as needed,” says Rossek.
Using an in-built camera, the intelligent Mobile Cobot Workstation reads the barcode or RFID tag that identifies its workstation location. Thanks to OMRON’s fully-integrated landmark functionality, a sensor enables the cobot to self-position with sub-millimetre accuracy. The cobot then calls up the relevant recipe for the task at that station.
“Ordinarily, the big challenge when moving a robot is that it loses its orientation and has to be repositioned to sub-millimetre accuracy. With our solution, accuracy is compensated by landmark detection so that the cobot retains its repeatability. You simply move it to its new location and the camera references it and recalibrates all of its coordinates,” explains Rossek.
Mobile machine tending without fencing is particularly relevant today, as it can give much-needed flexibility to COVID-compliant factories, where workforce social distancing is required on cramped production lines.
“We have spent a lot of time since the start of the pandemic discussing with manufacturers how they can reduce their workforce density without completely changing their plant and machine layouts. This has resulted in a lot of interest in deploying cobots to reduce the number of operators on a particular station area to enable safe social distancing measures,” notes Dan.
See the the system at Omron’s new virtual exhibition facility online https://industrial.omron.eu/en/news-events/events/virtual-exhibition
- High speed vision
- Medium payload AMRs
- Vision for defect-free production
- Complete solution for IO-Link
- OMRON awarded for sustainability
- UV-C Robot helps fight against COVID
- ROI calculator for mobile and collaborative robots
- Pressure sensors for industrial control and safety applications
- Accelerating human machine harmonisation
- Behind the curtain of automated inspection
- Balls to Gravity
- ROBOTS GIVE FASTER CELL TOOL CHANGE TIMES
- ROBOT FOR DELICATE ASSEMBLY
- NUMBER OF ROBOTS IN UK ON THE RISE
- The future is bright - The future is automation!
- High Demand For Grant
- More Capacity, Less Space
- FREEBIRD - THE THIRD DIMENSION
- PRECISION ROBOT CELL FOR THE PHARMACEUTICAL INDUSTRY
- ROBOT SALES REACH ALL TIME HIGH