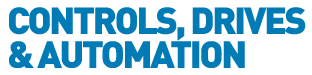
![]() |
Charlotte Stonestreet
Managing Editor |
Home> | AUTOMATION | >Systems | >The case for factory automation amid COVID-19 |
The case for factory automation amid COVID-19
07 September 2020
Robert Brooks, European Industry Marketing Manager F&B at Omron, addresses the coronavirus pandemic, and how it provides an opportunity for manufacturers to rethink outdated processes and procedures and enhance them with concepts such as innovative robotics, sensor technology and holistic automation strategies.
Q: What challenges has the pandemic posed to industrial manufacturers, and how has it made the argument for automation stronger?
A: COVID-19 has posed major challenges to organisations of all types and sizes, with many industries facing significantly reduced consumption and disrupted supply chains, as well as social distancing and tighter safety regulations. Around the world, economies are taking tentative steps to reopen, although it could be some time before a full recovery is realised. In the UK alone, industry reports predict it could take more than five years for the most affected sectors - transportation, warehousing and manufacturing - to get back to 2019-level contributions to GDP.
The case for automation is stronger than ever, offering manufacturers a way to overcome these challenges whilst also improving productivity and efficiency. Companies that want to prepare for the future should be appraising the opportunities and possibilities that elements such as fixed, collaborative and mobile robotics, along with complementary monitoring and control, sensor and vision technologies provide.
Q: What first steps can a manufacturer take in order to automate their manufacturing or processing framework and what are the benefits?
Automation in this context does not only mean robotics or artificial intelligence, but a well-thought-out overall structure of fixed, collaborative and mobile robotics; plus monitoring and control technology, sensors and vision technology tailored to the respective production requirements. In addition, the various stakeholders and market drivers should not be considered in isolation, but as a whole and integrated into the future production strategy.
The first aspect to be considered in this respect are the employees, the workforce perspective of factory automation. Take the food & beverage industry; at the moment, there are millions of people employed in these sectors. This number has an enormous impact on producers in terms of costs, but also primarily in terms of the health and safety of human resources. The pandemic has led to developments such as social distancing and tighter safety regulations that companies need to adhere to. Automation can help in overcoming this challenge while also ensuring security and efficiency in the longer term. A simple example is a cobot or mobile robot solution that can relieve employees from challenging and repetitive tasks so they can focus on more value-added and fulfilling roles.
For example, Omron Solution Partner, LCS Group, carried out a project where it implemented a fully automatic system for the handling of heavy rolls of fabric that weighed up to 30 kilos. These rolls were previously handled by humans. Automating this exhausting task meant that the company could support its employees while also boosting efficiency and productivity. The value of automation is in the mix of humans plus machines, robots and AI - collaboration is key.
While robots show their advantages when it comes to speed and accuracy, human colleagues can take care of business-critical issues, customer communication and daily individual tasks. Regarding the important aspect of ROI, companies should increasingly focus on releasing human labour to do value-added tasks, which is absolutely crucial for producers going forward. Furthermore, automation can fill a lack of experts in the labour market. Collaborative and mobile robots working alongside their human colleagues to assist in lifting or transporting goods and materials while fulfilling tasks employees cannot do because of distance or safety rules.
Q: How can a manufacturer engage their customers, both in the wake of the pandemic but also moving forward?
Product and production quality as well as traceability are further aspects that are increasingly important for both manufacturers and customers alike. Barcode quality is one example that is a key element in many industries and applications. Regulations from international organisations like ISO or GS1 are widely adopted, but in addition there may be further project specific specifications driven by suppliers and customers. This leads to a need for reliable systems and tools that ensure a barcode is correct and readable. Additionally, solutions can be adapted so they can also check pack design aspects and package integrity and completeness.
Information taken from the packaging in the form of codes is also becoming increasingly useful for consumers at the point of purchase. When reading the code at a self-scanning system or in the retailer, they can get information about the product and its components. Furthermore, consumers are increasingly taking an interest in information such as country of origin and of course manufacturers want to engage with consumers via information provided on the item. There is a close link between automation and traceability [both internal and external to the manufacturer], ultimately protecting the brand reputation of the producer and reducing costs. Another simple example is a verification solution using vision systems or RFID which, linked into the production management software, can help to reduce issues connected with false codes or labels.
Q: What other areas of the factory are most susceptible to unpredictable circumstances and how can automation technologies help?
A: Growing consumer demand and changing regulations are all areas that will impact profitability, but catering to new trends becomes a burden for manufacturers when situations such as the pandemic arise and impact profits. As such, being able to adapt and evolve from the factory floor will become even more relevant and important moving forward. Mobile robots and flexible production lines provide companies with valuable support.
One case that provides insight into this movement involves an LCS customer that produces coffee pods. The customer receives requests for very different pods, such as normal plastic or reusable, eco-friendly, different colours and different sizes. By implementing a fleet of Omron’s mobile robots that can manage the fluctuating demand across periods of time or two entirely different requests, LCS was able to help them to achieve a more flexible environment within the plant.
In addition, many solutions still rely on inflexible conveyor systems, whereas mobile robots provide the manufacturer with the flexibility to move stock and consumables to the required locations at the right time. Furthermore, cobots are very easy to train, easy to deploy and transportable, making them a useful companion in achieving more flexibility. Additionally, mobile robots can change routes quickly, dynamically avoiding obstacles or working on different priorities, and can be customised with special add-ons and accessories that allow for even more flexibility.
Q: What advice would you give to companies, particularly SMEs, that might not be able to afford the upfront costs of innovative automation technologies?
A: Certainly, this is an important factor to take into consideration. Upfront investment in automation technologies should be made with a strategic plan that considers a number of economical factors, including: energy efficiency, productivity, labour costs and ROI. Alternatively, leasing is an option that enables manufacturers to allocate their resources more efficiently and effectively.
This is why, in conjunction with established financing partners, Omron Financial Services now provides a wide array of leasing solutions to give manufacturers more choice when deciding how to finance robots on the factory floor. The flexibility that the new leasing options provide is an important consideration in these days of economic and business uncertainty.
To help companies to decide on the best leasing solution for their particular needs, Omron has developed leasing calculators for both mobile robots and collaborative robots. This tool enables a manufacturer to gain a quick idea of the monthly costs of leasing mobile robots or cobots according to the number of robots the company needs and the length of the lease.
This is just one example of how manufacturers can overcome any challenges that arise and respond rapidly to new business opportunities. Smart and connected systems, combining robotics, cobots, vision and sensor technology, as well as strong data collection and analytical capabilities, human machine interaction and full traceability provides real-time insights for a successful and customer-focused future.
- How can flexible production help UK manufacturers adapt to a changing market?
- Condition monitoring devices
- Software for accelerating AMR fleet management
- Let’s Build It - discover innovation in panel building
- Advanced motor condition monitoring devices
- Ensure maintenance isn't a pain in the asset
- Automation platform expanded
- Integrated controller makes mass personalisation a reality
- Advanced information and safety control
- Stable detection
- SWISSLOG SECURES MAJOR ORDER
- IMPROVED PERFORMANCE & RELIABILITY
- Engine Facility
- BULK AUTOMATION
- Integrated Packaging Solutions
- INTEGRATING ELECTRIC AND PNEUMATIC CONTROLS
- Rockwell Automation expands Midrange system portfolio
- Yokogawa joins Friends of the Supergrid
- Festo extends reach of VTUG and MPA-L valve terminals
- Siemens extends TIA Portal engineering framework